Solidification Mechanisms
During the casting process, the solidification of castings occurs when the molten metal transitions from a liquid to a solid state. This process can be broadly categorized into three mechanisms: nucleation, dendritic growth, and grain structure formation. During nucleation, small solid particles form within the liquid metal. These nuclei grow into dendritic structures, branching out in a tree-like pattern. The final grain structure of the castings is determined by the growth of these dendrites and their interaction with the cooling environment.
Solidification of Various Alloys
Different alloys solidify in unique ways, influenced by their chemical composition and thermal properties:
Aluminum Alloys: Aluminum alloys typically exhibit a high degree of fluidity, allowing for intricate and thin-walled castings. Their solidification often involves the formation of a fine, equiaxed grain structure. However, aluminum alloys are prone to shrinkage porosity and hot tearing, which can affect casting quality.
Iron and Steel Alloys: Cast iron solidifies with a complex structure due to its high carbon content, forming graphite flakes or nodules. The solidification of steel alloys involves the formation of austenite dendrites, which transform into ferrite and pearlite upon cooling. The cooling rate and alloy composition significantly influence the grain structure and mechanical properties of the casting.
Copper Alloys: Copper alloys, such as brass and bronze, solidify with a columnar or equiaxed grain structure. These alloys are prone to segregation, where different elements in the alloy separate during solidification, leading to variations in composition and properties within the casting.
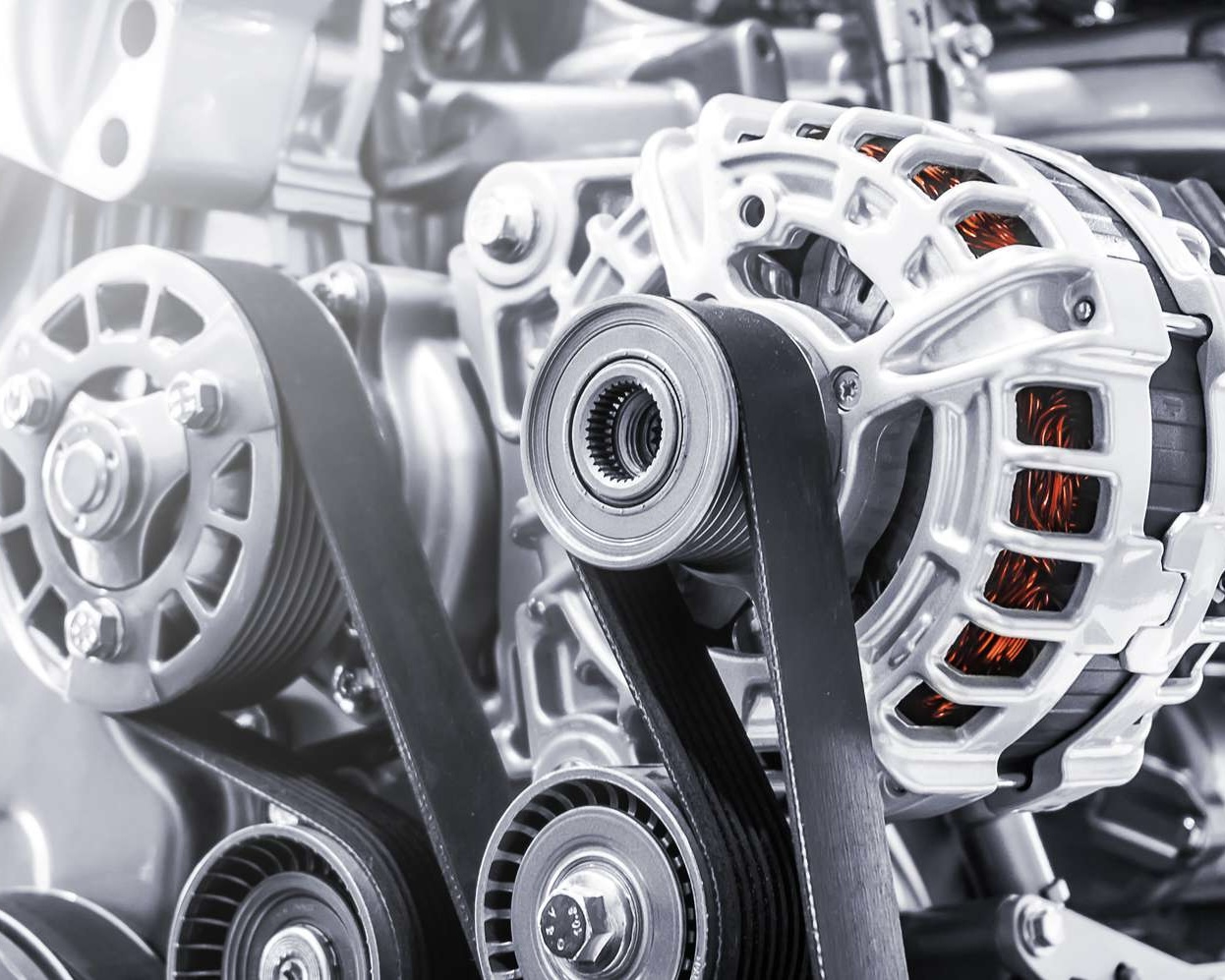
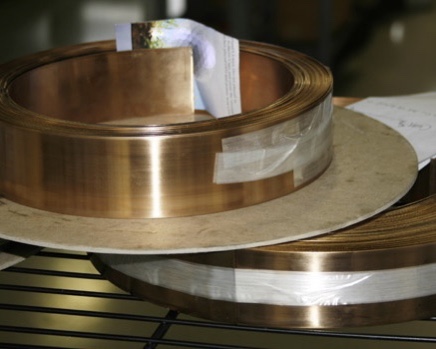
Relationship Between Solidification and Casting Quality
The solidification behavior of an alloy directly impacts the quality of the casting. A uniform and controlled solidification process is essential to minimize defects such as porosity, segregation, and hot tearing. For instance, rapid cooling can lead to the formation of fine grains, enhancing the mechanical properties of the casting. Conversely, slow cooling may result in coarse grains and increased susceptibility to defects.
Solidification Time and Speed
The solidification time and speed are influenced by factors such as the casting's size, shape, and the thermal properties of the mold material. The solidification time is the duration required for the entire casting to transition from liquid to solid, while the solidification speed refers to the rate at which this transition occurs.
Faster solidification speeds are generally achieved through techniques such as using chill molds, which rapidly extract heat from the molten metal. This results in a finer grain structure and improved mechanical properties. However, excessively fast cooling can lead to thermal stresses and cracking. Therefore, achieving an optimal balance between solidification speed and casting quality is crucial.
Post time: Oct-11-2024