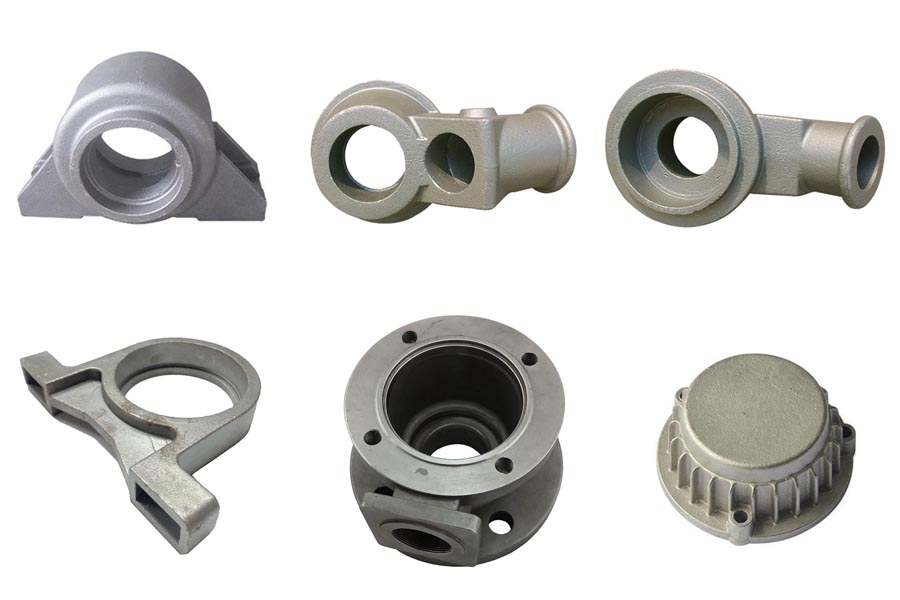
Steel castings the a combination of casting molding process and steel material metallurgy. They can not only have complex structure that are difficult to obtain by other forming processes, but also maintain the unique properties of steel, so the steel casting parts have a high important position in engineering structural materials. In most foundries, steel castings are mainly produced through these several casting processes: investment casting, lost foam casting, vacuum casting, sand casting and resin coated sand casting.
Steel castings are also very extensive in terms of metal and alloy selection. For example, the cast steel covers a wide range of alloys such as low carbon steel, medium carbon steel, high carbon steel, alloy steel, high alloy steel, stainless steel, duplex stainless steel, precipitation hardening stainless and other special steel alloys.
Carbon steel and low-alloy steel have high strength, high toughness and good weldability, and can adjust mechanical properties in a wide range through different heat treatment processes. They are the most widely used engineering structural materials. For some special engineering conditions, such as abrasion resistance, pressure resistance, heat resistance, corrosion resistance and low temperature resistance, there are various high alloy steels with corresponding special properties to choose from.
Forged steel parts also have their own advantages, such as higher strength and fewer internal defects. However, compared with forged steel parts, the advantages of steel castings are also obvious. In summary, the advantages of steel castings are mainly manifested in design flexibility. Specifically, this flexibility is manifested in the following aspects:
1) The structure of steel castings has high flexibility
The technical staff of the steel casting plant can have the greatest design freedom in the shape and size of the steel castings, especially the parts with complex shapes and hollow sections. The steel castings can be manufactured by the unique process of core assembly. At the same time, the forming and shape change of steel castings is very easy, and the conversion speed from drawing to finished product is very fast, which is conducive to rapid quotation response and shortened delivery time.
2) The metallurgical manufacturing of steel castings has high adaptability and variability
In general foundries, steel castings can have many different chemical compositions to choose from, such as low carbon steel, medium carbon steel, high carbon steel, low alloy steel, high alloy steel and special steel. Moreover, according to the different performance requirements of the steel castings, the foundry can also select the mechanical properties and use performance in a larger range through different heat treatments, and at the same time, it can also obtain good welding performance and machining performance.
3) The weight of steel castings can vary within a wide range
Steel castings can achieve a minimum weight of a few grams, such as through investment casting. The weight of large steel castings can reach several tons, dozens of tons or even hundreds of tons. Moreover, steel castings are easy to achieve lightweight design, which not only reduces the weight of the casting itself (which is particularly important in the passenger car, train, and ship industries), but also reduces the cost of the casting.
4) Flexibility of steel casting manufacturing
In the metal forming process, mold cost is a factor that cannot be ignored. Compared with forged steel parts, steel castings can adopt different casting processes according to different demands. For single-piece or small batch castings, wooden patterns or polystyrene gasification patterns can be used, and the production cycle is very short. For steel castings with relatively large demand, plastic or metal patterns can be used, and appropriate modeling techniques are used to make the castings have the required dimensional accuracy and surface quality. These features are difficult to achieve with forged steel parts.
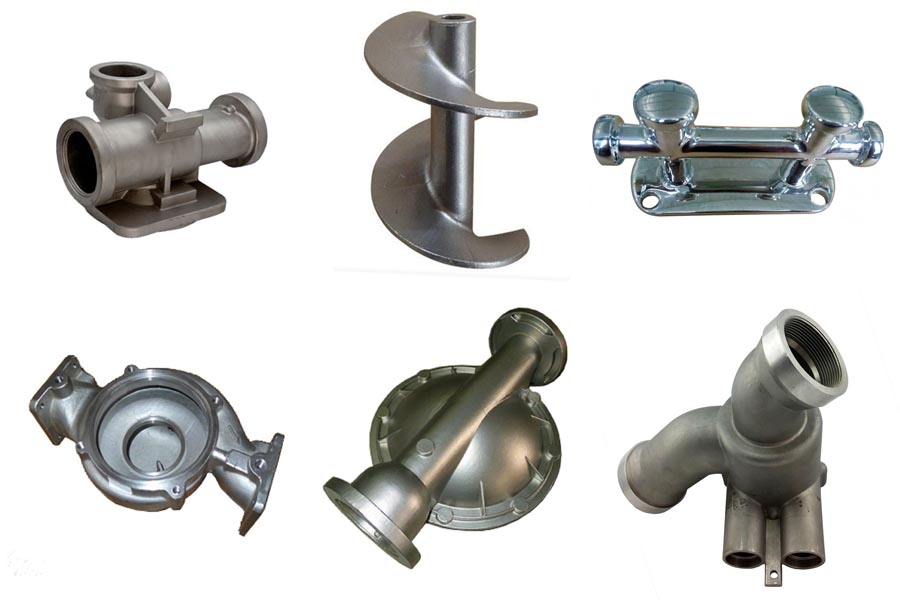
Post time: Feb-01-2021