Europe style for Aluminium Alloy Lost Wax Casting - Steel Green Sand Casting Foundry – RMC Foundry Detail:
Green sand casting has no need to dry and takes the bentonite as binder. The basic feature of green sand is that it does not need to be dried and solidified, while it has a certain wet strength. Although the strength is low, it has better retreatability and is easy to shake off; moreover, the green sand casting process has several advantages of high moulding efficiency, short production cycle, low material cost and it is easy to organize flow production. However, because the sand mold is not dried, moisture vaporization and migration appear on the surface of the sand mold during casting, which makes the casting prone to have blowholes, sand inclusions, bulging sand, sticky sand and other casting defects.
In order to give full play to the advantages of green sand molding and improve the quality of castings, it is necessary to maintain stable molding sand performance, compact and uniform sand molds and reasonable casting process during the production process. Therefore, the development of green sand molding technology has always been closely linked to the development of molding machine and molding technology.
Recently, green sand mechanized moulding has developed from ordinary machine moulding to high-density machine moulding. The productivity of moulding, the compactness of sand molds, and the dimensional accuracy of castings continue to increase, while the surface roughness value of castings continues to decrease. Green sand moulding casting process (when paint is not applied) can also produce iron castings weighing several hundred kilograms.
Green sand is generally composed of new sand, old sand, bentonite, addenda and a proper amount of water. Before formulating the ratio of molding sand, it is necessary to determine the performance range and control target value of the molding sand according to the type of alloy poured, the characteristics and requirements of the casting, the molding method and the process and the cleaning method. After that, according to the variety and specifications of various raw materials, sand processing method, equipment, sand to iron ratio and the burning loss ratio of various materials are used to formulate the sand ratio. The technical indicators and proportions of molding sand can only be determined after long-term production verification.
▶ Capabilities of Sand Casting moulded by hand at Green Sand Foundry of RMC:
• Max Size: 1,500 mm × 1000 mm × 500 mm
• Weight Range: 0.5 kg – 500 kg
• Annual Capacity: 5,000 tons – 6,000 tons
• Tolerances: On Request or Standard
• Mold Materials: Green Sand Casting, Shell Mold Sand Casting.
▶ Capabilities of Sand Casting by Automatic Molding Machines:
• Max Size: 1,000 mm × 800 mm × 500 mm
• Weight Range: 0.5 kg – 500 kg
• Annual Capacity: 8,000 tons – 10,000 tons
• Tolerances: On Request.
• Mold Materials: Green Sand Casting, Shell Mold Sand Casting.
▶ Materials Available for Sand Casting Foundry at RMC:
• Brass, Red Copper, Bronze or other Copper-based alloy metals: ZCuZn39Pb3, ZCuZn39Pb2, ZCuZn38Mn2Pb2, ZCuZn40Pb2, ZCuZn16Si4
• Gray Cast Iron: HT150, HT200, HT250, HT300, HT350; GJL-100, GJL-150, GJL-200, GJL-250, GJL-300, GJL-350; GG10~GG40.
• Ductile Cast Iron or Nodular Cast Iron: GGG40, GGG50, GGG60, GGG70, GGG80; GJS-400-18, GJS-40-15, GJS-450-10, GJS-500-7, GJS-600-3, GJS-700-2, GJS-800-2; QT400-18, QT450-10, QT500-7, QT600-3, QT700-2, QT800-2;
• Aluminium and Their Alloys
• Other Materials as per your unique requirements or according to ASTM, SAE, AISI, ACI, DIN, EN, ISO, and GB standards
Product detail pictures:
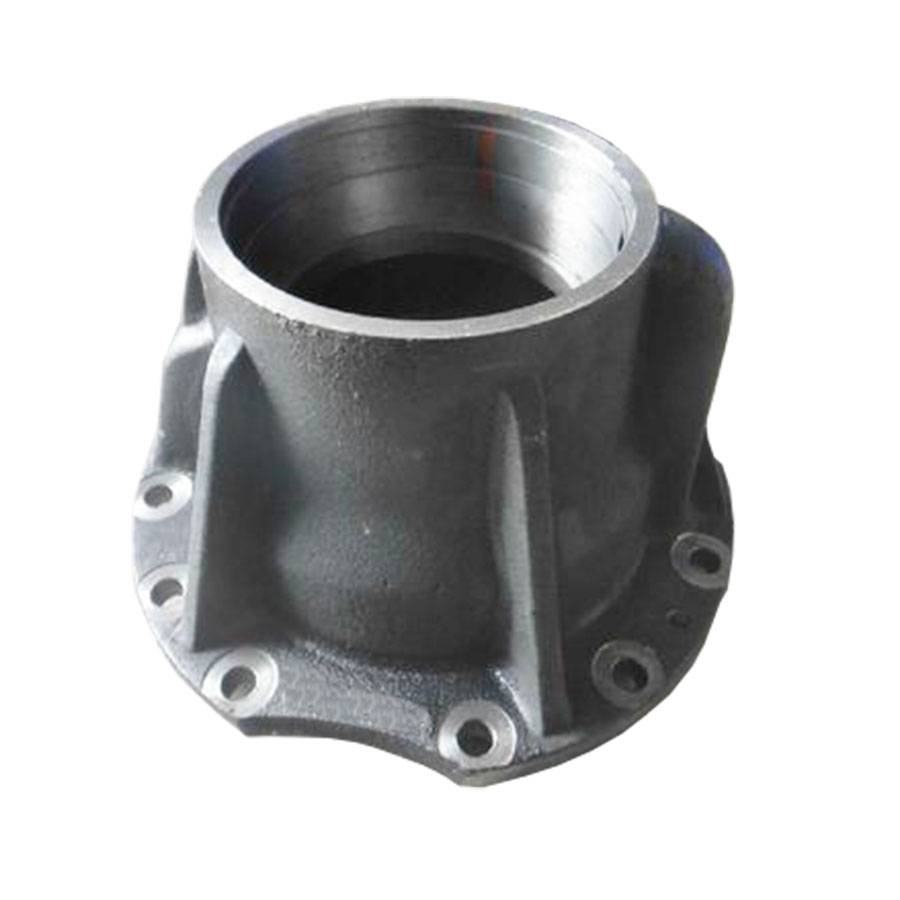
Related Product Guide:
We always continually offer you the most conscientious purchaser services, and the widest variety of designs and styles with finest materials. These efforts include the availability of customized designs with speed and dispatch for Europe style for Aluminium Alloy Lost Wax Casting - Steel Green Sand Casting Foundry – RMC Foundry, The product will supply to all over the world, such as: Guatemala , Munich , Georgia , We only supply quality items and we believe this is the only way to keep business continue. We can supply custom service too such as Logo, custom size, or custom merchandise etc that can according to customer's requirement.

The factory has advanced equipment, experienced staffs and good management level, so product quality had assurance, this cooperation is very relaxed and happy!

-
Super Purchasing for Ductile Iron Casting Facto...
-
Europe style for Aluminium Sand Casting Foundry...
-
China Gold Supplier for Steel Shell Casting Fou...
-
China Factory for Cast Steel Foundry - Lost Wa...
-
OEM/ODM China Stainless Steel Shell Mold Castin...
-
Best Price for Alloy Steel Sand Casting - Gray...