The exhaust manifold is connected to the engine cylinder block, and collects the exhaust of each cylinder and guides it into the exhaust main pipe with divergent pipes. The main requirement for it is to minimize the exhaust resistance and avoid mutual interference between the cylinders. When the exhaust is too concentrated, there will be mutual interference between the cylinders, that is, when a cylinder exhausts, it just hits the exhaust gas that has not been completely exhausted from other cylinders. In this way, the exhaust resistance will increase, thereby reducing the output power of the engine. The solution to this problem is to separate the exhaust of each cylinder as much as possible, with one branch for each cylinder, or one branch for two cylinders, and make each branch as long as possible and independently molded to reduce the mutual influence of gases in different pipes.
The exhaust manifold should take into account the engine power performance, engine fuel economy performance, emission standards, engine cost, matching vehicle front cabin layout and temperature field, etc. The exhaust manifolds commonly used on engines at present are divided into cast iron manifolds and stainless steel manifolds in terms of materials. From the manufacturing process, the exhaust manifold is realized by casting process, especially by lost wax casting due to their complex structure.
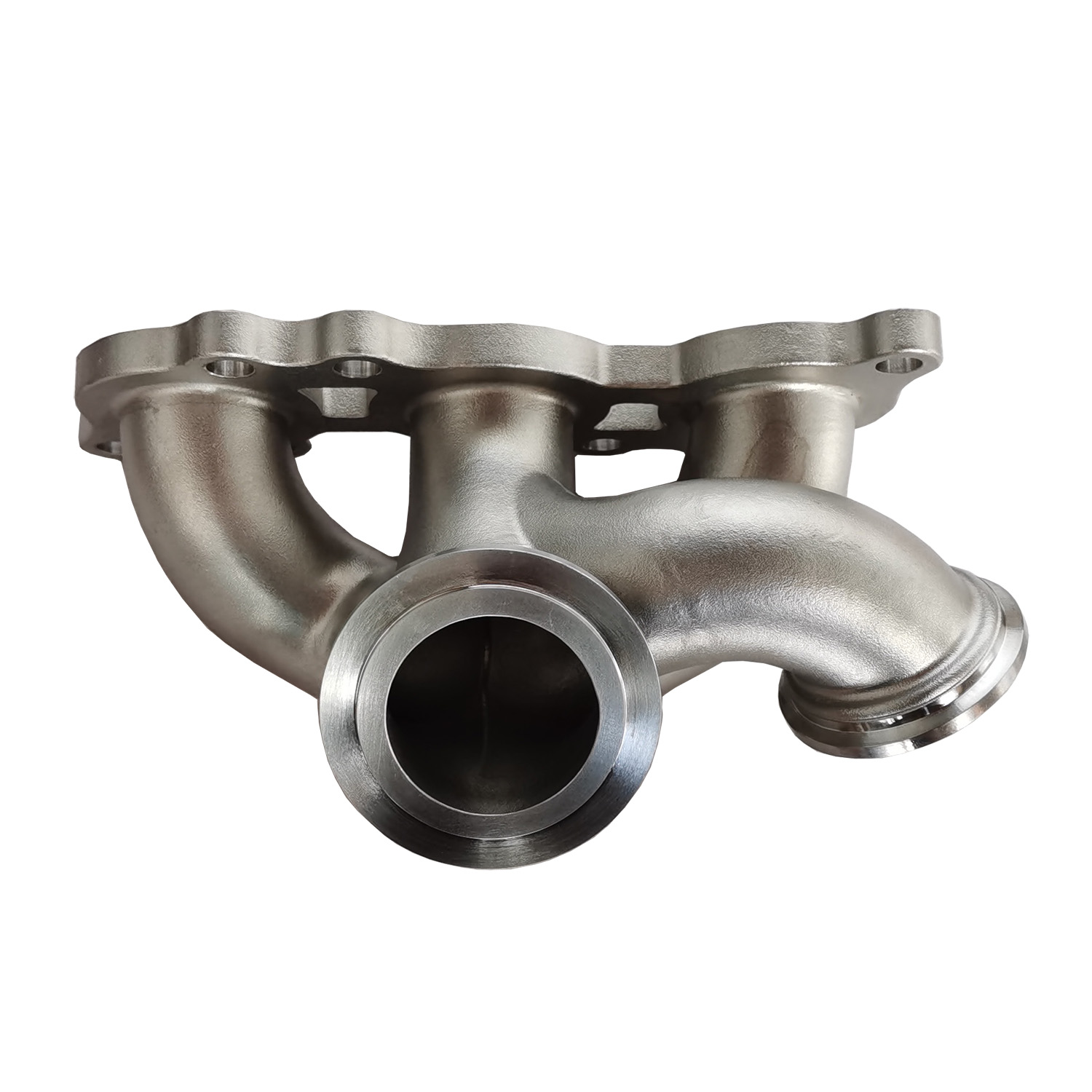
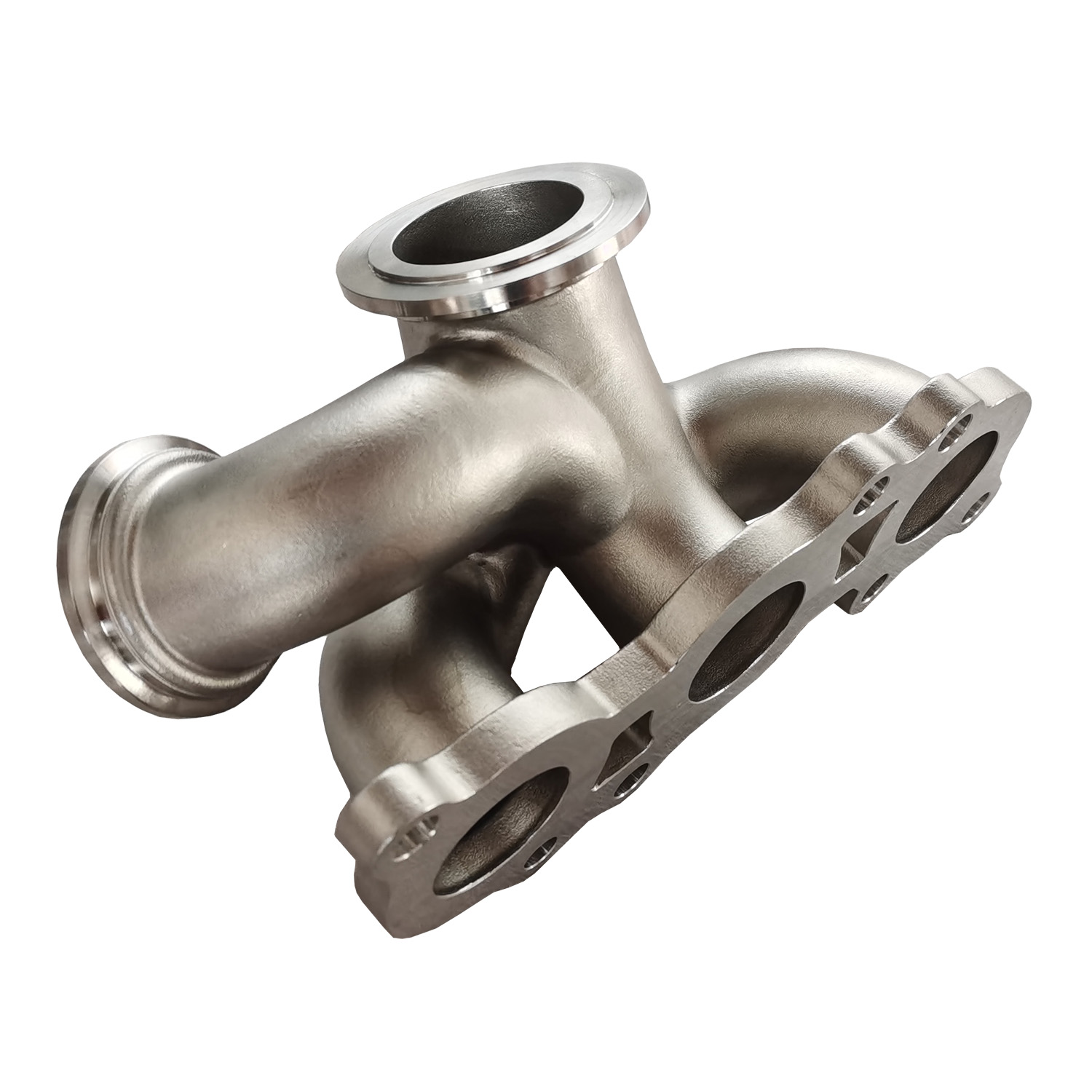

Requirements for exhaust manifolds
1. Good high-temperature oxidation resistance
The exhaust manifold works under high-temperature cyclic alternation for a long time. The oxidation resistance of the material under high temperature directly affects the service life of the exhaust manifold. Ordinary cast iron obviously cannot meet the requirements, and alloy elements need to be added to the material to improve the high-temperature oxidation resistance of the material.
2. Stable microstructure
In the range from room temperature to working temperature, the material should not undergo phase change or minimize phase change as much as possible. Because phase change will cause volume changes, internal stress or deformation, affecting the performance and life of the product. Therefore, the matrix material is preferably a stable ferrite or austenite structure. The destruction form of cast iron parts working under high temperature conditions is mainly manifested as corrosion under high temperature conditions. After the constituent phases in the organization are oxidized (such as graphite carbon), the volume of the oxide is greater than the original volume, causing irreversible expansion of the casting. Compared with the three graphite forms of flake, worm and spherical, cast iron with spherical graphite has the best high temperature resistance. The reason is that during the solidification process of cast iron, flake graphite grows as the leading phase. At the end of eutectic solidification, the graphite in each eutectic group forms a continuous branched three-dimensional form. At high temperature, when oxygen invades the metal, the graphite is oxidized to form a microscopic channel, which accelerates the oxidation process. When spherical graphite nucleates, it grows to a certain size alone and is surrounded by the matrix. It exists as an isolated ball. After the graphite ball is oxidized, no channel is formed, thus weakening the further oxidation. Therefore, the high temperature oxidation resistance of ductile iron is better than that of other forms of graphite, and the oxidized holes have less effect on the high temperature strength of cast iron than other forms of graphite. Vermicular graphite is between the two.
3. Small thermal expansion coefficient
A small thermal expansion coefficient is conducive to reducing the thermal stress and thermal deformation of the exhaust manifold, and is conducive to improving the performance and service life of the product.
4. Excellent high temperature strength
It must meet the necessary strength requirements of the product when used at high temperatures.
5. Good process performance and low cost
There are many types of heat-resistant and high-temperature resistant metal materials, but due to the complex shape of the exhaust manifold, the material used to manufacture the exhaust manifold must have good process performance, and its cost must meet the needs of mass production in the automotive industry.