Super Lowest Price Ductile Iron Investment Casting Foundry – Water Glass Investment Casting of Alloy Steel – RMC Foundry Detail:
Custom alloy steel casting machinery spare parts by lost wax investment casting process. with water glass (the aqueous solution of sodium silicate) as the binder materials for shell making. The quality of shell making influent the accuracy of the final castings and therefore is a very critical process during investment casting. The quality of the shell is directly related to the roughness and dimensional tolerance of the final casting. Therefore, it is an important task for the investment casting foundry to choose a suitable manufacturing method for the mold shell. According to different adhesives or binder materials for making the mold shell, investment casting molds can be divided into water glass adhesive shells, silica sol adhesive shells, ethyl silicate adhesive shells and ethyl silicate-silica sol composite shells. These modeling methods are the most commonly used methods in investment casting.
Mold Shell by Water Glass (aqueous solution of sodium silicate)
The investment casting produced by the water glass shell casting has high surface roughness, low dimensional accuracy, short shell-making cycle and low price. This process is widely used in casting carbon steel, low alloy steel, aluminum alloy and copper alloy.
Mold Shell by Silica Sol Shell (a dispersion of nano-scale silica particles in water or solvent)
The silica sol investment casting has low roughness, high dimensional accuracy, and long shell-making cycle. This process is widely used in high-temperature heat-resistant alloy castings, heat-resistant steel castings, stainless steel castings, carbon steel castings, low alloy castings, aluminum alloy castings and copper alloy castings.
Mold Shell by Ethyl Silicate Shell
In investment casting, castings made by using ethyl silicate as a binder to make the shell have low surface roughness, high dimensional accuracy, and a long shell-making cycle. This process is widely used in heat-resistant alloy castings, heat-resistant steel castings, stainless steel castings, carbon steel castings, low alloy castings, aluminum alloy castings and copper alloy castings.
Carbon steel, low alloy steel, and tool steel castings are used in several industrial applications and environments. With their numerous grades, steel and their alloys can be heat-treated to improve its yield and tensile strength; and, adjust hardness or ductility to the engineer’s application needs or desired mechanical properties.
Wear-resistant alloy steel investment castings are the casting parts produced by lost wax investment casting process made of wear-resistant alloy steel. At RMC Foundry, the main sand casting processes we could use for wear-resistant alloy steel are green sand casting, resin coated sand casting, no-bake sand mold casting, lost foam casting, vacuum casting and investment casting. The heat treatment, surface treatment and CNC machining are also available at our factory as per your drawings and requirements.
Among a wide variety of casting alloys, wear-resistant cast steel is a very widely used alloy steel. Wear-resistant cast steel mainly improves the wear resistance of steel castings by adding different content of alloying elements, such as manganese, chromium, carbon, etc., to the alloy. At the same time, the wear resistance of wear-resistant steel castings also depends on the heat treatment method used by the foundry and the structure of the casting.
According to different wear characteristics, the wear of steel castings can be divided into abrasive wear, adhesive wear, fatigue wear, corrosion wear and fretting wear. Wear-resistant steel castings are mainly used in industrial fields with complex working conditions and high mechanical performance requirements, such as mining, metallurgy, construction, power, petrochemical, water conservancy, agriculture and transportation industries. Wear-resistant steel castings are mostly used in abrasion conditions with a certain impact load, such as grinding equipment, excavators, crushers, tractors, etc.
Equivalent Grade of Cast Alloy Steel from Different Markets | |||||||||
GROUPS | AISI | W-stoff | DIN | BS | SS | AFNOR | U.N.E. / I.H.A. | JIS | UNI |
Low Alloy Steel | 9255 | 1.0904 | 55 Si 7 | 250 A 53 | 2090 | 55 S 7 | 56Si7 | - | 5SSi8 |
1335 | 1.1167 | 36 Mn 5 | 150 M 36 | 2120 | 40 M 5 | 36Mn5 | SMn 438(H) | - | |
1330 | 1.1170 | 28 Mn 6 | 150 M 28 | - | 20 M 5 | - | SCMn1 | C28MN | |
P4 | 1.2341 | X6 CrMo 4 | - | - | - | - | - | - | |
52100 | 1.3505 | 100 Cr 6 | 534 A 99 | 2258 | 100 C 6 | F.131 | SUJ 2 | 100Cr6 | |
A204A | 1.5415 | 15 Mo 3 | 1501 240 | 2912 | 15 D 3 | 16 Mo3 | STBA 12 | 16Mo3 KW | |
8620 | 1.6523 | 21 NiCrMo 2 | 805 M 20 | 2506 | 20 NCD 2 | F.1522 | SNCM 220(H) | 20NiCrMo2 | |
8740 | 1.6546 | 40NiCrMo22 | 311-Type 7 | - | 40 NCD 2 | F.129 | SNCM 240 | 40NiCrMo2(KB) | |
- | 1.6587 | 17CrNiMo6 | 820 A 16 | - | 18 NCD 6 | 14NiCrMo13 | - | - | |
5132 | 1.7033 | 34 Cr 4 | 530 A 32 | - | 32 C 4 | 35Cr4 | SCr430(H) | 34Cr4(KB) | |
5140 | 1.7035 | 41 Cr 4 | 530 A 40 | - | 42 C 2 | 42 Cr 4 | SCr 440 (H) | 40Cr4 | |
5140 | 1.7035 | 41 Cr 4 | 530 A 40 | - | 42 C 2 | 42 Cr 4 | SCr 440 (H) | 41Cr4 KB | |
5140 | 1.7045 | 42 Cr 4 | 530 A 40 | 2245 | 42 C 4 TS | F.1207 | SCr 440 | - | |
5115 | 1.7131 | 16 MnCr 5 | (527 M 20) | 2511 | 16 MC 5 | F.1516 | - | 16MnCr5 | |
5155 | 1.7176 | 55 Cr 3 | 527 A 60 | 2253 | 55 C 3 | - | SUP 9(A) | 55Cr3 | |
4130 | 1.7218 | 25 CrMo 4 | 1717CDS 110 | 2225 | 25 CD 4 | F.1251/55Cr3 | SCM 420 / SCM430 | 25CrMo4(KB) | |
4135 (4137) | 1.7220 | 35 CrMo 4 | 708 A 37 | 2234 | 35 CD 4 | 34 CrMo 4 | SCM 432 | 34CrMo4KB | |
4142 | 1.7223 | 41 CrMo 4 | 708 M 40 | 2244 | 42 CD 4 TS | 42 CrMo 4 | SCM 440 | 41 CrMo 4 | |
4140 | 1.7225 | 42 CrMo 4 | 708 M 40 | 2244 | 40 CD 4 | F.1252 | SCM 440 | 40CrMo4 | |
4137 | 1.7225 | 42 CrMo 4 | 708 M 40 | 2244 | 42 CD 4 | F.1252 | SCM 440 | 42CrMo4 | |
A387 12-2 | 1.7337 | 16 CrMo 4 4 | 1501 620 | 2216 | 15 CD 4.5 | - | - | 12CrMo910 | |
- | 1.7361 | 32CrMo12 | 722 M 24 | 2240 | 30 CD 12 | F.124.A | - | 30CrMo12 | |
A182 F-22 | 1.7380 | 10 CrMo9 10 | 1501 622 | 2218 | 12 CD 9, 10 | F.155 / TU.H | - | 12CrMo9 10 | |
6150 | 1.8159 | 50 CrV 4 | 735 A 50 | 2230 | 50 CV 4 | F.143 | SUP 10 | 50CrV4 | |
- | 1.8515 | 31 CrMo 12 | 722 M 24 | 2240 | 30 CD 12 | F.1712 | - | 30CrMo12 | |
- | - | - | - | - | - | - | - | - | |
Medium Alloy Steel | W1 | 1.1545 | C105W1 | BW1A | 1880 | Y 105 | F.5118 | SK 3 | C100 KU |
L3 | 1.2067 | 100Cr6 | BL 3 | (2140) | Y 100 C 6 | F.520 L | - | - | |
L2 | 1.2210 | 115 CrV 3 | - | - | - | - | - | - | |
P20 + S | 1.2312 | 40 CrMnMoS 8 6 | - | - | 40 CMD 8 +S | X210CrW12 | - | - | |
- | 1.2419 | 105WCr6 | - | 2140 | 105W C 13 | F.5233 | SKS 31 | 107WCr5KU | |
O1 | 1.2510 | 100 MnCrW 4 | BO1 | - | 90MnWCrV5 | F.5220 | (SK53) | 95MnWCr5KU | |
S1 | 1.2542 | 45 WCrV 7 | BS1 | 2710 | 55W20 | F.5241 | - | 45WCrV8KU | |
4340 | 1.6582 | 34 CrNiMo 6 | 817 M 40 | 2541 | 35 NCD 6 | F.1280 | SNCM 447 | 35NiCrMo6KB | |
5120 | 1.7147 | 20 MnCr 5 | - | - | 20 MC 5 | - | - | - | |
- | - | - | - | - | - | - | - | - | |
Tool and High Alloy Steel | D3 | 1.2080 | X210 Cr 12 | BD3 | 2710 | Z200 C 12 | F.5212 | SKD 1 | X210Cr13KU |
P20 | 1.2311 | 40 CrMnMo 7 | - | - | 40 CMD 8 | F.5263 | - | - | |
H13 | 1.2344 | X40CrMoV 5 1 | BH13 | 2242 | Z 40 CDV 5 | F.5318 | SKD 61 | X40CrMoV511KU | |
A2 | 1.2363 | X100 CrMoV 5 1 | BA2 | 2260 | Z 100 CDV 5 | F.5227 | SKD 12 | X100CrMoV51KU | |
D2 | 1.2379 | X155 CrMoV 12 1 | BD2 | 2310 | Z 160 CDV 12 | F.520.A | SKD11 | X155CrVMo121KU | |
D4 (D6) | 1.2436 | X210 CrW 12 | BD6 | 2312 | Z 200 CD 12 | F.5213 | SKD 2 | X215CrW121KU | |
H21 | 1.2581 | X30WCrV9 3 | BH21 | - | Z 30 WCV 9 | F.526 | SKD5 | X30WCrV 9 3 KU | |
L6 | 1.2713 | 55NiCrMoV 6 | - | - | 55 NCDV 7 | F.520.S | SKT4 | - | |
M 35 | 1.3243 | S6/5/2/5 | BM 35 | 2723 | 6-5-2-5 | F.5613 | SKH 55 | HS6-5-5 | |
M 2 | 1.3343 | S6/5/2 | BM2 | 2722 | Z 85 WDCV | F.5603 | SKH 51 | HS6-5-2-2 | |
M 7 | 1.3348 | S2/9/2 | - | 2782 | 2 9 2 | - | - | HS2-9-2 | |
HW 3 | 1.4718 | X45CrSi 9 3 | 401 S 45 | - | Z 45 CS 9 | F.3220 | SUH1 | X45CrSi8 | |
- | 1.7321 | 20 MoCr 4 | - | 2625 | - | F.1523 | - | 30CrMo4 | |
High Tensile Strength Steel | A128 (A) | 1.3401 | G-X120 Mn 12 | BW10 | 2183 | Z 120 M 12 | F.8251 | SCMnH 1 | GX120Mn12 |
Capabilities of Investment Casting Foundry:
• Max Size: 1,000 mm × 800 mm × 500 mm
• Weight Range: 0.5 kg – 100 kg
• Annual Capacity: 2,000 tons
• Bond Materials for Shell Building: Silica Sol, Water Glass and their mixtures.
• Tolerances: On Request.
Advantages of Investment Casting Components:
- Excellent and smooth surface finish
- Tight dimensional tolerances.
- Complex and intricate shapes with design flexibility
- Capability to cast thin walls therefore a lighter casting component
- Wide selection of cast metals and alloys (ferrous and non-ferrous)
- Draft is not required in the molds design.
- Reduce the need for secondary machining.
- Low material waste.
Materials for Investment Casting Process at RMC Foundry | |||
Category | China Grade | US Grade | Germany Grade |
Ferritic Stainless Steel | 1Cr17, 022Cr12, 10Cr17, | 430, 431, 446, CA-15, CA6N, CA6NM | 1.4000, 1.4005, 1.4008, 1.4016, GX22CrNi17, GX4CrNi13-4 |
Martensitic Stainless Steel | 1Cr13, 2Cr13, 3Cr13, 4Cr13, | 410, 420, 430, 440B, 440C | 1.4021, 1.4027, 1.4028, 1.4057, 1.4059, 1.4104, 1.4112, 1.4116, 1.4120, 1.4122, 1.4125 |
Austenitic stainless steel | 06Cr19Ni10, 022Cr19Ni10, 06Cr25Ni20, 022Cr17Ni12Mo2, 03Cr18Ni16Mo5 |
302, 303, 304, 304L, 316, 316L, 329, CF3, CF3M, CF8, CF8M, CN7M, CN3MN | 1.3960, 1.4301, 1.4305, 1.4306, 1.4308, 1.4313, 1.4321, 1.4401, 1.4403, 1.4404, 1.4405, 1.4406, 1.4408, 1.4409, 1.4435, 1.4436, 1.4539, 1.4550, 1.4552, 1.4581, 1.4582, 1.4584, |
Precipitation Hardening Stainless Steel | 05Cr15Ni5Cu4Nb, 05Cr17Ni4Cu4Nb | 630, 634, 17-4PH, 15-5PH, CB7Cu-1 | 1.4542 |
Duplex Stainless Steel | 022Cr22Ni5Mo3N, 022Cr25Ni6Mo2N | A 890 1C, A 890 1A, A 890 3A, A 890 4A, A 890 5A, A 995 1B, A 995 4A, A 995 5A, 2205, 2507 |
1.4460, 1.4462, 1.4468, 1.4469, 1.4517, 1.4770 |
High Mn Steel | ZGMn13-1, ZGMn13-3, ZGMn13-5 | B2, B3, B4 | 1.3802, 1.3966, 1.3301, 1.3302 |
Tool Steel | Cr12 | A5, H12, S5 | 1.2344, 1.3343, 1.4528, GXCrMo17, X210Cr13, GX162CrMoV12 |
Heat Resistant Steel | 20Cr25Ni20, 16Cr23Ni13, 45Cr14Ni14W2Mo |
309, 310, CK20, CH20, HK30 | 1.4826, 1.4828, 1.4855, 1.4865 |
Nickle-base Alloy | HASTELLY-C, HASTELLY-X, SUPPER22H, CW-2M, CW-6M, CW-12MW, CX-2MW, HX(66Ni-17Cr), MRE-2, NA-22H, NW-22, M30C, M-35-1, INCOLOY600, INCOLOY625 |
2.4815, 2.4879, 2.4680 | |
Aluminum Alloy |
ZL101, ZL102, ZL104 | ASTM A356, ASTM A413, ASTM A360 | G-AlSi7Mg, G-Al12 |
Copper Alloy | H96, H85, H65, HPb63-3, HPb59-1, QSn6.5-0.1, QSn7-0.2 |
C21000, C23000, C27000, C34500, C37710, C86500, C87600, C87400, C87800, C52100, C51100 | CuZn5, CuZn15, CuZn35, CuZn36Pb3, CuZn40Pb2, CuSn10P1, CuSn5ZnPb, CuSn5Zn5Pb5 |
Cobalt-base Alloy | UMC50, 670, Grade 31 | 2.4778 |
INVESTMENT CASTING TOLERANCES | |||
Inches | Millimeters | ||
Dimension | Tolerance | Dimension | Tolerance |
Up to 0.500 | ±.004″ | Up to 12.0 | ± 0.10mm |
0.500 to 1.000” | ±.006″ | 12.0 to 25.0 | ± 0.15mm |
1.000 to 1.500” | ±.008″ | 25.0 to 37.0 | ± 0.20mm |
1.500 to 2.000” | ±.010″ | 37.0 to 50.0 | ± 0.25mm |
2.000 to 2.500” | ±.012″ | 50.0 to 62.0 | ± 0.30mm |
2.500 to 3.500” | ±.014″ | 62.0 to 87.0 | ± 0.35mm |
3.500 to 5.000” | ±.017″ | 87.0 to 125.0 | ± 0.40mm |
5.000 to 7.500” | ±.020″ | 125.0 to190.0 | ± 0.50mm |
7.500 to 10.000” | ±.022″ | 190.0 to 250.0 | ± 0.57mm |
10.000 to 12.500” | ±.025″ | 250.0 to 312.0 | ± 0.60mm |
12.500 to 15.000 | ±.028″ | 312.0 to 375.0 | ± 0.70mm |
OEM Custom Investment Casting Products
Product detail pictures:
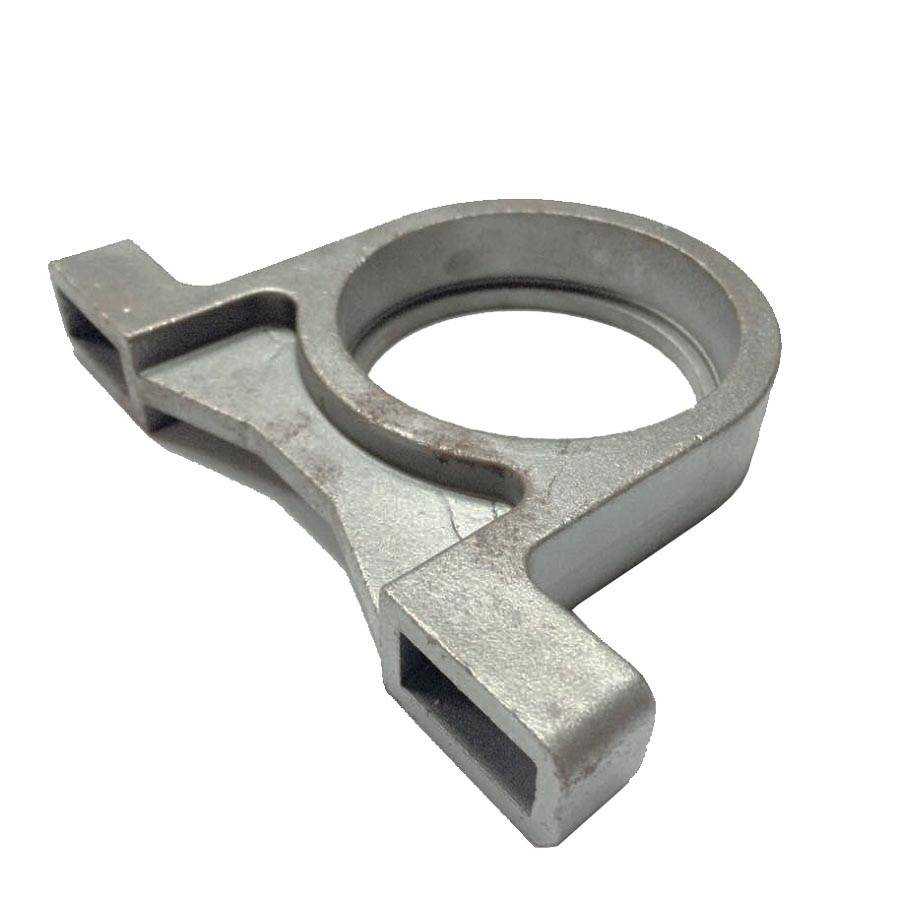
Related Product Guide:
We thinks what prospects think, the urgency of urgency to act from the interests of a client position of theory, allowing for greater high-quality, reduced processing costs, rates are much more reasonable, won the new and previous consumers the support and affirmation for Super Lowest Price Ductile Iron Investment Casting Foundry – Water Glass Investment Casting of Alloy Steel – RMC Foundry, The product will supply to all over the world, such as: Puerto Rico , Sydney , Luxembourg , We'd like to invite customers from abroad to discuss business with us. We can provide our clients with high quality products and excellent service. We are sure that we will have good cooperative relationships and make a brilliant future for both parties.

This is a very professional wholesaler, we always come to their company for procurement, good quality and cheap.

-
8 Year Exporter Ductile Iron Foundry - Custom ...
-
Factory wholesale Carbon Steel Casting Company ...
-
High reputation Alloy Steel Lost Wax Casting Pr...
-
2020 New Style Bronze Green Sand Casting - Duc...
-
Hot New Products Lost Foam Casting Supplier - ...
-
2020 Latest Design Stainless Steel Precision Ca...