Shrinkage in castings is a crucial aspect that significantly impacts the quality and integrity of the final product. Understanding the different types of shrinkage associated with various materials, such as cast steel and cast iron, as well as the factors contributing to defects like shrinkage cavities and hot cracks, is essential for effective casting practices.
Shrinkage in Cast Steel and Cast Iron
When discussing shrinkage, it is vital to differentiate between the two primary materials used in casting: cast steel and cast iron. Both materials exhibit shrinkage, but the mechanisms and rates can differ.
Cast steel typically experiences a total shrinkage of approximately 1.5% to 2% from its molten state to its solidified form. This shrinkage is primarily due to the thermal contraction of the material as it cools. In contrast, cast iron has a higher shrinkage rate, generally around 2% to 3%. The additional shrinkage in cast iron can be attributed to its composition, which includes a higher carbon content that affects its solidification behavior.
Actual Shrinkage of Castings
Actual shrinkage refers to the total dimensional change experienced by a casting from its liquid state to its final solid state. This can include both the volumetric shrinkage during cooling and the effects of solidification. Proper design and calculation of the casting geometry are essential to accommodate this shrinkage, as failure to do so can lead to dimensional inaccuracies and compromised mechanical properties.
Shrinkage Cavities and Porosity
Shrinkage cavities, also known as shrinkage voids, occur when the liquid metal fails to fill the mold due to insufficient feeding during solidification. This phenomenon can lead to weak points in the casting, making it susceptible to failure under load. On the other hand, porosity—often seen in castings—is primarily caused by gas entrapment or improper pouring techniques, which can further diminish the structural integrity.
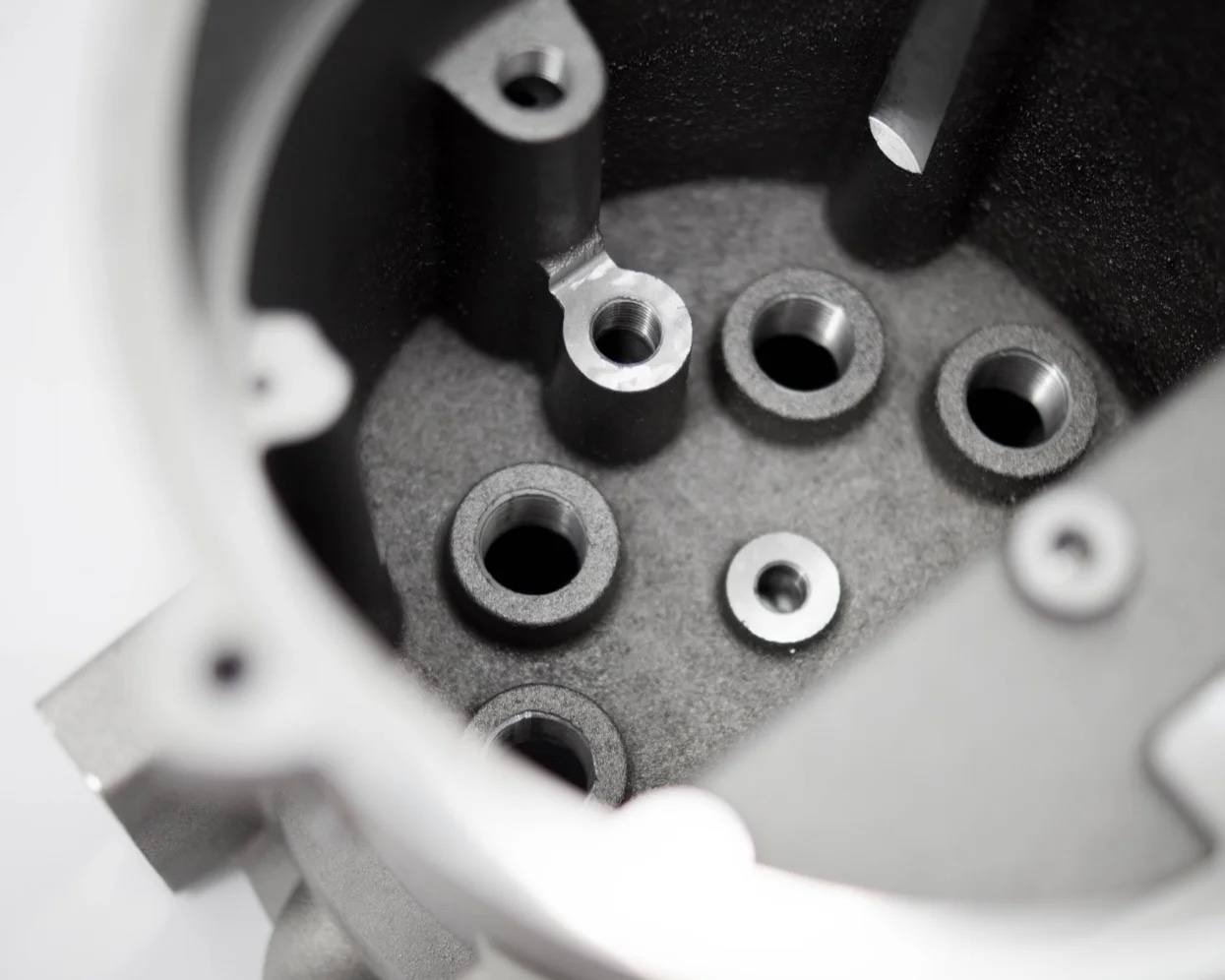
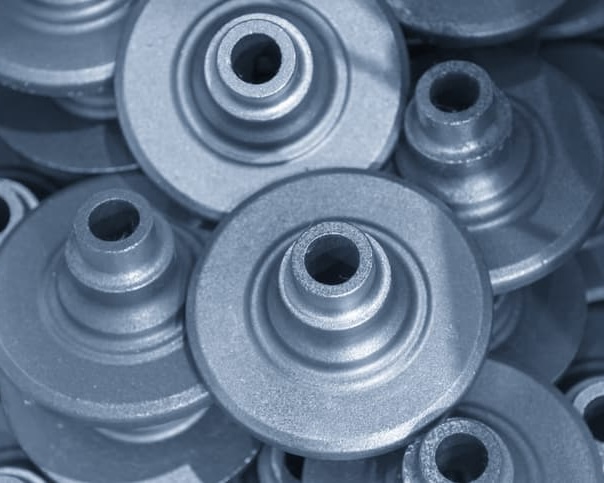
Hot Cracking and Casting Stresses
Hot cracks are another significant concern in casting. These occur when the casting is still at elevated temperatures but has already begun to solidify. The stresses induced during cooling can exceed the material's tensile strength, resulting in fractures. Controlling the cooling rate and understanding the thermal properties of the material can help mitigate the risks of hot cracking.
Cold Cracking and Deformation
Cold cracking occurs after the casting has cooled to room temperature and is often a result of residual stresses. These stresses can arise from uneven cooling, which leads to differential contraction throughout the casting. Such stresses may also result in deformation, impacting the casting's final shape and usability.
To reduce the likelihood of cold cracking and deformation, it is crucial to implement proper cooling techniques and stress-relief processes during and after the casting process.
Post time: Oct-25-2024