Factory Outlets Aluminium Lost Wax Casting - Grey Cast Iron Sand Casting Part – RMC Foundry Detail:
Grey cast iron products by sand mould casting process and CNC machining.
Grey cast iron is named after the gray color of the fracture it forms. The gray cast iron is used for housings where the stiffness of the component is more important than its tensile strength, such as internal combustion engine cylinder blocks, pump housings, valve bodies, electrical boxes, counter weights and decorative castings. Grey cast iron’s high thermal conductivity and specific head capacity are often exploited to make cast iron cookware and disc brake rotors.
A typical chemical composition to obtain a graphitic microstructure is 2.5 to 4.0% carbon and 1 to 3% silicon by weight. Graphite may occupy 6 to 10% of the volume of grey iron. Silicon is important to making grey iron as opposed to white cast iron, because silicon is a graphite stabilizing element in cast iron, which means it helps the alloy produce graphite instead of iron carbides; at 3% silicon almost no carbon is held in chemical combination with the iron.
The graphite takes on the shape of a three-dimensional flake. In two dimensions, as a polished surface will appear under a microscope, the graphite flakes appear as fine lines. The tips of the flakes act as preexisting notches; therefore, it is brittle. The presence of graphite flakes makes the Grey Iron easily machinable as they tend to crack easily across the graphite flakes. Grey iron also has very good damping capacity and hence it is mostly used as the base for machine tool mountings.
Gray Cast Iron Mechanical Properties |
|||||||
Item according to DIN EN 1561 | Measure | Unit | EN-GJL-150 | EN-GJL-200 | EN-GJL-250 | EN-GJL-300 | EN-GJL-350 |
EN-JL 1020 | EN-JL 1030 | EN-JL 1040 | EN-JL 1050 | EN-JL 1060 | |||
Tensile Strength | Rm | MPA | 150-250 | 200-300 | 250-350 | 300-400 | 350-450 |
0.1% Yield Strength | Rp0,1 | MPA | 98-165 | 130-195 | 165-228 | 195-260 | 228-285 |
Elongation Strength | A | % | 0,3 – 0,8 | 0,3 – 0,8 | 0,3 – 0,8 | 0,3 – 0,8 | 0,3 – 0,8 |
Compressive Strength | σdB | MPa | 600 | 720 | 840 | 960 | 1080 |
0,1% Compressive Strength | σd0,1 | MPa | 195 | 260 | 325 | 390 | 455 |
Flexural Strength | σbB | MPa | 250 | 290 | 340 | 390 | 490 |
Schuifspanning | σaB | MPa | 170 | 230 | 290 | 345 | 400 |
Shear Stress | TtB | MPa | 170 | 230 | 290 | 345 | 400 |
Modules of elasticity | E | GPa | 78 – 103 | 88 – 113 | 103 – 118 | 108 – 137 | 123 – 143 |
Poisson number | v | – | 0,26 | 0,26 | 0,26 | 0,26 | 0,26 |
Brinell hardness | HB | 160 – 190 | 180 – 220 | 190 – 230 | 200 – 240 | 210 – 250 | |
Ductility | σbW | MPa | 70 | 90 | 120 | 140 | 145 |
Tension and pressure change | σzdW | MPa | 40 | 50 | 60 | 75 | 85 |
Breaking Strength | Klc | N/mm3/2 | 320 | 400 | 480 | 560 | 650 |
Density | g/cm3 | 7,10 | 7,15 | 7,20 | 7,25 | 7,30 |
Sand casting uses green sand (moist sand) or dry sand to form the molding systems. The green sand casting is the oldes casting process used in history. When making the mold, the patterns made of wood or metal should be produced in order to form the hollow cavity. The molten metal then pour into the cavity to form the castings after cooling and solidification. Sand casting is less expensive than other casting processes both for mold development and unit casting part. The sand casting, always mean the green sand casting (if no special description). However, nowadays, the other casting processes are also use the sand to make the mold. They have their own names, such as shell mold casting, furan resin coated sand casting (no bake type), lost foam casting and vacuum casting.
Sand Casting Capabilities at RMC Foundry |
||
Description | Molding by Manual | Molding by Automatic Machines |
Max size of Castings | 1,500 mm × 1000 mm × 500 mm | 1,000 mm × 800 mm × 500 mm |
Casting Weight Range | 0.5 kg – 1,000 kg | 0.5 kg – 500 kg |
Annual Capacity | 5,000 tons – 6,000 tons | 8,000 tons – 10,000 tons |
Casting Tolerance | On Request or Standard (ISO8062-2013 or GB/T 6414-1999) | |
Molding Materials | Green Sand, Resin Coated Sand | |
Casting Metal & Alloys | Gray Iron, Ductile Iron, Cast Steel, Stainless Steel, Al Alloys, Brass, Bronze…etc. |
The Advantages of Sand Casting:
- ✔ Lower Cost due to its cheap and recyclable mold materials and simple production equipment.
- ✔ Wide range of unit weight from 0.10 kg to 500 kgs or even bigger.
- ✔ Various Structure from simple type to complex type.
- ✔ Suitable for production requirements of various quantity.
Tolerance That Sand Castings Achieve:
The casting tolerances are divided into Dimensional Casting Tolerances (DCT) and Geometrical Casting Tolerances (GCT). Our foundry would like to talk with you if you have special request on the required tolerances. Here in the following are the general tolerances grade we could reach by our green sand casting, shell mould casting and no-bake furan resin sand casting:
- ✔ DCT Grade by Green Sand Casting: CTG10 ~ CTG13
- ✔ DCT Grade by Shell Mold Casting or Furan Resin Sand Casting: CTG8 ~ CTG12
- ✔ GCT Grade by Green Sand Casting: CTG6 ~ CTG8
- ✔ GCT Grade by Shell Mold Casting or Furan Resin Sand Casting: CTG4 ~ CTG7
Metal & Alloys Grade for Sand Casting Processes |
|
Metal & Alloys | Popular Grade |
Gray Cast Iron | GG10~GG40; GJL-100 ~ GJL-350; |
Ductile (Nodualar) Cast Iron | GGG40 ~ GGG80; GJS-400-18, GJS-40-15, GJS-450-10, GJS-500-7, GJS-600-3, GJS-700-2, GJS-800-2 |
Austempered Ductile Iron (ADI) | EN-GJS-800-8, EN-GJS-1000-5, EN-GJS-1200-2 |
Carbon Steel | C20, C25, C30, C45 |
Alloy Steel | 20Mn, 45Mn, ZG20Cr, 40Cr, 20Mn5, 16CrMo4, 42CrMo, 40CrV, 20CrNiMo, GCr15, 9Mn2V |
Stainless Steel | Ferritic Stainless Steel, Martensitic Stainless Steel, Austenitic Stainless Steel, Precipitation Hardening Stainless Steel, Duplex Stainless Steel |
Aluminium Alloys | ASTM A356, ASTM A413, ASTM A360 |
Brass / Copper-based Alloys | C21000, C23000, C27000, C34500, C37710, C86500, C87600, C87400, C87800, C52100, C51100 |
Standard: ASTM, SAE, AISI, GOST, DIN, EN, ISO, and GB |
Product detail pictures:

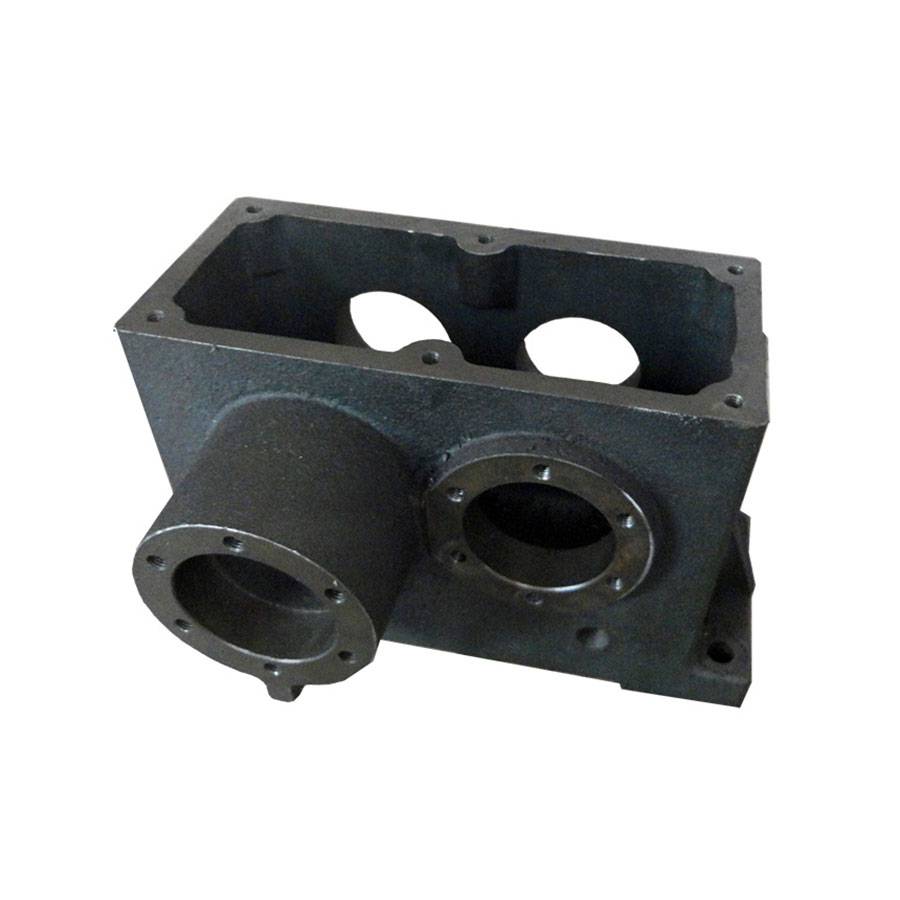
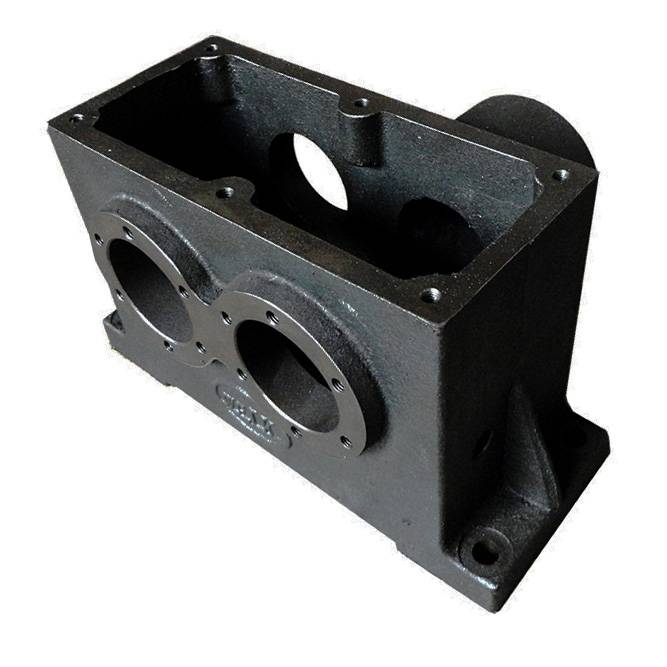
Related Product Guide:
"Based on domestic market and expand overseas business" is our development strategy for Factory Outlets Aluminium Lost Wax Casting - Grey Cast Iron Sand Casting Part – RMC Foundry, The product will supply to all over the world, such as: Cyprus , America , Puerto Rico , We accomplish this by exporting our wigs directly from our own factory to you. The goal of our company is to get customers who enjoy coming back to their business. We sincerely hope to cooperate with you in the near future. If there's any opportunity, welcome to visit our factory!!!

The company's products can meet our diverse needs, and the price is cheap, the most important is that the quality is also very nice.

-
Factory Free sample Nodular Iron Green Sand Cas...
-
PriceList for Lost Wax Casting Parts - Nodular...
-
Free sample for Iron Foundry - Non Ferrous Met...
-
professional factory for Precision Casting Manu...
-
Big Discount Steel Casting Supplier - CNC Prec...
-
2020 China New Design China Machining Company -...