Cheapest Price Duplex Stainless Steel Sand Casting - Custom Ductile Iron Sand Casting – RMC Foundry Detail:
Custom Ductile Cast Iron Sand Casting Products from China with Custom and CNC Machining Services.
Cast iron is an iron-carbon cast alloy with other elements that is made by remelting pig iron, scrap, and other additions. For differentiation from steel and cast steel, cast iron is defined as a cast alloy with a carbon content (min 2.03%) that ensures the solidification of the final phase with a eutectic transformation.
When graphite is present as small, round, and well-distributed particles, its weakening effect is small and such cast irons would have higher ductility. This type of cast iron is called ductile or nodular iron or spheroidal graphite or simply SG iron. This form of graphite can be achieved by adding elemental magnesium or cerium or a combination of the two elements to molten cast iron. Magnesium is added in quantities of 0.07 to 0. 10% followed by the addition of ferro-silicon to promote graphitization. During solidification, magnesium helps in the distribution of graphite throughout the metal.
Ductile iron has better strength-to-weight ratio, better machinability and higher impact value. Moreove, the ductile iron components are produced by casting process wherein better control of component shape can be achieved compared to drop forging. Thus, many a component such as crank shafts and connecting rods manufactured usually by drop forging is increasingly being replaced by ductile iron castings.
Depending on chemical specifications, cast irons can be non- alloyed or alloyed. The range of alloyed irons is much wider, and they contain either higher amounts of common components, such as silicon and manganese, or special additions, such as nickel, chromium, aluminum, molybdenum, tungsten, copper, vana- dium, titanium, plus others. Generally speaking, the cast iron could be divided into gray iron, ducitle iron (nodular iron), white cast iron, compacted graphite iron and malleable cast iron.
Raw Materials Available for Sand Casting
• Gray Iron: GJL-100, GJL-150, GJL-200, GJL-250, GJL-300, GJL-350
• Ductile Iron: GJS-400-18, GJS-40-15, GJS-450-10, GJS-500-7, GJS-600-3, GJS-700-2, GJS-800-2
• Aluminium and Their Alloys
• Other Materials and Standards on request
Capabilities of Sand Casting:
• Max Size (by automatic molding line): 1,500 mm × 1000 mm × 500 mm
• Max Size (by handle molding): 1,000 mm × 800 mm × 500 mm
• Weight Range: 0.5 kg – 500 kg
• Annual Capacity: 7,000 tons – 8,000 tons
• Tolerances: On Request.
Main Production Procedure
Patterns & Tooling Design → Making Patterns → Moulding Process → Chemical Composition Analysis → Melting & Pouring → Cleaning, Grinding & Shot Blasting → Post Processing or Packing for Shipment
Sand Casting Inspection Capabilities
• Spectrographic and manual quantitative analysis
• Metallographic analysis
• Brinell, Rockwell and Vickers hardness inspection
• Mechanical property analysis
• Low and normal temperature impact testing
• Cleanliness inspection
• UT, MT and RT inspection
Post-Casting Process
• Deburring & Cleaning
• Shot Blasting / Sand Peening
• Heat Treatment: Normalization, Quench, Tempering, Carburization, Nitriding
• Surface Treatment: Passivation, Andonizing, Electroplating, Hot Zinc Plating, Zinc Plating, Nickel Plating, Polishing, Electro-Polishing, Painting, GeoMet, Zintec
• CNC Machining: Turning, Milling, Lathing, Drilling, Honing, Grinding,
General Commerial Terms
• Main work flow: Inquiry & Quotation → Confirming Details / Cost Reduction Proposals → Tooling Development → Trial Casting → Samples Approval → Trial Order → Mass Production → Continuous Order Proceeding
• Lead time: Estimatedly 15-25 days for tooling development and estimatedly 20 days for mass production.
• Payment Terms: To be negotiated.
• Payment methods: T/T, L/C, West Union, Paypal.
Product detail pictures:
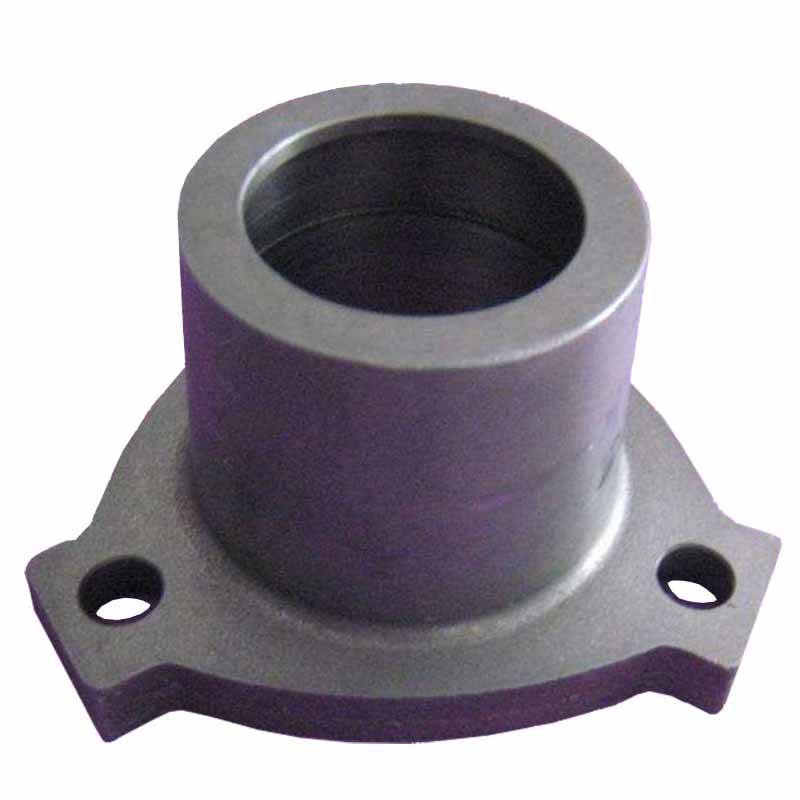
Related Product Guide:
We rely upon strategic thinking, constant modernisation in all segments, technological advances and of course upon our employees that directly participate in our success for Cheapest Price Duplex Stainless Steel Sand Casting - Custom Ductile Iron Sand Casting – RMC Foundry, The product will supply to all over the world, such as: Danish , Chile , Finland , Based on our guiding principle of quality is the key to development, we continually strive to exceed our customers' expectations. As such, we sincerely invite all interested companies to contact us for future cooperation, We welcome old and new customers to hold hands together for exploring and developing; For more information, be sure to feel free to contact us. Thanks. Advanced equipment, strict quality control, customer-orientation service, initiative summary and improvement of defects and extensive industry experience enable us to guarantee more customer satisfaction and reputation which, in return, brings us more orders and benefits. If you are interested in any of our merchandise, make sure you feel free to contact us. Inquiry or visit to our company are warmly welcome. We sincerely hope to start a win-win and friendly partnership with you. You can see more details in our website.

The product manager is a very hot and professional person, we have a pleasant conversation, and finally we reached a consensus agreement.

-
Super Lowest Price Sand Mold Casting - Alloy S...
-
2020 New Style Malleable Casting Foundry - Cob...
-
Fast delivery Malleable Iron Sand Casting Compa...
-
Manufacturing Companies for Alloy Steel No Bake...
-
Excellent quality Precision Casting Parts - Cu...
-
Low price for Precision Casting Products - CNC...