Short Lead Time for Zinc Alloy Gravity Casting - Super Duplex Stainless Steel Investment Casting Impeller – RMC Foundry Detail:
Duplex stainless steel casting means the castings made of duplex stainless steel. Duplex Stainless Steel (DSS) refers to stainless steel with ferrite and austenite each accounting for about 50%. Generally, the content of less phases needs to be at least 30%. In the case of low C content, the Cr content is 18% to 28%, and the Ni content is 3% to 10%. Some duplex stainless steels also contain alloying elements such as Mo, Cu, Nb, Ti, and N.
The DSS has the characteristics of austenitic and ferritic stainless steel. Compared with ferrite, it has higher plasticity and ductility, no room temperature brittleness, and significantly improved intergranular corrosion resistance and welding performance, while still maintaining brittleness, high thermal conductivity, and superplasticity as ferrite stainless steel. Compared with austenitic stainless steel, DSS has high strength and significantly improved resistance to intergranular corrosion and chloride stress corrosion. Duplex stainless steel has excellent pitting corrosion resistance and is also a nickel-saving stainless steel.
In casting production, most of the stainless steel castings are completed by investment casting. The surface of stainless steel castings produced by investment casting is smoother and the dimensional accuracy is easier to control. Of course, the cost of investment casting stainless steel parts is relatively high compared to other processes and materials.
▶ Capabilities of Investment Casting Foundry
• Max Size: 1,000 mm × 800 mm × 500 mm
• Weight Range: 0.5 kg – 100 kg
• Annual Capacity: 2,000 tons
• Bond Materials for Shell Building: Silica Sol, Water Glass and their mixtures.
• Tolerances: On Request.
▶ Main Production Procedure of Investment Casting
• Create a wax pattern or replica
• Sprue the wax pattern
• Invest the wax pattern
• Eliminate the wax pattern by burning it (inside the furnace or in hot water) to create a mould.
• Force molten metal pour into the mould
• Cooling and Solidification
• Remove sprue from the castings
• Finish and polish the finished investment castings
▶ Why You Choose RMC for Custom Lost Wax Casting Parts?
• Full solution from one single supplier ranging customized pattern design to finished castings and secondary process including CNC machining, heat treatment and surface treatment.
• Costdown proposals from our professional engineers based on your unique requirement.
• Short leadtime for prototype, trial casting and any possible technical improvement.
• Bonded Materials: Silica Col, Water Glass and their mixtures.
• Manufacturing flexibility for small orders to mass orders.
• Strong outsourcing manufacturing capabilities.
Product detail pictures:
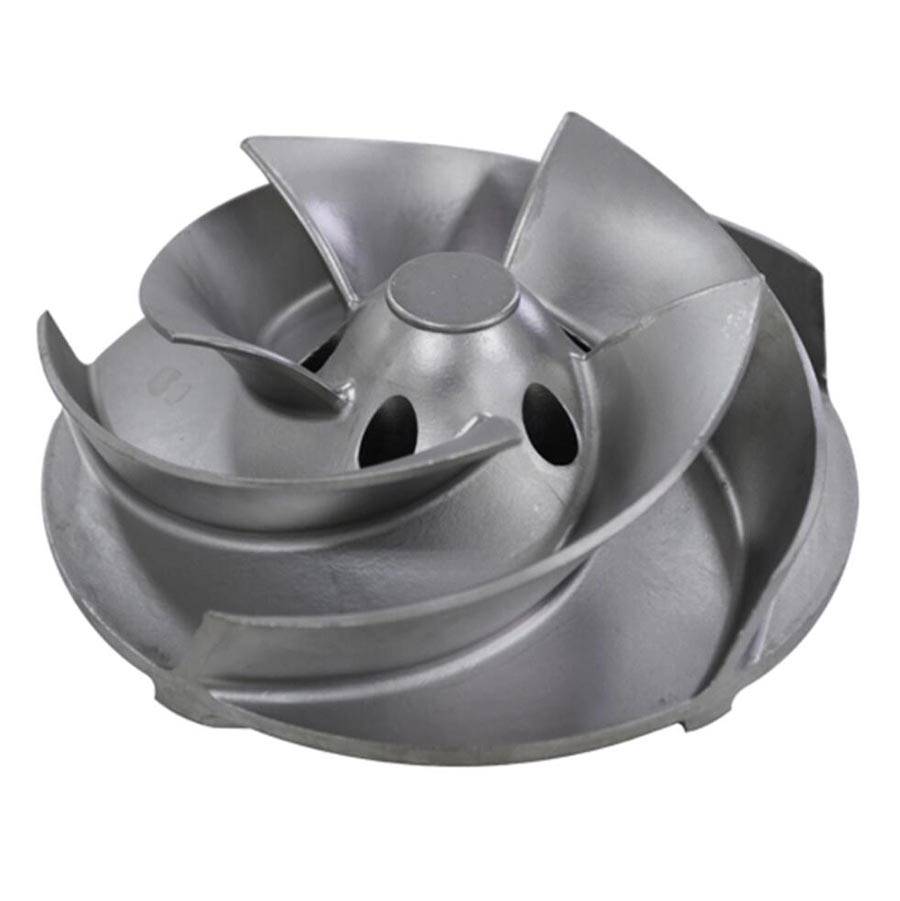
Related Product Guide:
abide by the contract", conforms to the market requirement, joins during the market competition by its superior quality also as provides extra comprehensive and exceptional service for consumers to let them turn into significant winner. The pursue of the business, is definitely the clients' gratification for Short Lead Time for Zinc Alloy Gravity Casting - Super Duplex Stainless Steel Investment Casting Impeller – RMC Foundry, The product will supply to all over the world, such as: Egypt , Algeria , Greek , Our experience makes us important in our customer eyes. Our quality speaks itself the properties like it do not tangle, shed or breakdown, so that are our customers will always be confident while placing an order.

The sales manager has a good English level and skilled professional knowledge, we have a good communication. He is a warm and cheerful man, we have a pleasant cooperation and we became very good friends in private.

-
Hot sale Full Mold Casting - Ductile Cast Iron...
-
New Delivery for Bronze Casting Foundry - Allo...
-
Manufactur standard Carbon Steel V Process Cast...
-
OEM/ODM China Stainless Steel Vacuum Casting Ma...
-
Hot sale Alloy Steel Vacuum Casting Foundry - ...
-
Factory Original Ductile Iron Lost Foam Casting...