OEM/ODM China Malleable Iron Sand Casting Foundry - Ductile Iron Sand Casting Valve Body – RMC Foundry Detail:
Ductile Cast Iron Ball Valve Housing by Sand Casting from China Foundry with OEM Custom and CNC Machining Services.
Cast iron is an iron-carbon cast alloy with other elements that is made by remelting pig iron, scrap, and other additions. For differentiation from steel and cast steel, cast iron is defined as a cast alloy with a carbon content (min 2.03%) that ensures the solidification of the final phase with a eutectic transformation.
Depending on chemical specifications, cast irons can be non- alloyed or alloyed. The range of alloyed irons is much wider, and they contain either higher amounts of common components, such as silicon and manganese, or special additions, such as nickel, chromium, aluminum, molybdenum, tungsten, copper, vana- dium, titanium, plus others. Generally speaking, the cast iron could be divided into gray iron, ducitle iron (nodular iron), white cast iron, compacted graphite iron and malleable cast iron.
Ductile cast iron, which is represent a group of cast iron, also called nodular iron. Nodular cast iron obtains nodular graphite through spheroidization and inoculation treatment, which effectively improves the mechanical properties of the cast iron, especially the plasticity and toughness, so as to obtain higher strength than carbon steel.
Ductile cast iron castings have better shock absorption performance than carbon steel, while carbon steel castings have much better weldability. And to some extent, the ductile iorn castings could have some performances of resistanting wear and rust. So the ductile iron casting could be used for some pump housings or water supply systems. However, we still need to make precautions for protecting them from wearing and rust.
Ductile iron is not a single material but is part of a group of materials which can be produced to have a wide range of properties through control of the microstructure. The common defining characteristic of this group of materials is the shape of the graphite. In ductile irons, the graphite is in the form of nodules rather than flakes as it is in grey iron. The sharp shape of the flakes of graphite create stress concentration points within the metal matrix and the rounded shape of the nodules less so, thus inhibiting the creation of cracks and providing the enhanced ductility that gives the alloy its name.
Raw Materials Available for Sand Casting
• Gray Iron: GJL-100, GJL-150, GJL-200, GJL-250, GJL-300, GJL-350
• Ductile Iron: GJS-400-18, GJS-40-15, GJS-450-10, GJS-500-7, GJS-600-3, GJS-700-2, GJS-800-2
• Aluminium and Their Alloys
• Other Materials and Standards on request
Capabilities of Sand Casting moulded by hand:
• Max Size: 1,500 mm × 1000 mm × 500 mm
• Weight Range: 0.5 kg – 500 kg
• Annual Capacity: 5,000 tons – 6,000 tons
• Tolerances: On Request.
Capabilities of Sand Casting by Automatic Molding Machines:
• Max Size: 1,000 mm × 800 mm × 500 mm
• Weight Range: 0.5 kg – 500 kg
• Annual Capacity: 8,000 tons – 10,000 tons
• Tolerances: On Request.
Main Production Procedure
Patterns & Tooling Design → Making Patterns → Moulding Process → Chemical Composition Analysis → Melting & Pouring → Cleaning, Grinding & Shot Blasting → Post Processing or Packing for Shipment
Sand Casting Inspection Capabilities
• Spectrographic and manual quantitative analysis
• Metallographic analysis
• Brinell, Rockwell and Vickers hardness inspection
• Mechanical property analysis
• Low and normal temperature impact testing
• Cleanliness inspection
• UT, MT and RT inspection
Post-Casting Process
• Deburring & Cleaning
• Shot Blasting / Sand Peening
• Heat Treatment: Normalization, Quench, Tempering, Carburization, Nitriding
• Surface Treatment: Passivation, Andonizing, Electroplating, Hot Zinc Plating, Zinc Plating, Nickel Plating, Polishing, Electro-Polishing, Painting, GeoMet, Zintec
• CNC Precision Machining: Turning, Milling, Lathing, Drilling, Honing, Grinding,
General Commerial Terms
• Main work flow: Inquiry & Quotation → Confirming Details / Cost Reduction Proposals → Tooling Development → Trial Casting → Samples Approval → Trial Order → Mass Production → Continuous Order Proceeding
• Lead time: Estimatedly 15-25 days for tooling development and estimatedly 20 days for mass production.
• Payment Terms: To be negotiated.
• Payment methods: T/T, L/C, West Union, Paypal.
Product detail pictures:
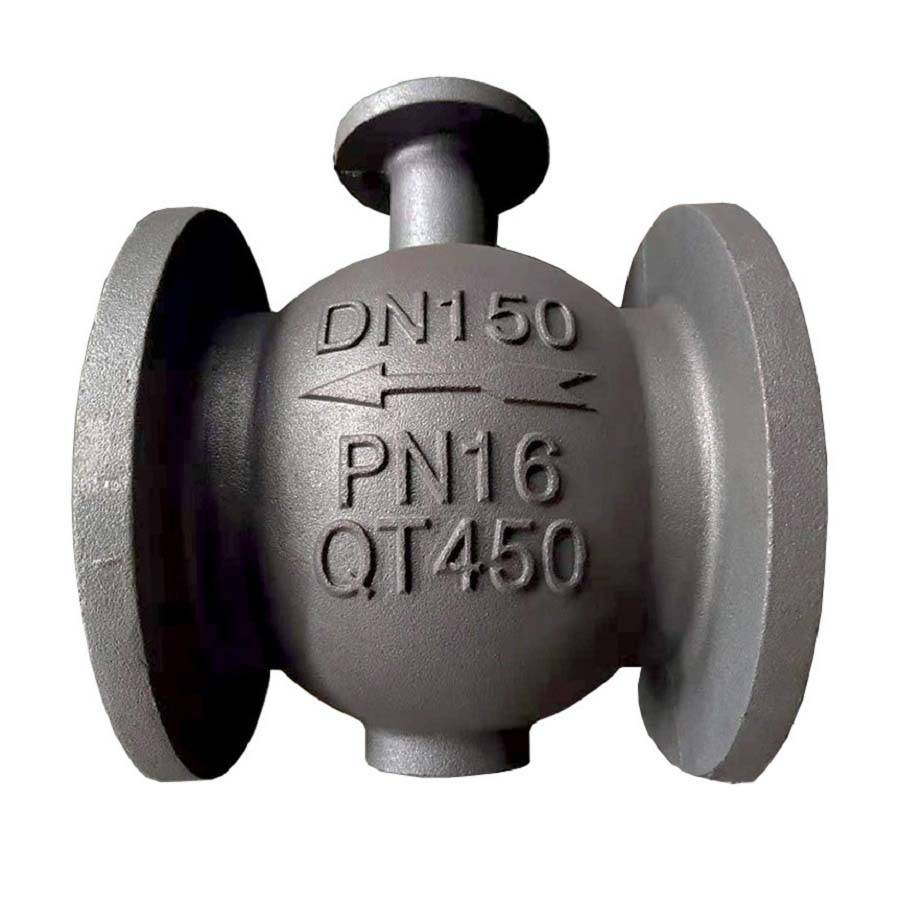
Related Product Guide:
Our pursuit and company intention is usually to "Always fulfill our purchaser requirements". We go on to acquire and layout excellent high quality products for both our previous and new consumers and realize a win-win prospect for our customers too as us for OEM/ODM China Malleable Iron Sand Casting Foundry - Ductile Iron Sand Casting Valve Body – RMC Foundry, The product will supply to all over the world, such as: Dominica , Madrid , Armenia , If you are interested in any of our products or would like to discuss a custom order, please feel free to contact us. We are looking forward to forming successful business relationships with new clients around the world in the near future.

The accounts manager made a detailed introduction about the product, so that we have a comprehensive understanding of the product, and ultimately we decided to cooperate.

-
Factory supplied Iron Casting Manufacturer - A...
-
Factory For Stainless Steel Lost Wax Casting Su...
-
Manufacturer of Aluminium Foundry - Brass CNC ...
-
Factory Price For Aluminium Green Sand Casting ...
-
Best quality Steel Investment Casting Supplier ...
-
Manufacturer for Gray Iron Sand Casting Product...