Bottom price Ductile Iron Sand Casting Manufacturer - Steel Sand Casting Company – RMC Foundry Detail:
Custom Wear-resistant Castings from Sand Casting Company in China with Custom and CNC Machining Services.
Among a wide variety of casting alloys, wear-resistant cast steel is a very widely used alloy steel. Wear-resistant cast steel mainly improves the wear resistance of steel castings by adding different content of alloying elements, such as manganese, chromium, carbon, etc., to the alloy. At the same time, the wear resistance of wear-resistant steel castings also depends on the heat treatment method used by the foundry and the structure of the casting.
Wear-resistant alloy steel sand castings are the casting parts produced by sand casting process made of wear-resistant alloy steel. At RMC Foundry, the main sand casting processes we could use for wear-resistant alloy steel are green sand casting, resin coated sand casting, no-bake sand mold casting, lost foam casting, vacuum casting and investment casting. The heat treatment, surface treatment and CNC machining are also available at our factory as per your drawings and requirements.
Raw Materials Available for Sand Casting
• Cast carbon steel: cast low carbon steel, cast medium carbon steel, cast high carbon steel (high strength carbon steel)
• Medium-alloy steel and low-alloy steel for casting: cast manganese steel, cast silico-manganese steel, cast manganese-molybdenum steel, cast manganese-molybdenum-vanadium copper steel, cast chromium steel, chromium-molybdenum cast steel, chromium-manganese-silicon cast steel, chromium-manganese Molybdenum cast steel, chromium molybdenum vanadium cast steel, chromium copper cast steel, molybdenum cast steel, chromium nickel molybdenum cast steel, etc. Different chemical elements can play a different role in improving the corresponding performance. In the following articles, we will introduce the properties of related alloy steels and the roles played by chemical elements one by one.
• Corrosion-resistant stainless steel: ferritic stainless steel, martensitic stainless steel, austenitic stainless steel and austenitic-ferritic duplex stainless steel.
• Heat-resistant steel: high chromium steel, high chromium nickel steel and high nickel chromium steel.
• Wear-resistant cast steel: wear-resistant manganese steel, wear-resistant chromium steel
• Casting special steel and professional steel: low-temperature cast steel, foundry tool steel (die steel), pressure cast steel, precision casting steel, centrifugal cast cast steel pipe.
• Gray Iron: GJL-100, GJL-150, GJL-200, GJL-250, GJL-300, GJL-350
• Ductile Iron: GJS-400-18, GJS-40-15, GJS-450-10, GJS-500-7, GJS-600-3, GJS-700-2, GJS-800-2
• Aluminium and Their Alloys
• Other Materials and Standards on request
Capabilities of Sand Casting:
• Max Size (by automatic molding line): 1,500 mm × 1000 mm × 500 mm
• Max Size (by handle molding): 1,000 mm × 800 mm × 500 mm
• Weight Range: 0.5 kg – 500 kg
• Annual Capacity: 7,000 tons – 8,000 tons
• Tolerances: On Request.
Main Production Procedure
Patterns & Tooling Design → Making Patterns → Moulding Process → Chemical Composition Analysis → Melting & Pouring → Cleaning, Grinding & Shot Blasting → Post Processing or Packing for Shipment
Sand Casting Inspection Capabilities
• Spectrographic and manual quantitative analysis
• Metallographic analysis
• Brinell, Rockwell and Vickers hardness inspection
• Mechanical property analysis
• Low and normal temperature impact testing
• Cleanliness inspection
• UT, MT and RT inspection
Post-Casting Process
• Deburring & Cleaning
• Shot Blasting / Sand Peening
• Heat Treatment: Normalization, Quench, Tempering, Carburization, Nitriding
• Surface Treatment: Passivation, Andonizing, Electroplating, Hot Zinc Plating, Zinc Plating, Nickel Plating, Polishing, Electro-Polishing, Painting, GeoMet, Zintec
• Machining: Turning, Milling, Lathing, Drilling, Honing, Grinding,
General Commerial Terms
• Main work flow: Inquiry & Quotation → Confirming Details / Cost Reduction Proposals → Tooling Development → Trial Casting → Samples Approval → Trial Order → Mass Production → Continuous Order Proceeding
• Lead time: Estimatedly 15-25 days for tooling development and estimatedly 20 days for mass production.
• Payment Terms: To be negotiated.
• Payment methods: T/T, L/C, West Union, Paypal.
Product detail pictures:
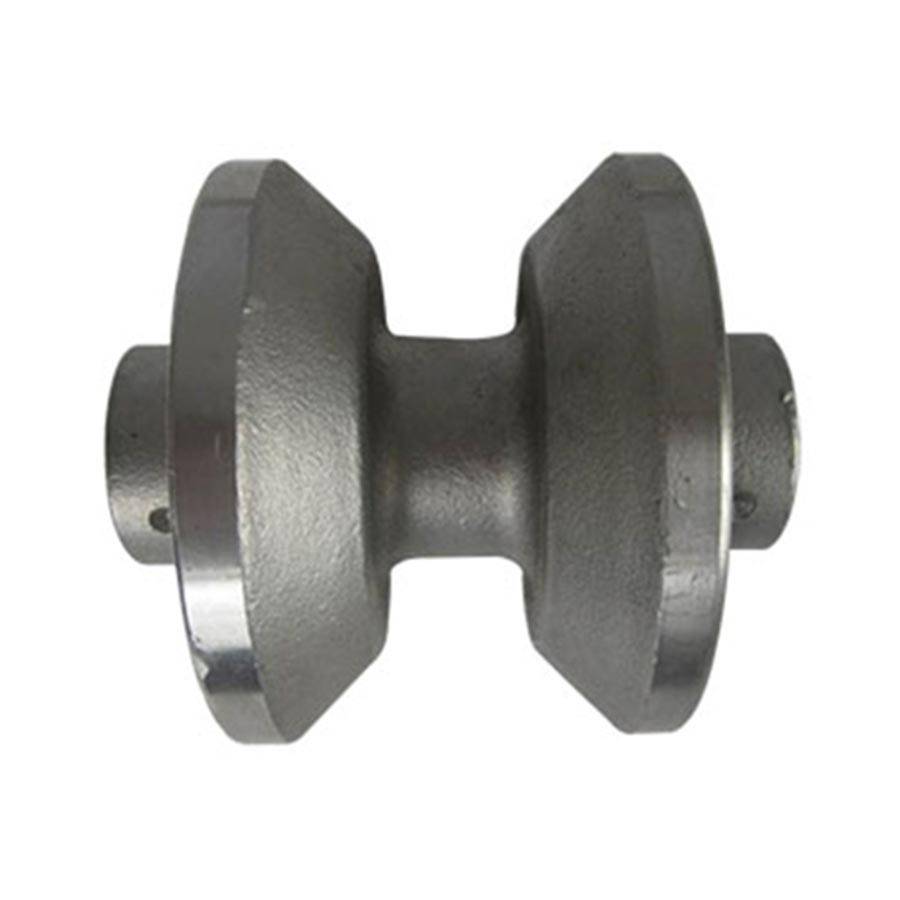
Related Product Guide:
Well-run equipment, professional sales team, and better after-sales services; We are also a unified big family, everyone stick to the company value "unification, dedication, tolerance" for Bottom price Ductile Iron Sand Casting Manufacturer - Steel Sand Casting Company – RMC Foundry, The product will supply to all over the world, such as: Nepal , Johor , Rwanda , Our products are widely recognized and trusted by users and can meet continuously developing economic and social needs. We welcome new and old customers from all walks of life to contact us for future business relationships and achieving mutual success!

Hope that the company could stick to the enterprise spirit of "Quality, Efficiency, Innovation and Integrity", it will be better and better in the future.

-
Super Lowest Price Sand Mold Casting - Alumini...
-
Good quality Stainless Steel Casting Parts - A...
-
Factory Cheap Hot Stainless Steel Precision Cas...
-
China Cheap price Stainless Steel Vacuum Castin...
-
Reasonable price Solid Mold Casting - Stainles...
-
Best Price on Duplex Stainless Steel Green Sand...