SG Iron Shell Mold Casting Company – Ductile Cast Iron Resin Coated Sand Castings – RMC Foundry Detail:
Ductile cast iron resin coated sand castings for freight car with CNC machining services.
Resin coated sand shell mould casting is a process in which the sand mixed with a thermosetting resin is allowed to come into contact with a heated metallic pattern plate, so that a thin and strong shell of mould is formed around the pattem. Then the shell is removed from the pattern and the cope and drag are removed together and kept in a flask with the necessary back-up material and the molten metal is poured into the mould.
Cast irons are the ferrous alloys which have carbon contents of more than 2%. Though cast irons can have a carbon percentage between 2 to 6.67, the practical limit is normally between 2 and 4%. These are important mainly because of their excellent casting qualities. The gray cast irons and ductile cast irons (also called nodular cast iron or spheroidal graphite iron).
When graphite is present as small, round, and well-distributed particles, its weakening effect is small and such cast irons would have higher ductility. This type of cast iron is called ductile or nodular iron or spheroidal graphite or simply SG iron. This form of graphite can be achieved by adding elemental magnesium or cerium or a combination of the two elements to molten cast iron. Magnesium is added in quantities of 0.07 to 0. 10% followed by the addition of ferro-silicon to promote graphitization. During solidification, magnesium helps in the distribution of graphite throughout the metal.
Ductile cast iron has better strength-to-weight ratio, better machinability and higher impact value. Moreove, the ductile iron components are produced by casting process wherein better control of component shape can be achieved compared to drop forging. Thus, many a component such as crank shafts and connecting rods manufactured usually by drop forging is increasingly being replaced by ductile iron castings.
Advantages of Resin Coated Sand Shell Mould Casting:
1. Resin Coated Sand Shell-mould castings are generally more dimensionally accurate than sand castings. It is possible to obtain a tolerance of +0.25 mm for steel castings and +0. 35 mm for grey cast iron castings under normal working conditions. In the case of close toleranced shell moulds, one may obtain it in the range of +0.03 to +0.13 mm for specific applications.
2. A smoother surface can be obtained in shell castings. This is primarily achieved by the finer size grain used. The typical range of roughness is of the order of 3 to 6 mircrons.
3. Draft angles, which are lower than the sand castings, are required in shell moulds. The reduction in draft angles may be from 50 to 75%, which considerably saves the material costs and the subsequent machining costs.
4. Sometimes, special cores may be eliminated in shell moulding. Since the sand has high strength the mould could be designed in such a manner that internal cavities can be formed directly with the need of shell cores.
5. Also, very thin sections(up to 0.25 mm) of the type of air-cooled cylinder heads can be readily made by the shell moulding because of the higher strength of the sand used for moulding.
6. Permeability of the shell is high and therefore no gas inclusions occur.
7. Very small amount of sand needs to be used.
8. Mechanisation is readily possible because of the simple processing involved in shell moulding.
Raw Materials for Resin Coated Sand Casting Process:
• Cast Iron: Gray Cast Iron, Ductile Cast Iron.
• Cast Carbon Steel and Alloy Steel: Low Carbon Steel, Medium Carbon Steel and High Carbon Steel from AISI 1020 to AISI 1060; 20CrMnTi, 20SiMn, 30SiMn, 30CrMo, 35CrMo, 35SiMn, 35CrMnSi, 40Mn, 40Cr, 42Cr, 42CrMo…etc on request.
• Cast Stainless Steel: AISI 304, AISI 304L, AISI 316, AISI 316L and other stainless steel grade.
• Cast Aluminium Alloys.
• Brass & Copper.
• Other Materials and Standards on request
▶ Resin Coated Sand Casting Capacities:
• Max Size: 1,000 mm × 800 mm × 500 mm
• Weight Range: 0.5 kg – 100 kg
• Annual Capacity: 2,000 tons
• Tolerances: On Request.
▶ Inspecting Resin Coated Sand Castings:
• Spectrographic and manual quantitative analysis
• Metallographic analysis
• Brinell, Rockwell and Vickers hardness inspection
• Mechanical property analysis
• Low and normal temperature impact testing
• Cleanliness inspection
• UT, MT and RT inspection
▶ Resin Coated Sand Casting Procedures:
✔ Making Metal Patterns. The pre-coated resin sand needs to be heated in the patterns, so metal patterns are the necessary tooling to make shell molding castings.
✔ Making Pre-coated Sand Mold. After installing the metal patterns on the molding machine, the pre-coated resin sand will be shot into the patterns, and after heating, the resin coating will be molten, then the sand molds become solid sand shell and cores.
✔ Melting the Cast Metal. Using induction furnaces, the materials would be melted into liquid, then the chemical compositions of the liquid iron should be analyzed to match the required numbers and percents.
✔ Pouring Metal. When the melted iron meet the requirements, then they will be poured into the shell molds. Based on different characters of the casting design, the shell molds will be buried into green sand or stacked up by layers.
✔ Shot Blasting, Grinding and Cleaning. After the cooling and solidification of the castings, the risers, gates or additional iron should be cut off and removed. Then the iron castings will be cleaned by sand peening equipment or shot blasting machines. After grinding the gating head and parting lines, the finished casting parts would come, waiting for the further processes if needed.
▶ Post-Casting Process
• Deburring & Cleaning
• Shot Blasting / Sand Peening
• Heat Treatment: Normalization, Quench, Tempering, Carburization, Nitriding
• Surface Treatment: Passivation, Andonizing, Electroplating, Hot Zinc Plating, Zinc Plating, Nickel Plating, Polishing, Electro-Polishing, Painting, GeoMet, Zintec.
• CNC Machining: Turning, Milling, Lathing, Drilling, Honing, Grinding.
▶ Why You Choose RMC Foundry for Shell Mold Casting Components?
✔ Precision and therefore a high material utilization. You will get a net or near-net-shape products after shell molding casting, depending on the requirements of end-users, there will be no or very little machining process is required.
✔ Better surface performance. Thanks to the new-tech materials for molding, the castings from shell molding have a much fine and higher accuracy surface.
✔ A good balanced choice comparing to the sand casting and investment. The shell molding casting have better performance and surface than sand casting, while having much lower costs than precision investment casting.
Product detail pictures:
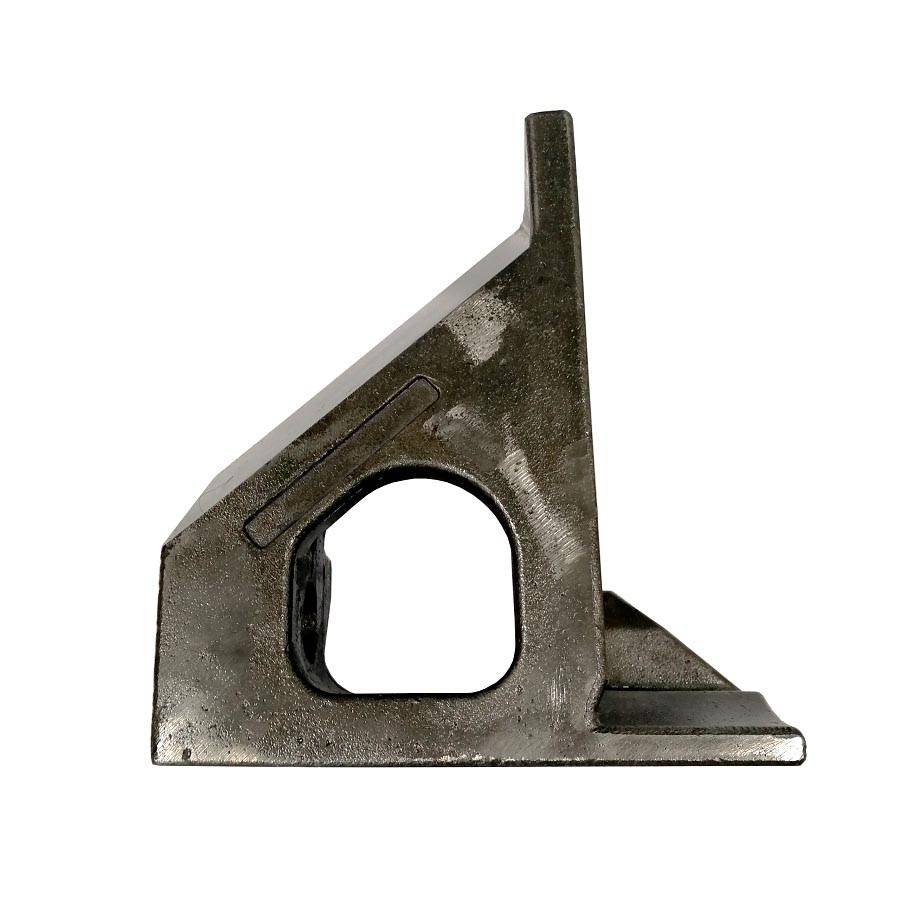
Related Product Guide:
Good quality comes 1st; assistance is foremost; business enterprise is cooperation" is our business enterprise philosophy which is regularly observed and pursued by our company for SG Iron Shell Mold Casting Company – Ductile Cast Iron Resin Coated Sand Castings – RMC Foundry, The product will supply to all over the world, such as: Madagascar , El Salvador , Belgium , To win customers' confidence, Best Source has set up a strong sales and after-sales team to provide the best product and service. Best Source abides by the idea of "Grow with customer" and philosophy of "Customer-oriented" to achieve cooperation of mutual trust and benefit. Best Source will always stand ready to cooperate with you. Let's grow together!

We always believe that the details decides the company's product quality, in this respect, the company conform our requirements and the goods are meet our expectations.

-
Factory Supply Steel Casting Products - Stainl...
-
factory Outlets for Iron Casting Factory - Sta...
-
Factory Supply Sand Casting Manufacturer - Nod...
-
Cheapest Price Duplex Stainless Steel Sand Cast...
-
Top Quality Casting Company - Brass CNC Machin...
-
Factory best selling Steel Precision Casting Ma...