Vacuum Casting Foundry
Vacuum casting process, also called Nagative Pressure Sealed Casting or V process casting, uses the dry sand (which is the same as lost foam casting in this point) and vacuum pressure to form the casting mold. It uses vacuum pressure to cover the heated plastic film on the pattern and template, fill the sand box with dry sand without binder, and then seal the top surface of the sand mold with the plastic film, followed by vacuum to make the sand firm and tight. After that, remove the mold, put the sand cores, close the mold to make everything ready for pouring. Finally, the custom casting is obtained after the molten metal is cooled and solidified.
Vacuum casting is different from both the green sand casting and investment casting due to the technique that is used to create molding systems. The required castings which with large size and thick walls are more suitable for beening cast by the vacuum casting process.

Wood Patterns for Vacuum Casting
What We Can Achieve by Vacuum Casting
Here at RMC, we utilize vacuum casting methods to produce metal components that range in weight from a few kilograms up to hundreds of kilograms. Our experience in the vacuum casting method guarantee that we can supply net shape or near net shape parts that require little or no secondary process.
• Max Size: 1,000 mm × 800 mm × 500 mm
• Weight Range: 0.5 kg - 100 kg
• Annual Capacity: 2,000 tons
• Tolerances: On Request.
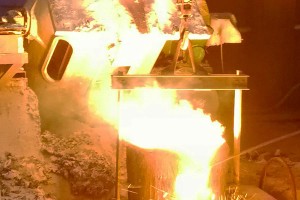
Molten Metal
What Metals and Alloy We Pour by Vacuum Casting
The following cast metal could be used in vacuum casting process at our foundry:
• Cast Iron: Gray Iron, Ductile Iron, Malleable Iron
• Carbon Steel: Low Carbon Steel, Medium Carbon Steel and High Carbon Steel from AISI 1020 to AISI 1060.
• Cast Steel Alloys: ZG20SiMn, ZG30SiMn, ZG30CrMo, ZG35CrMo, ZG35SiMn, ZG35CrMnSi, ZG40Mn, ZG40Cr, ZG42Cr, ZG42CrMo...etc on request.
• Stainless Steel: AISI 304, AISI 304L, AISI 316, AISI 316L and other stainless steel grade.
• Brass & other Copper-based Alloys.
• Wear-resistant Steel, Corrosion-resistant Steel, Tool Steel.
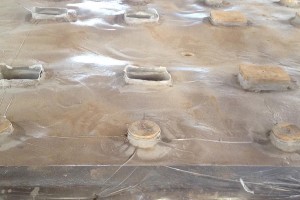
Sealing Sand Box
Steps of Vacuum Casting Process
1- The pattern is covered tightly by a thin sheet of plastic.
2- A flask is placed over the coated pattern and is filled with dry sand without bind.
3- The second flak is then placed on top of the sand, and a vacuum draws the sand so that the pattern can be tight and withdrawn. Both halves of the mold are made and assembled in this way.
4- During pouring, the mold remains under a vacuum but the casting cavity does not.
5- When the metal has solidified, the vacuum is turned off and the sand falls away, releasing the casting.
6- Vacuum molding produces casting with high-quality detail and dimensional accuracy.
7- It is especially well suited for large, relatively flat castings.
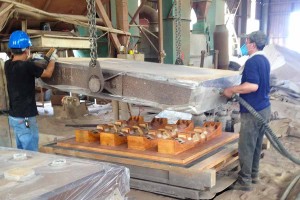
Closing Flasks
Why Choose Vacuum Casting
Vacuum casting could be your alternative if you care about the following points:
- Easy recovery of the sand because the binders are not used
- Sand does not require mechanical reconditioning.
- Good air permeability because there is no water is mixed with sand, therefore less casting defects.
- More suitable for large scale castings
- Cost effective, especially for large castings.
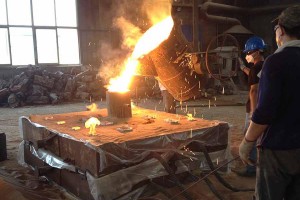
Molten Metal Pouring
What Facilities We Rely On for Vacuum Casting
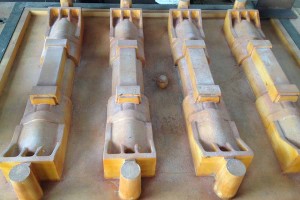
Wood Patterns
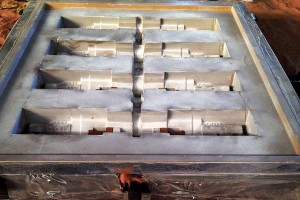
Sand Cores Making
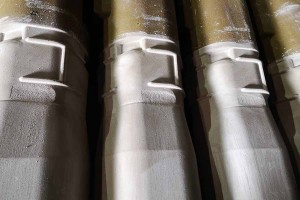
Coating Sand Cores
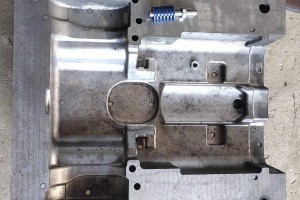
Vacuum Casting Toolings
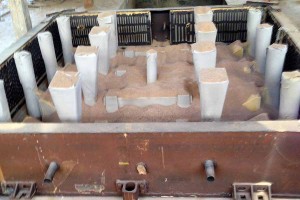
Vacuum Casting Mould

Cooling and Solidification
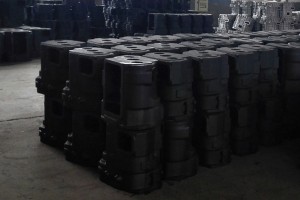
Vacuum Casting Products
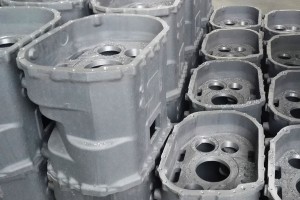
Gray Iron Vacuum Castings
Typical Vacuum Casting We Are Producing

Vacuum Casting Parts
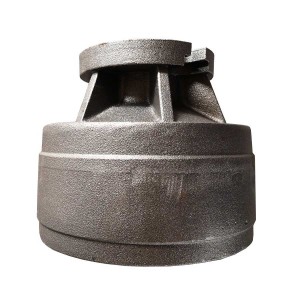
Steel Vacuum Castings
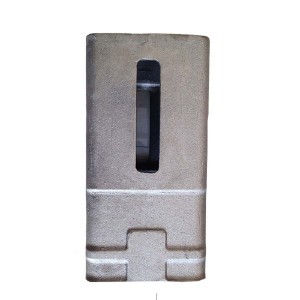
Custom V Type Castings
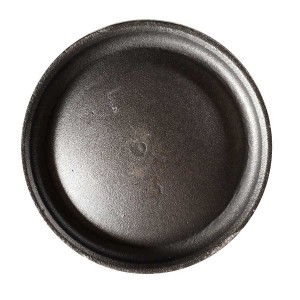
V Type Casting Parts
Which Industries Our Vacuum Castings Are Serving
Castings made by vacuum casting process are utilized to cast a wide variety of items, including high quality, high performance industrial parts of complex structures. The application of the vacuum casting parts covers a wide range of industries, in our casting company they are typically used in the following areas:
• Rail Trains | • Logistics Equipment |
• Heavy Duty Trucks | • Agricultural Equipment |
• Automotive | • Hydraulics |
• Construction Equipment | • Engine Systems |
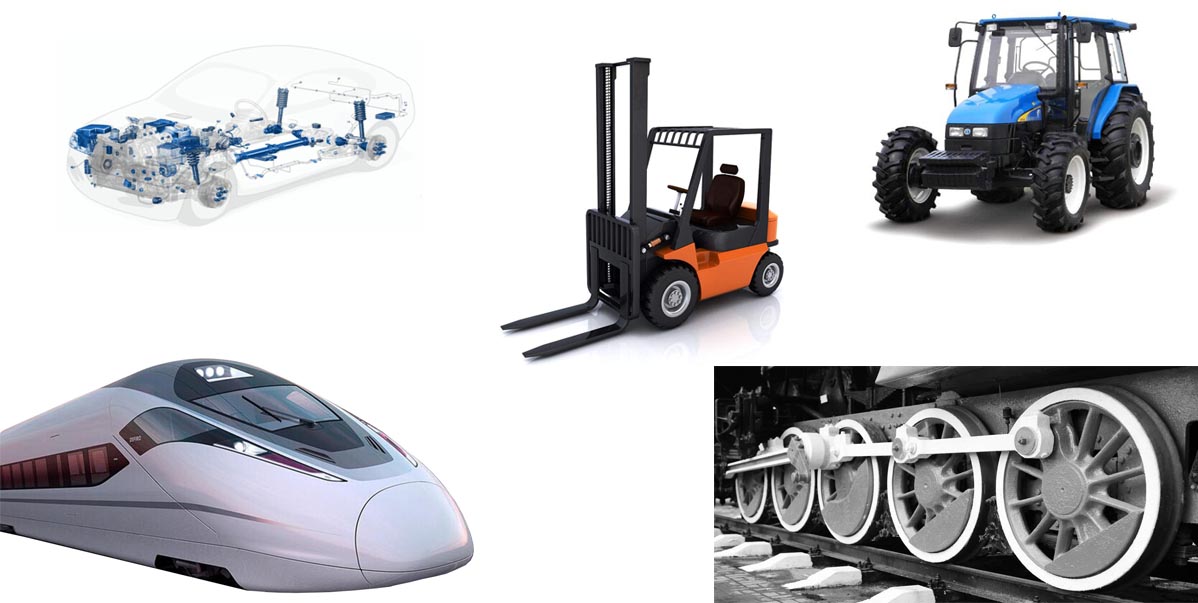
Applications of V Type Castings
We Can Provide More Than You Expect
There are several reasons to choose RMC as your source for vacuum castings, these include:
- Engineering team whose members are focusing on metal casting field.
- Extensive experience with complex geometries parts
- A broad range of materials, including ferrous and non-ferrous alloys
- In-house CNC machining capabilities
- One-stop solutions for castings and secondary process
- Consistent quality guaranteed and continuous improvement.
- Teamwork including toolmakers, engineers, foundryman, machinist and production technicians.
