Professional China Steel Shell Mold Casting - Custom Malleable Cast Iron Shell Casting Product – RMC Foundry Detail:
The malleable cast iron castings are usually cast by green sand casting or resin coated sand shell mold casting processes at RMC casting foundry.
Cast irons are the ferrous alloys which have carbon contents of more than 2%. Though cast irons can have a carbon percentage between 2 to 6.67, the practical limit is normally between 2 and 4%. These are important mainly because of their excellent casting qualities. The gray cast irons, ductile cast irons (also called nodular cast iron or spheroidal graphite iron) and malleable cast iron are the three main cast iron in foundry.
The malleable cast iron has free carbon which is present in the form of nodules in the matrix of cementite and ferrite. This is achieved by first chilling the casting so that all white cast iron is formed, followed by a controlled heat treatment process so that some of the cementite is transformed to ferrite and nodules of free carbon. This material is more ductile than grey cast iron. This form is suitable only for components with very small section thicknesses since all white cast iron is to form the starting point for malleable iron.
Shell mould casting is a process in which the sand mixed with a thermosetting resin is allowed to come into contact with a heated metallic pattern plate, so that a thin and strong shell of mould is formed around the pattem. Then the shell is removed from the pattern and the cope and drag are removed together and kept in a flask with the necessary back-up material and the molten metal is poured into the mould.
Generally, dry and fine sand (90 to 140 GFN) that is completely free of the clay is used for preparing the shell moulding sand. The grain size to be chosen depends on the surface finish desired on the casting. Too fine a grain size requires large amount of resin, which makes the mould expensive.
Advantages of Resin Coated Sand Shell Mold Casting:
1. Shell-mould castings are generally more dimensionally accurate than sand castings. It is possible to obtain a tolerance of +0.25 mm for steel castings and +0. 35 mm for grey cast iron castings under normal working conditions. In the case of close toleranced shell moulds, one may obtain it in the range of +0.03 to +0.13 mm for specific applications.
2. A smoother surface can be obtained in shell castings. This is primarily achieved by the finer size grain used. The typical range of roughness is of the order of 3 to 6 mircrons.
3. Draft angles, which are lower than the sand castings, are required in shell moulds. The reduction in draft angles may be from 50 to 75%, which considerably saves the material costs and the subsequent machining costs.
4. Sometimes, special cores may be eliminated in shell moulding. Since the sand has high strength the mould could be designed in such a manner that internal cavities can be formed directly with the need of shell cores.
5. Also, very thin sections(up to 0.25 mm) of the type of air-cooled cylinder heads can be readily made by the shell moulding because of the higher strength of the sand used for moulding.
6. Permeability of the shell is high and therefore no gas inclusions occur.
7. Very small amount of sand needs to be used.
8. Mechanisation is readily possible because of the simple processing involved in shell moulding.
Resin Coated Sand Casting Metal and Alloys | |
Metal & Alloys | Popular Grade |
Gray Cast Iron | GG10~GG40; GJL-100 ~ GJL-350; |
Ductile (Nodular) Cast Iron | GGG40 ~ GGG80; GJS-400-18, GJS-40-15, GJS-450-10, GJS-500-7, GJS-600-3, GJS-700-2, GJS-800-2 |
Austempered Ductile Iron (ADI) | EN-GJS-800-8, EN-GJS-1000-5, EN-GJS-1200-2 |
Carbon Steel | C20, C25, C30, C45 |
Alloy Steel | 20Mn, 45Mn, ZG20Cr, 40Cr, 20Mn5, 16CrMo4, 42CrMo, 40CrV, 20CrNiMo, GCr15, 9Mn2V |
Stainless Steel | Ferritic Stainless Steel, Martensitic Stainless Steel, Austenitic Stainless Steel, Precipitation Hardening Stainless Steel, Duplex Stainless Steel |
Aluminium Alloys | ASTM A356, ASTM A413, ASTM A360 |
Brass / Copper-based Alloys | C21000, C23000, C27000, C34500, C37710, C86500, C87600, C87400, C87800, C52100, C51100 |
Standard: ASTM, SAE, AISI, GOST, DIN, EN, ISO, and GB |
CNC Precision Machining Capabilities | ||||
Facilities | Quantity | Size Range | Annual Capacity | General Accuracy |
Vertical Machining Center (VMC) | 48 sets | 1500mm × 1000mm × 800mm | 6000 tonn or 300000 pieces | ±0.005 |
Horizontal Machining Center (VMC) | 12 sets | 1200mm × 800mm × 600mm | 2000 tons or 100000 pieces | ±0.005 |
CNC Machine | 60 sets | Max turning dia. φ600mm | 5000 tons or 600000 pieces |
Product detail pictures:
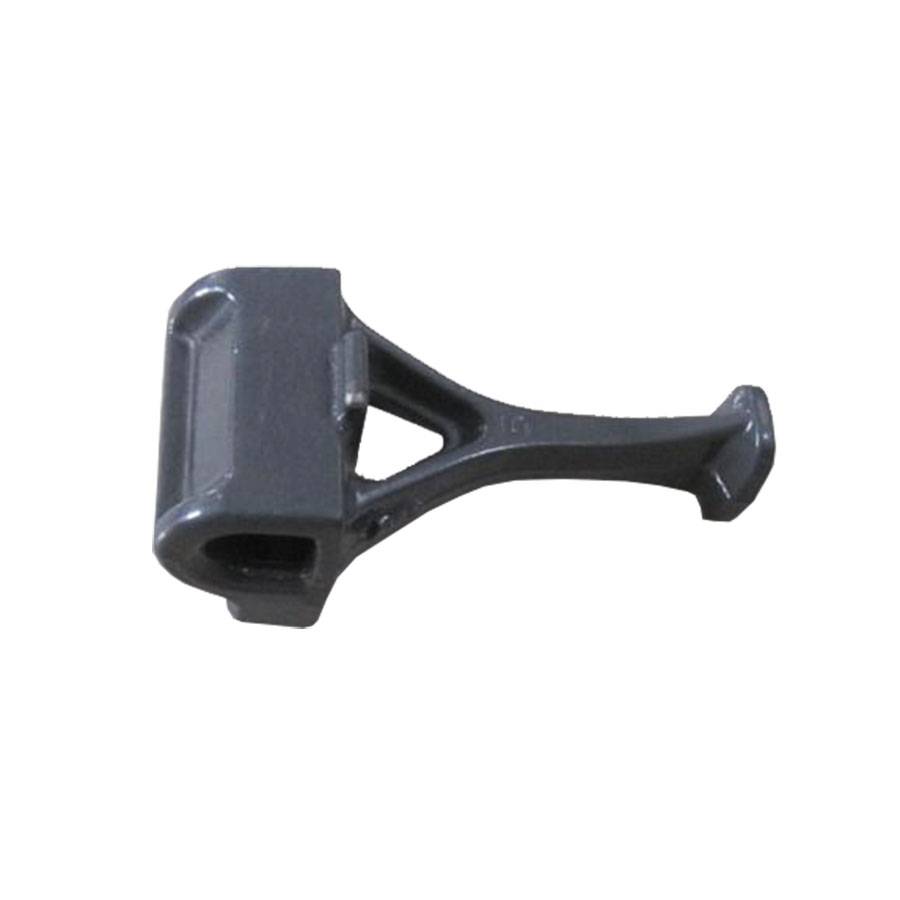
Related Product Guide:
That has a positive and progressive attitude to customer's interest, our organization consistently improves our products quality to satisfy the demands of shoppers and further focuses on safety, reliability, environmental specifications, and innovation of Professional China Steel Shell Mold Casting - Custom Malleable Cast Iron Shell Casting Product – RMC Foundry, The product will supply to all over the world, such as: Korea , Brasilia , Armenia , Now, we professionally supplies customers with our main products And our business is not only the "buy" and "sell", but also focus on more. We target to be your loyal supplier and long-term cooperator in China. Now, We hope to be the friends with you.

The goods are very perfect and the company sales manager is warmful, we will come to this company to purchase next time.

-
Custom Gray Cast Iron Sand Casting
-
Ductile Cast Iron CNC Machining Parts
-
Ductile Cast Iron Investment Casting
-
Ductile Cast Iron Resin Coated Sand Castings
-
Ductile Cast Iron Sand Casting Parts
-
Ductile Cast Iron Sand Castings
-
Custom Stainless Steel Investment Casting
-
Duplex Stainless Steel 2205 / 2507 Investment C...
-
Duplex Stainless Steel Lost Wax Casting
-
Lost Wax Casting Stainless Steel Product
-
Precipitation Hardening Stainless Steel Casting
-
Stainless Steel 304/CF8 Investment Casting