China Cheap price Shell Mold Casting Parts - Resin Coated Sand Casting of Nodular Cast Iron – RMC Foundry Detail:
The ductile cast iron castings produced by resin coated sand casting from China casting company with CNC machining and testing services. The resin coated sand casting is widely used to produce custom castings with higher requirements than green sand casting process. Before making the mould and core, the coated sand have been covered with a solid resin film on the surface of the sand particles. The coated sand is also called shell (core) sand. The technological process is to mechanically mix powdered thermosetting phenolic tree with raw sand and solidify when heated. It has been developed into coated sand by using thermoplastic phenolic resin plus latent curing agent (such as urotropine) and lubricant (such as calcium stearate) through a certain coating process. When the coated sand is heated, the resin coated on the surface of the sand particles melts. Under the action of the methylene group decomposed by the Maltropine, the molten resin rapidly transforms from a linear structure to an infusible body structure so that the coated sand is solidified and formed. In addition to the general dry granular form of coated sand, there are also wet and viscous coated sand. Resin coated sand casting has the following characteristics 1) It has suitable strength performance. It can meet the requirements for high-strength shell core sand, medium-strength hot-box sand, and low-strength non-ferrous alloy sand. 2) Excellent fluidity, good moldability of the sand core and clear outline, which can produce the most complex sand cores, such as water jacket sand cores such as cylinder heads and machine bodies. 3) The surface quality of the sand core is good, compact and not loose. Even if less or no coating is applied, better surface quality of castings can be obtained. The dimensional accuracy of castings can reach CT7-CT8, and the surface roughness Ra can reach 6.3-12.5μm. 4) Good collapsibility, which is conducive to casting cleaning and improving product performance 5) The sand core is not easy to absorb moisture, and the strength of long-term storage is not easy to decrease, which is conducive to storage, transportation and use Manufacturing processes of resin coated sand mold (core) making for shell moulding casting: 1. The basic process of manufacturing coated sand mold (core) is: flip or blow sand→crust→sand discharge→harden→core (mold) and so on. 1) Turn over or blow sand. That is, the coated sand is poured on the shell mold or blown into the core box to manufacture the shell or shell core. 2) Encrustation. The thickness of the shell layer is controlled by adjusting the heating temperature and holding time. 3) Sand discharge. Tilt the mold and the core box to make the unreacted coated sand fall from the heated shell surface, and collect it for reuse. In order to make it easier to remove the unmelted coated sand, if necessary, a mechanical method of shaking back and forth can be adopted. 4) Hardening. In the heating state, in order to make the thickness of the shell more uniform, make it contact with the surface of the heated shell within a certain period of time to further harden. 5) Take the core. Take the hardened shell shape and shell core out of the mold and core box. Raw Materials for Resin Coated Sand Casting Process: • Cast Iron: Gray Cast Iron, Ductile Cast Iron. • Cast Carbon Steel and Alloy Steel: Low Carbon Steel, Medium Carbon Steel and High Carbon Steel from AISI 1020 to AISI 1060; 20CrMnTi, 20SiMn, 30SiMn, 30CrMo, 35CrMo, 35SiMn, 35CrMnSi, 40Mn, 40Cr, 42Cr, 42CrMo…etc on request. • Cast Stainless Steel: AISI 304, AISI 304L, AISI 316, AISI 316L and other stainless steel grade. • Cast Aluminium Alloys. • Brass & Copper. • Other Materials and Standards on request ▶ Resin Coated Sand Casting Capacities: • Max Size: 1,000 mm × 800 mm × 500 mm • Weight Range: 0.5 kg – 100 kg • Annual Capacity: 2,000 tons • Tolerances: On Request. ▶ Inspecting Resin Coated Sand Castings: • Spectrographic and manual quantitative analysis • Metallographic analysis • Brinell, Rockwell and Vickers hardness inspection • Mechanical property analysis • Low and normal temperature impact testing • Cleanliness inspection • UT, MT and RT inspection ▶ Resin Coated Sand Casting Procedures: ✔ Making Metal Patterns. The pre-coated resin sand needs to be heated in the patterns, so metal patterns are the necessary tooling to make shell molding castings. ✔ Making Pre-coated Sand Mold. After installing the metal patterns on the molding machine, the pre-coated resin sand will be shot into the patterns, and after heating, the resin coating will be molten, then the sand molds become solid sand shell and cores. ✔ Melting the Cast Metal. Using induction furnaces, the materials would be melted into liquid, then the chemical compositions of the liquid iron should be analyzed to match the required numbers and percents. ✔ Pouring Metal. When the melted iron meet the requirements, then they will be poured into the shell molds. Based on different characters of the casting design, the shell molds will be buried into green sand or stacked up by layers. ✔ Shot Blasting, Grinding and Cleaning. After the cooling and solidification of the castings, the risers, gates or additional iron should be cut off and removed. Then the iron castings will be cleaned by sand peening equipment or shot blasting machines. After grinding the gating head and parting lines, the finished casting parts would come, waiting for the further processes if needed. ▶ Post-Casting Process • Deburring & Cleaning • Shot Blasting / Sand Peening • Heat Treatment: Normalization, Quench, Tempering, Carburization, Nitriding • Surface Treatment: Passivation, Andonizing, Electroplating, Hot Zinc Plating, Zinc Plating, Nickel Plating, Polishing, Electro-Polishing, Painting, GeoMet, Zintec. • CNC Machining: Turning, Milling, Lathing, Drilling, Honing, Grinding. ▶ Why You Choose RMC for Shell Mold Casting Components? ✔ Precision and therefore a high material utilization. You will get a net or near-net-shape products after shell molding casting, depending on the requirements of end-users, there will be no or very little machining process is required. ✔ Better surface performance. Thanks to the new-tech materials for molding, the castings from shell molding have a much fine and higher accuracy surface. ✔ A good balanced choice comparing to the sand casting and investment. The shell molding casting have better performance and surface than sand casting, while having much lower costs than precision investment casting. ▶ General Commerial Terms • Main workflow: Inquiry & Quotation → Confirming Details / Cost Reduction Proposals → Tooling Development → Trial Casting → Samples Approval → Trial Order → Mass Production → Continuous Order Proceeding • Leadtime: Estimatedly 15-25 days for tooling development and estimatedly 20 days for mass production. • Payment Terms: To be negotiated. • Payment methods: T/T, L/C, West Union, Paypal.
Product detail pictures:
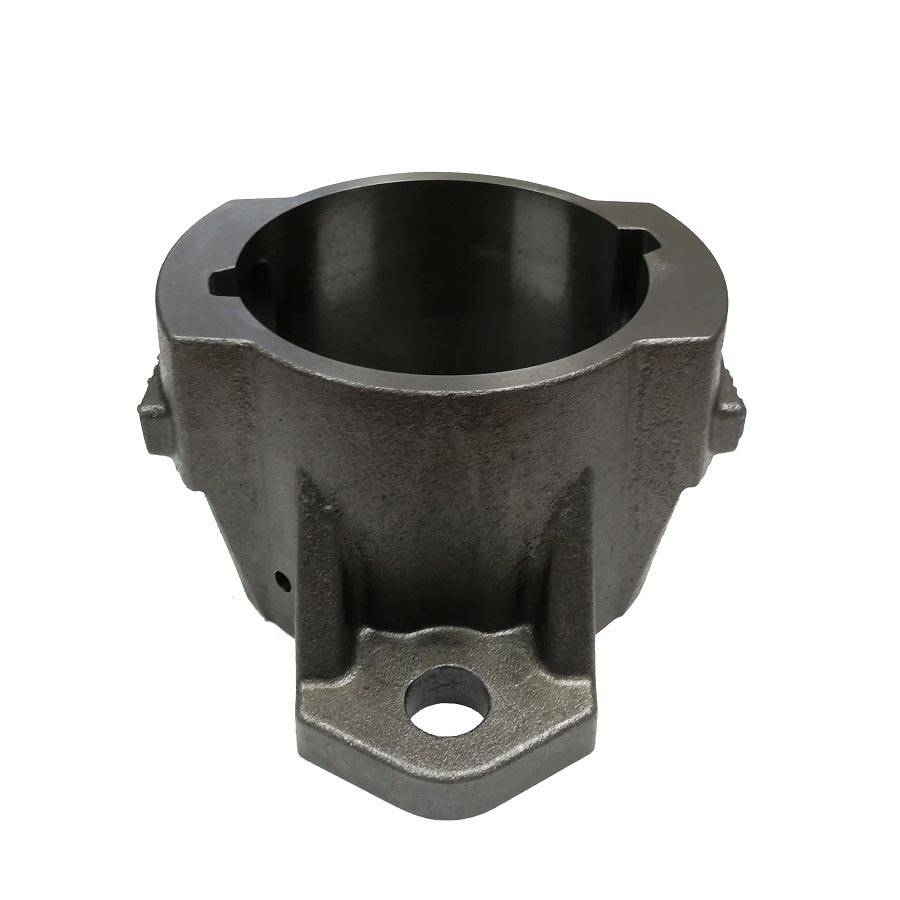
Related Product Guide:
Excellent 1st,and Client Supreme is our guideline to deliver the ideal provider to our prospects.Nowadays, we have been seeking our best to become certainly one of the most effective exporters in our discipline to meet shoppers more require for China Cheap price Shell Mold Casting Parts - Resin Coated Sand Casting of Nodular Cast Iron – RMC Foundry, The product will supply to all over the world, such as: Israel , Paris , Macedonia , As a well educated, innovative and energetic staff,we are responsible for all elements of the research, design, manufacturing, sales and distribution. With studying and developing new techniques,we are not only following but also leading the fashion industry. We listen attentively to the feedback from our customers and provide instant communication. You will instantly feel our expertise and attentive service.

In China, we have many partners, this company is the most satisfying to us, reliable quality and good credit, it is worth appreciation.

-
2020 wholesale price Steel Vacuum Casting Compa...
-
Bottom price Ductile Iron No Bake Casting - Al...
-
Hot Sale for Gray Iron Casting Foundry - Custo...
-
Factory Price Alloy Steel Casting Foundry - Du...
-
Quality Inspection for Copper Casting Foundry -...
-
Massive Selection for Brass Casting Foundry - ...