Chinese Professional Nodular Iron Shell Mold Casting - Steel Sand Casting Foundry – RMC Foundry Detail:
Steel Sand Casting Foundry from China with Custom and CNC Machining Services.
Sand casting is one of the most popular and simplest types of casting, and has been used for centuries. Sand casting allows for smaller batches than permanent mold casting and at a very reasonable cost. Not only does this method allow manufacturers to create products at a low cost, but there are other benefits to sand casting, such as very small-size operations. Sand casting also allows most metals to be cast depending on the type of sand used for the molds.
Ideally suited for complex geometries, sand casting takes advantage of sand’s inherent compactability, refractory nature and recyclability to produce relatively inexpensive molds. Sand casting requires a relatively low investment and allows for quick tooling development and part changes at a reasonable cost. As a result, it’s well suited for working through the evolution of designs and for lower volume casting parts.
In RMC casting foundry, we uses sand casting for parts made of grey iron, ductile iron, carbon steel, steel alloys or aluminium. Part weights can vary from tens of grams to hundreds of kilograms. The applications of sand casting parts range from small parts like gears, pulleys, connecting rods, brackets and propellers to large components such as pump components, pipeline parts, manifolds, engine blocks, cylinder heads and transmission cases.
We ensure our customers have the highest quality parts on time and on budget by providing full turn-key services, including assistance with design and material selection through heat treatment, machining, surface finishing, assembly and painting. Apart from the green sand casting processes, we are also using other casting processes, such as pre-coated resin sand casting (hot shell and core molding), furan resin sand casting, investment casting, lost foam casting and vacuum casting.
Raw Materials Available for Sand Casting
• Cast Steel: Carbon Steel, Low Alloy Steel, Stainless Steel, Duplex Stainless Steel
• Gray Cast Iron and Ductile Cast Iron: GJL-100, GJL-150, GJL-200, GJL-250, GJL-300, GJL-350; GJS-400-18, GJS-40-15, GJS-450-10, GJS-500-7, GJS-600-3, GJS-700-2, GJS-800-2
• Aluminium and Their Alloys
• Other Materials and Standards on request
Capabilities of Sand Casting:
• Max Size (by automatic molding line): 1,500 mm × 1000 mm × 500 mm
• Max Size (by handle molding): 1,000 mm × 800 mm × 500 mm
• Weight Range: 0.5 kg – 500 kg
• Annual Capacity: 7,000 tons – 8,000 tons
• Tolerances: On Request.
Main Production Procedure
Patterns & Tooling Design → Making Patterns → Moulding Process → Chemical Composition Analysis → Melting & Pouring → Cleaning, Grinding & Shot Blasting → Post Processing or Packing for Shipment
Sand Casting Inspection Capabilities
• Spectrographic and manual quantitative analysis
• Metallographic analysis
• Brinell, Rockwell and Vickers hardness inspection
• Mechanical property analysis
• Low and normal temperature impact testing
• Cleanliness inspection
• UT, MT and RT inspection
Post-Casting Process
• Deburring & Cleaning
• Shot Blasting / Sand Peening
• Heat Treatment: Normalization, Quench, Tempering, Carburization, Nitriding
• Surface Treatment: Passivation, Andonizing, Electroplating, Hot Zinc Plating, Zinc Plating, Nickel Plating, Polishing, Electro-Polishing, Painting, GeoMet, Zintec
• CNC Precision Machining: Turning, Milling, Lathing, Drilling, Honing, Grinding,
General Commerial Terms
• Main work flow: Inquiry & Quotation → Confirming Details / Cost Reduction Proposals → Tooling Development → Trial Casting → Samples Approval → Trial Order → Mass Production → Continuous Order Proceeding
• Lead time: Estimatedly 15-25 days for tooling development and estimatedly 20 days for mass production.
• Payment Terms: To be negotiated.
• Payment methods: T/T, L/C, West Union, Paypal.
Product detail pictures:
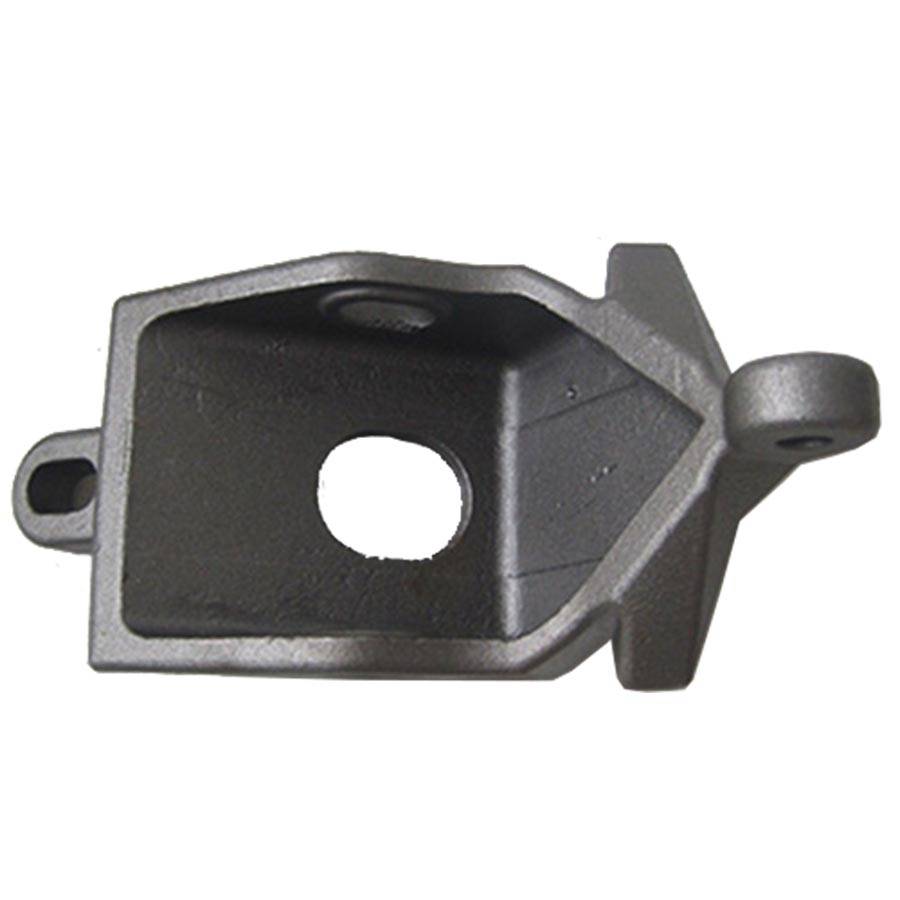
Related Product Guide:
We will make just about every exertion for being excellent and perfect, and speed up our actions for standing during the rank of worldwide top-grade and high-tech enterprises for Chinese Professional Nodular Iron Shell Mold Casting - Steel Sand Casting Foundry – RMC Foundry, The product will supply to all over the world, such as: Austria , Netherlands , Rio de Janeiro , Our company insists on the purpose of "takes service priority for standard, quality guarantee for the brand, do business in good faith, to offer skilled, rapid, accurate and timely service for you". We welcome old and new customers to negotiate with us. We are going to serve you with all sincerity!

The factory workers have a good team spirit, so we received high quality products fast, in addition, the price is also appropriate, this is a very good and reliable Chinese manufacturers.

-
China Factory for Cast Steel Foundry - Stainle...
-
PriceList for Brass Vacuum Casting - Vacuum Ca...
-
Trending Products Zinc Alloy Casting - Metal P...
-
High reputation Alloy Steel Lost Wax Casting Pr...
-
High definition Gray Iron Casting Products - C...
-
Hot sale Factory Alloy Steel Casting Manufactur...