Bottom price Ductile Iron Sand Casting Manufacturer - Cast Steel Sand Casting – RMC Foundry Detail:
As a sand casting foundry from China, RMC could cast the cast steel by sand casting. Cast steel can be divided into cast alloy steel and cast carbon steel according to its chemical composition, and can also be divided into cast tool steel, cast special steel, engineering and structural casting and cast alloy steel according to its characteristics.
By chemical composition
1. Cast carbon steel. Cast steel with carbon as the main alloying element and a small amount of other elements. Cast carbon steel can be divided into cast low carbon steel, cast medium carbon steel and cast high carbon steel. The carbon content of cast low carbon steel is less than 0.25%, the carbon content of cast carbon steel is between 0.25% and 0.60%, and the carbon content of cast high carbon steel is between 0.6% and 3.0%. The strength and hardness of cast carbon steel increase with the increase of carbon content. Cast carbon steel has the following advantages: lower production cost, higher strength, better toughness and higher plasticity. Cast carbon steel can be used to manufacture parts that bear heavy loads, such as steel rolling mill stands and hydraulic press bases in heavy machinery. It can also be used to manufacture parts that are subject to large forces and impact, such as wheels, couplers, bolsters and side frames on railway vehicles.
2. Cast alloy steel. Casting alloy steel can be divided into cast low alloy steel (the total alloy elements are less than or equal to 5%), cast alloy steel (the total alloy elements are 5% to 10%) and cast high alloy steel (the total alloy elements are greater than or equal 10%).
By use characteristics
1. Casting tool steel. Cast tool steel can be divided into casting tool steel and casting mold steel.
2. Casting special steel. Casting special steel can be divided into cast stainless steel, cast heat-resistant steel, cast wear-resistant steel, cast nickel-based alloy, etc.
3. Cast steel for engineering and structure. Cast steel for engineering and structure can be divided into cast carbon structural steel and cast alloy structural steel.
4. Cast alloy steel. It can be divided into cast low alloy steel, cast medium alloy steel and cast high alloy steel.
304 and 316 cast stainless steel are the most widely used stainless steels. Both are austenitic cast steels, non-magnetic or weakly magnetic. The 430, 403, and 410 are austenitic-ferritic stainless steels with magnetic properties.
▶ Raw Materials of Cast Steel as per standard or customized chemical compositions and mechanical properties.
• Carbon Steel: AISI 1020 – AISI 1060,
• Steel Alloys: ZG20SiMn, ZG30SiMn, ZG30CrMo, ZG35CrMo, ZG35SiMn, ZG35CrMnSi, ZG40Mn, ZG40Cr, ZG42Cr, ZG42CrMo…etc on request.
• Stainless Steel: AISI 304, AISI 304L, AISI 316, AISI 316L, 1.4404, 1.4301 and other stainless steel grade.
▶ Capabilities of Sand Casting moulded by hand:
• Max Size: 1,500 mm × 1000 mm × 500 mm
• Weight Range: 0.5 kg – 500 kg
• Annual Capacity: 5,000 tons – 6,000 tons
• Tolerances: On Request.
▶ Capabilities of Sand Casting by Automatic Molding Machines:
• Max Size: 1,000 mm × 800 mm × 500 mm
• Weight Range: 0.5 kg – 500 kg
• Annual Capacity: 8,000 tons – 10,000 tons
• Tolerances: On Request.
▶ Main Production Procedure
• Patterns & Tooling Design → Making Patterns → Moulding Process → Chemical Composition Analysis → Melting & Pouring → Cleaning, Grinding & Shot Blasting → Post Processing or Packing for Shipment
▶ Sand Casting Inspection Capabilities
• Spectrographic and manual quantitative analysis
• Metallographic analysis
• Brinell, Rockwell and Vickers hardness inspection
• Mechanical property analysis
• Low and normal temperature impact testing
• Cleanliness inspection
• UT, MT and RT inspection
▶ Post-Casting Process
• Deburring & Cleaning
• Shot Blasting / Sand Peening
• Heat Treatment: Normalization, Quench, Tempering, Carburization, Nitriding
• Surface Treatment: Passivation, Andonizing, Electroplating, Hot Zinc Plating, Zinc Plating, Nickel Plating, Polishing, Electro-Polishing, Painting, GeoMet, Zintec
• CNC Machining: Turning, Milling, Lathing, Drilling, Honing, Grinding,
Cast Steel Alloys at Sand Casting Foundry of RMC
|
|||||||
No. | China | Japan | Korea | Germany | France | Russia гост | |
GB | JIS | KS | DIN | W-Nr. | NF | ||
1 | ZG40Mn | SCMn3 | SCMn3 | GS-40Mn5 | 1.1168 | - | - |
2 | ZG40Cr | - | - | - | - | - | 40Xл |
3 | ZG20SiMn | SCW480 (SCW49) | SCW480 | GS-20Mn5 | 1.112 | G20M6 | 20гсл |
4 | ZG35SiMn | SCSiMn2 | SCSiMn2 | GS-37MnSi5 | 1.5122 | - | 35гсл |
5 | ZG35CrMo | SCCrM3 | SCCrM3 | GS-34CrMo4 | 1.722 | G35CrMo4 | 35XMл |
6 | ZG35CrMnSi | SCMnCr3 | SCMnCr3 | - | - | - | 35Xгсл |
Product detail pictures:
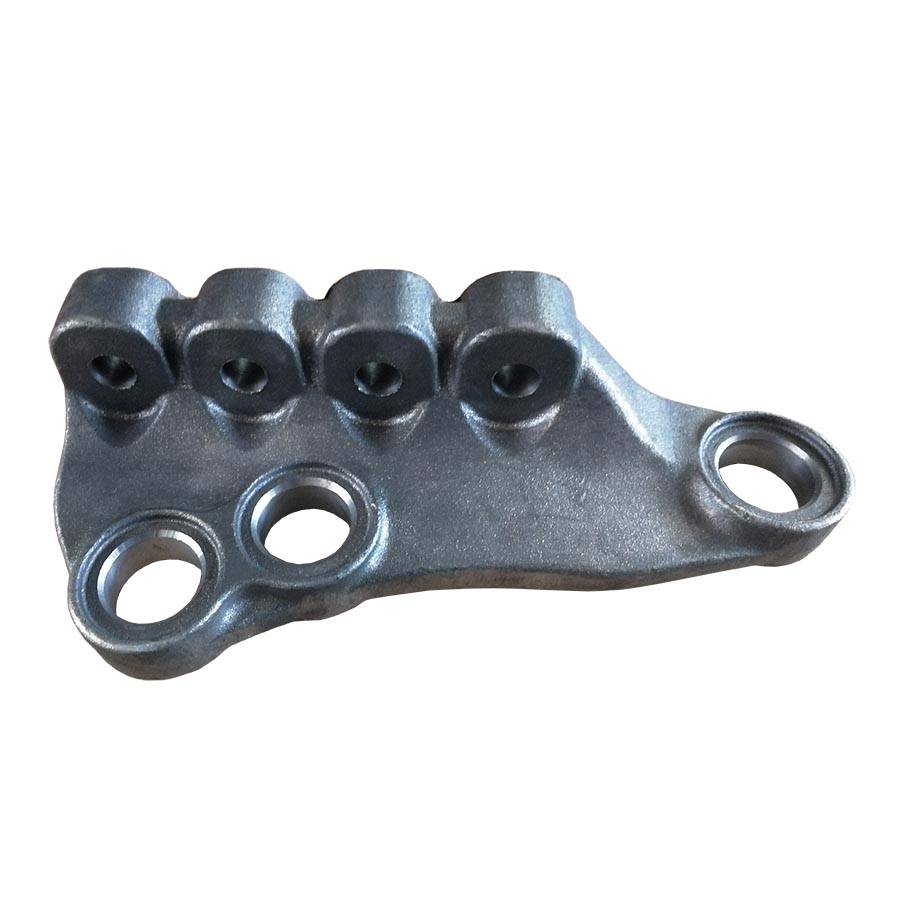
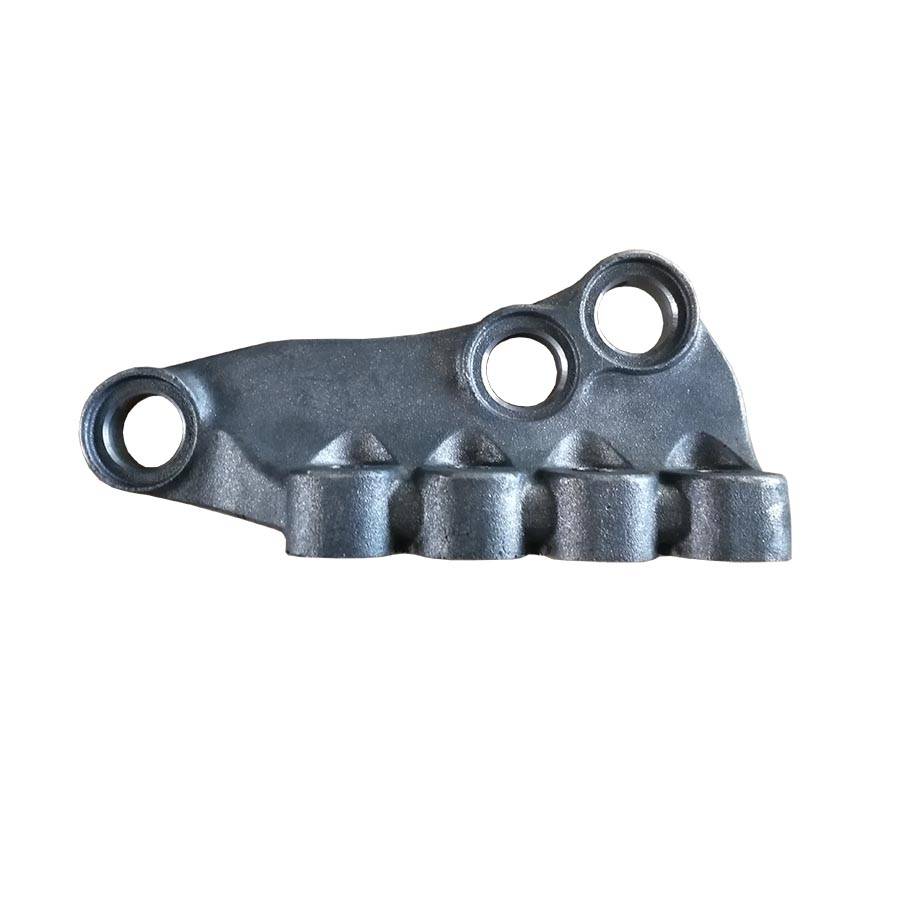
Related Product Guide:
With our leading technology also as our spirit of innovation,mutual cooperation, benefits and advancement, we'll build a prosperous future together with your esteemed organization for Bottom price Ductile Iron Sand Casting Manufacturer - Cast Steel Sand Casting – RMC Foundry, The product will supply to all over the world, such as: French , Egypt , Lyon , If any product meed your demand, remember to feel free to contact us. We're sure your any inquiry or requirement will get prompt attention, high-quality merchandise, preferential prices and cheap freight. Sincerely welcome friends all over the world to call or come to visit, to discuss cooperation for a better future!

We have been looking for a professional and responsible supplier, and now we find it.

-
Factory wholesale Carbon Steel Casting Company ...
-
China Gold Supplier for Steel Shell Casting Fou...
-
Chinese wholesale Shell Mold Casting Manufactur...
-
Hot sale Alloy Steel Vacuum Casting Foundry - ...
-
Fixed Competitive Price Malleable Casting Compa...
-
Factory wholesale Ductile Iron Casting Parts - ...