Manufacturer for Shell Mold Casting Factory - Gray Cast Iron Shell Casting Product – RMC Foundry Detail:
China OEM custom gray cast iron shell mold casting products with CNC machining service.
Property | Gray Cast Iron | Melleable iron | Ductile Iron | C30 steel |
Melt temperature, ℃ | 1175 | 1200 | 1150 | 1450 |
Specific gravity, kg/m³ | 6920 | 6920 | 6920 | 7750 |
Vibration damping | Exellent | Good | Good | Poor |
Modulus of elasticity, MPa | 126174 | 175126 | 173745 | 210290 |
Modolus of rigidiy, MPa | 48955 | 70329 | 66190 | 78600 |
Shell molding casting process is also called pre-coated resin sand casting process, hot shell molding castings or core casting process. The main molding material is the pre-coated phenolic resin sand, which is more expensive than green sand and furan resin sand. Moreover, this sand can not be recycle used.
Furan resin self-hardening sand casting process (nobake process) uses the furan resin coated sand to form the casting mold. After mixing the original sand (or reclaimed sand), liquid furan resin and liquid catalyst evenly, and filling them into the core box (or sand box), and then tighten it to harden into a mold or mold in the core box (or sand box) at room temperature. Then the casting mould or casting core were formed, which is called self-hardening cold-core box molding (core), or self-hardening method (core).
Because the mold is formed at room temperature and no need to heat, the self-hardening sand casting is also called no-bake casting process. The self-hardening method can be divided into acid-catalyzed furan resin and phenolic resin sand self-hardening method, urethane resin sand self-hardening method and phenolic monoester self-hardening method.
As a self-hardening cold box binder sand, furan resin sand is the earliest and currently most widely used synthetic binder sand in Chinese foundry. The amount of resin added in molding sand is generally 0.7% to 1.0%, and the amount of added resin in core sand is generally 0.9% to 1.1%. The content of free aldehyde in furan resin is below 0.3%, and some factories have dropped to below 0.1%. In the foundries in China, the furan resin self-hardening sand has reached the international level regardless of the production process and the surface quality of the castings.
Resin Coated Sand Casting Metal and Alloys | |
Metal & Alloys | Popular Grade |
Gray Cast Iron | GG10~GG40; GJL-100 ~ GJL-350; |
Ductile (Nodular) Cast Iron | GGG40 ~ GGG80; GJS-400-18, GJS-40-15, GJS-450-10, GJS-500-7, GJS-600-3, GJS-700-2, GJS-800-2 |
Austempered Ductile Iron (ADI) | EN-GJS-800-8, EN-GJS-1000-5, EN-GJS-1200-2 |
Carbon Steel | C20, C25, C30, C45 |
Alloy Steel | 20Mn, 45Mn, ZG20Cr, 40Cr, 20Mn5, 16CrMo4, 42CrMo, 40CrV, 20CrNiMo, GCr15, 9Mn2V |
Stainless Steel | Ferritic Stainless Steel, Martensitic Stainless Steel, Austenitic Stainless Steel, Precipitation Hardening Stainless Steel, Duplex Stainless Steel |
Aluminium Alloys | ASTM A356, ASTM A413, ASTM A360 |
Brass / Copper-based Alloys | C21000, C23000, C27000, C34500, C37710, C86500, C87600, C87400, C87800, C52100, C51100 |
Standard: ASTM, SAE, AISI, GOST, DIN, EN, ISO, and GB |
The Advantages of Furan Resin Coated Sand Self-hardening Molding Casting:
1) Improve the dimensional accuracy of castings and the surface roughness.
2) The hardening of the mold (core) sand does not require drying, which can save energy, and inexpensive wood or plastic core boxes and templates can also be used.
3) Self-hardnening molding sand is easy to compact and collapse, easy to clean up castings, and old sand can be recycled and reused, which greatly reduces the labor intensity of core making, modeling, sand falling, cleaning and other links, and it is easy to realize mechanization or automation.
4) The mass fraction of resin in sand is only 0.8%~2.0%, and the comprehensive cost of raw materials is low.
Because the self-hardening method has many of the above-mentioned unique advantages, the self-hardening method is not only used for core making, but also used for casting moulding. It is especially suitable for single piece and small batch production, and can produce cast iron, cast steel and non-ferrous alloy castings. Some Chinese foundries have completely replaced clay dry sand molds, cement sand molds, and partially replaced water glass sand molds.
Ductile Cast Iron Products
Ductile Iron Casting Products
Product detail pictures:
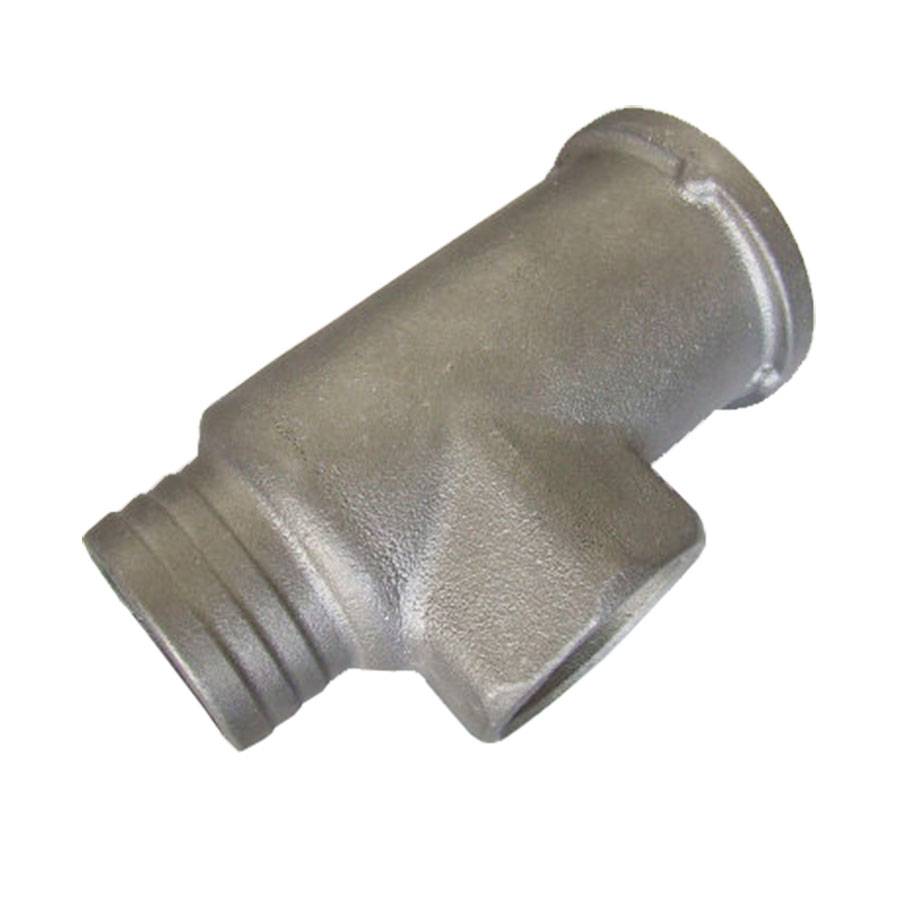
Related Product Guide:
Having a sound small business credit score, outstanding after-sales services and modern manufacturing facilities, we've got earned an fantastic reputation among our buyers across the globe for Manufacturer for Shell Mold Casting Factory - Gray Cast Iron Shell Casting Product – RMC Foundry, The product will supply to all over the world, such as: Sevilla , Sacramento , Mauritania , Whether selecting a current product from our catalog or seeking engineering assistance for your application, you can talk to our customer service center about your sourcing requirements. We can provided good quality with competitive price for you.

Perfect services, quality products and competitive prices, we have work many times, every time is delighted, wish continue to maintain!

-
Manufactur standard Alloy Steel Foundry - Shel...
-
2020 Latest Design Stainless Steel Precision Ca...
-
Best Price on Brass No Bake Casting - Lost Foa...
-
High Quality for Duplex Stainless Steel Casting...
-
High reputation Alloy Steel Lost Wax Casting Pr...
-
OEM/ODM China Stainless Steel Shell Mold Castin...