Vacuum casting has many other names such as vacuum sealed casting, negative pressure sand casting, V process casting and V casting, just because of the negative pressure used for making the casting mold. It is of great importance to investigate the casting processes for high precision thin wall ferrous metal casting parts because the processes are helpful in reducing energy consumption, saving raw materials and decreasing machine weight. To achieve these objectives, many casting methods have been developed. Vacuum-sealed molding process, the V-process for short, is widely used to make iron and steel castings with relatively thin wall, high precision and smooth surface. However, the vacuum casting process cannot be used to pour metal castings with very small wall thickness, because the liquid metal filling in a mold cavity relies on only the static pressure head in the V-process. Moreover, the process cannot produce castings that require very high dimension accuracy due to the restricted compressive strength of the mold.
In order to improve the filling ability of the molten liquid metal and increase the compressive strength of mold, we have developed a new casting method named as the vacuum-sealed mold casting under pressure. Al though this casting process is based on V-process, it is different because in the process the liquid metal fills and solidifies in a vacuum-sealed mold under high pressure. By using the method, metal castings with thin walls, smooth surface and accurate dimensions have been produced successfully.
The mold used this new vacuum casting process is similar to that used for common V-process. After the mold is made, it is placed into a vessel. By removing the air through exhausting pipe, the vacuum level in the mold can be maintained at a fixed value. The liquid metal is poured into the ladle inside the vessel. Then the vessel is sealed; and the air pressure in the vessel is increased to the designated value by pumping air through the channel. After that, the liquid metal is poured into the mold cavity by turning the rocker arm. During the process of filling and solidification, the air inside the mold is continuously sucked out through the pipes and the mold is kept in a vacuum state. Hereafter, liquid metal fills and solidifies under the high pressure.
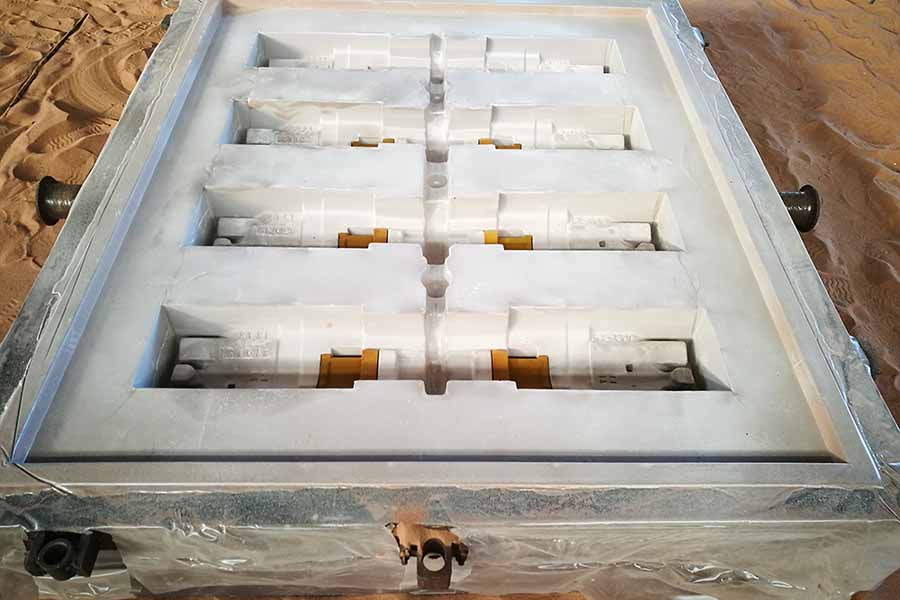
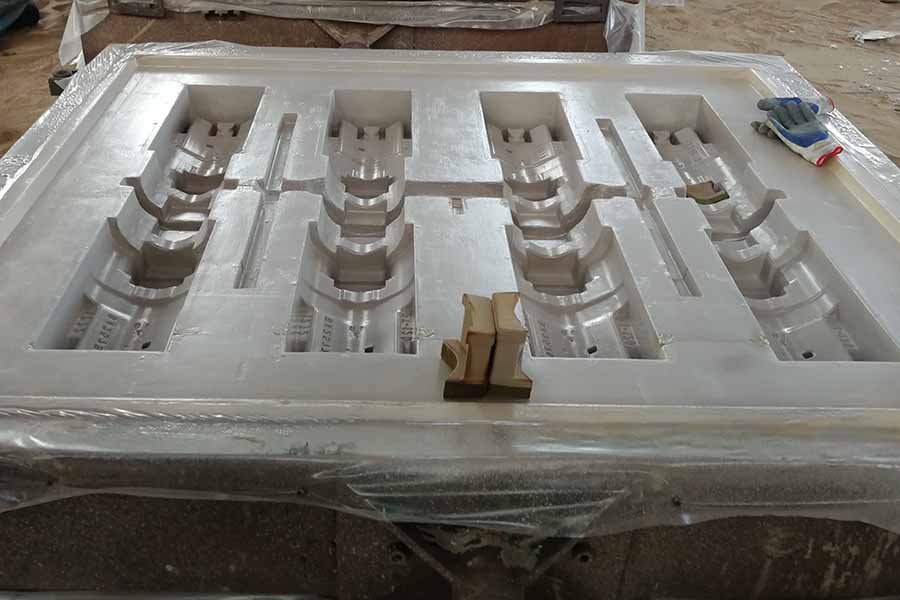
Generally speaking, the mold can be formed and kept from collapsing when the pressure difference imore than 50 kPa. The function of the vent screen connecting the mold cavity to the old is to promote the liquid metal flowing into the mold cavity by pulling gas or air from the mold cavity through dry sand in the mold. When there is such a vent screen, the pressure difference decreases during pouring; but it is still higher than 150 kPa, far greater than 50 kPa. Therefore, the vent screen doesn't destroy the function of the plastic film on the cope mold.
Therefore P-V process can be used to produce thin wall cast iron castings and cast steel castings with high precision. In practical casting production some common approaches are applied to improve the filling ability of liquid metal, including increasing the static pressure head of the liquid metal,to increase the mold's temperature and to increase the filling pressure. The decreasing the pressure in the m old cavity is also an effective way to increase the filling ability.
The mold compressive strength in this new type vacuum casting process results from the pressure difference between the inside and the outside the mold. The larger the pressure difference, the largerthe friction among sand grains, and the more difficult the movement of sand grains against one another, leading to higher mold compressive strength. High compressive strength is beneficial in producing castings with high dimension accuracy and less or no casting defects.
Although approaches such as increasing binder content, baking green mold and using resin bonded sand can all improve the mold compressive strength, they will also increase the production cost greatly. Under high temperatures the plastic film on the surface of the mold cavity softens and melts, then the film evaporates and diffuses into the mold sand under the effect of pressure difference, and in the process the mold loses its airproof capability gradually. Such process is named as the burning-losing process of the plastic film. Many factors affect the velocity of burning-losing of plastic film, such as the type and thickness of plastic film, casting size, pressure difference between the inside and the outside of the mold, the temperature of molten liquid metal and whether there is a coating layer on the plastic film. However, when a coating layer is sprayed on the film, the velocity of burning-losing reduces greatly and the mold has good air proof property.
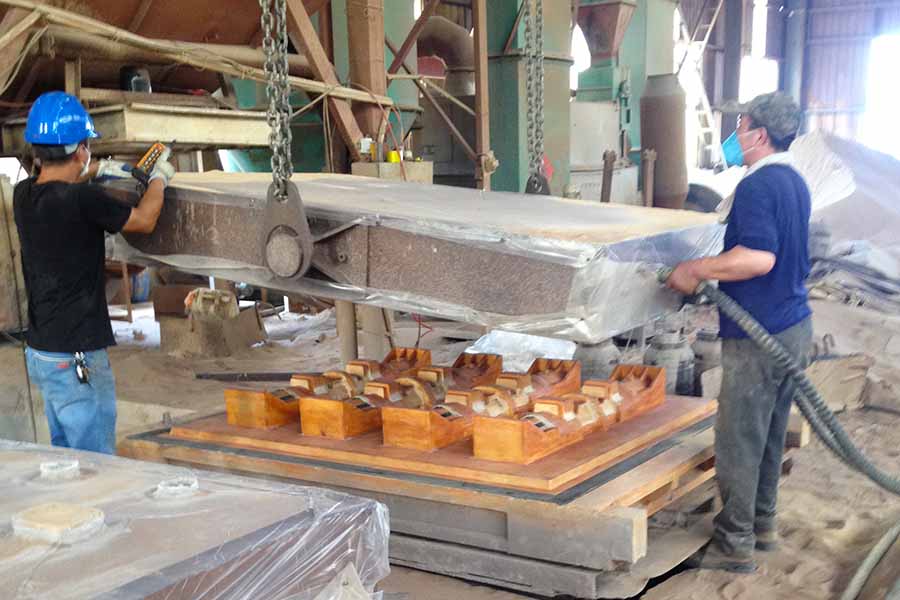
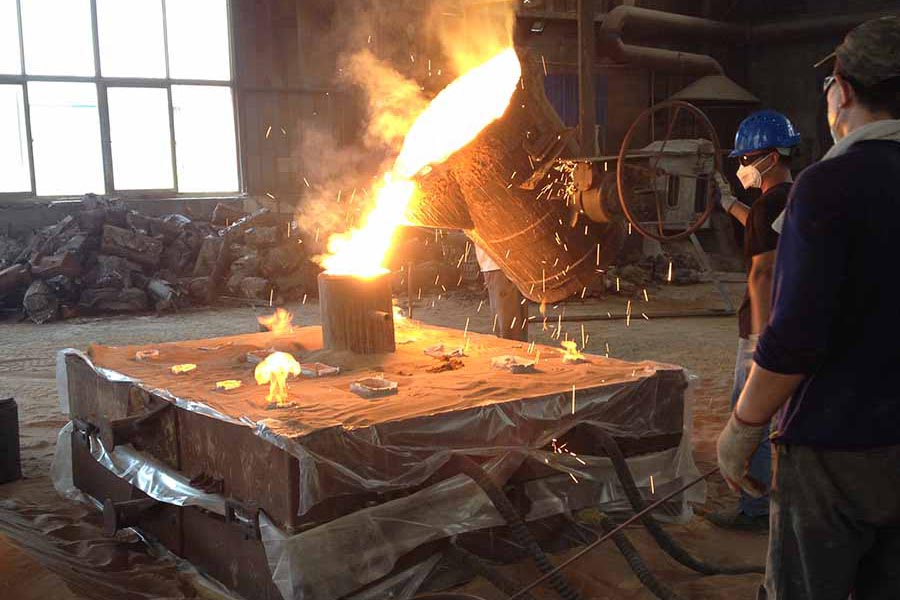
Post time: Jan-24-2021