Sand core design is a critical aspect of the casting process in foundries, where intricate shapes and internal cavities are formed in metal parts. Understanding the different types of sand cores, the principles of setting them, their fixation and positioning is essential for producing high-quality castings.
Types of Sand Cores
Sand cores come in various types, each serving a specific purpose in the casting process:
1.Dry Sand Cores: These are made from sand bonded with resin and baked to improve strength. They are used for intricate shapes and internal cavities where high dimensional accuracy is required.
2.Green Sand Cores: These are formed from moist sand and are typically used in simple applications where high strength is not necessary.
3.Oil Sand Cores: These are bonded with oil and offer better collapsibility than dry sand cores, making them ideal for applications where easy removal of the core is necessary.
4.Cold Box Cores: These are made using a binder that hardens at room temperature, offering a balance between strength and ease of removal.
5.Shell Cores: These are created using a resin-coated sand that is heated to form a shell. They provide excellent surface finish and dimensional accuracy.
Basic Principles of Sand Core Setting
Setting sand cores correctly is crucial for the quality of the final casting. The basic principles include:
1.Alignment: Cores must be aligned accurately with the mold to ensure the final dimensions of the casting are correct. Misalignment can lead to defects such as misruns and shifts.
2.Stability: Cores must be stable within the mold to avoid movement during the pouring process, which could result in casting defects.
3.Venting: Proper venting must be provided to allow gases to escape during the pouring process, preventing gas porosity in the final casting.
4.Support: Adequate support structures must be in place to hold the cores in position, especially in complex molds where multiple cores are used.
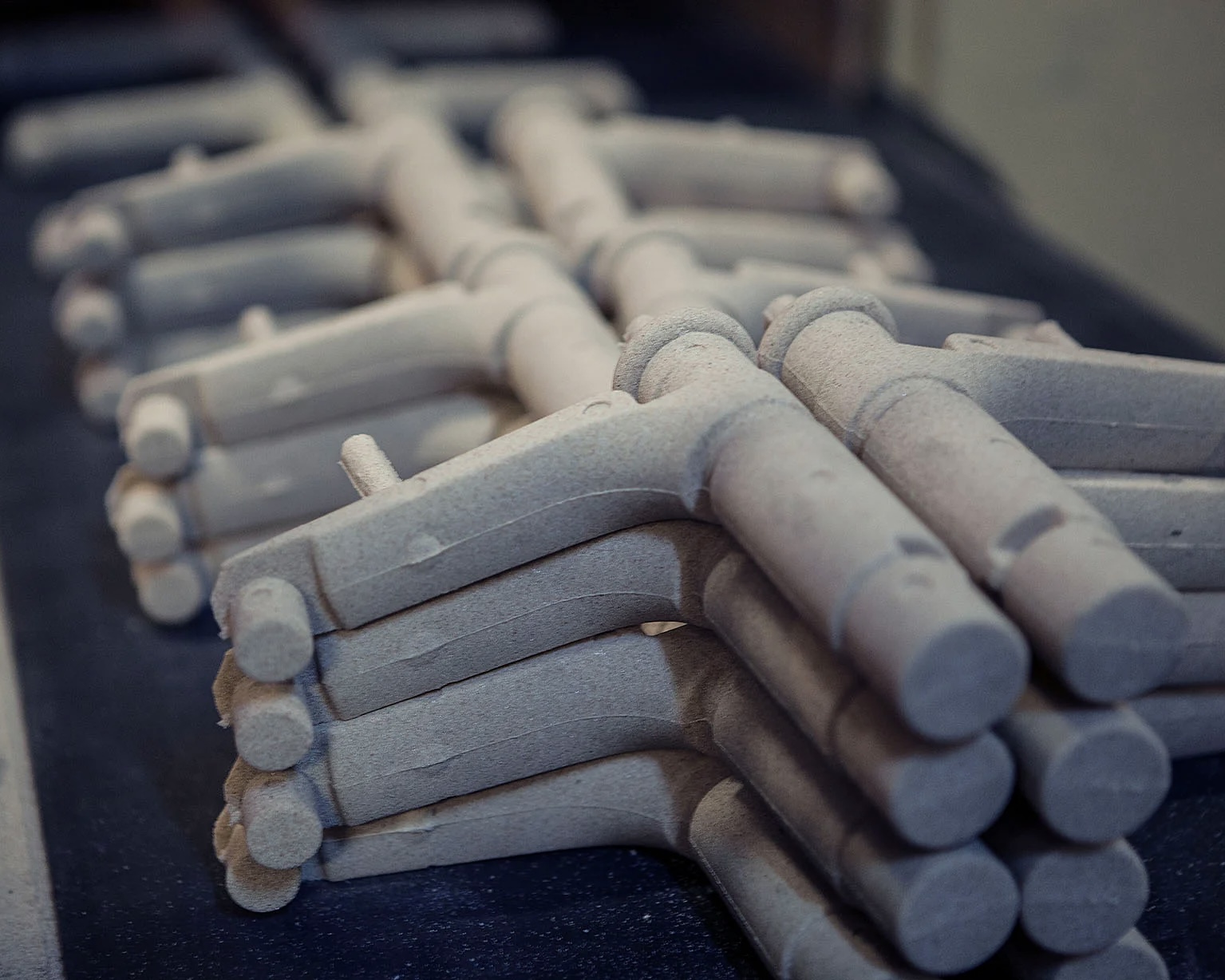
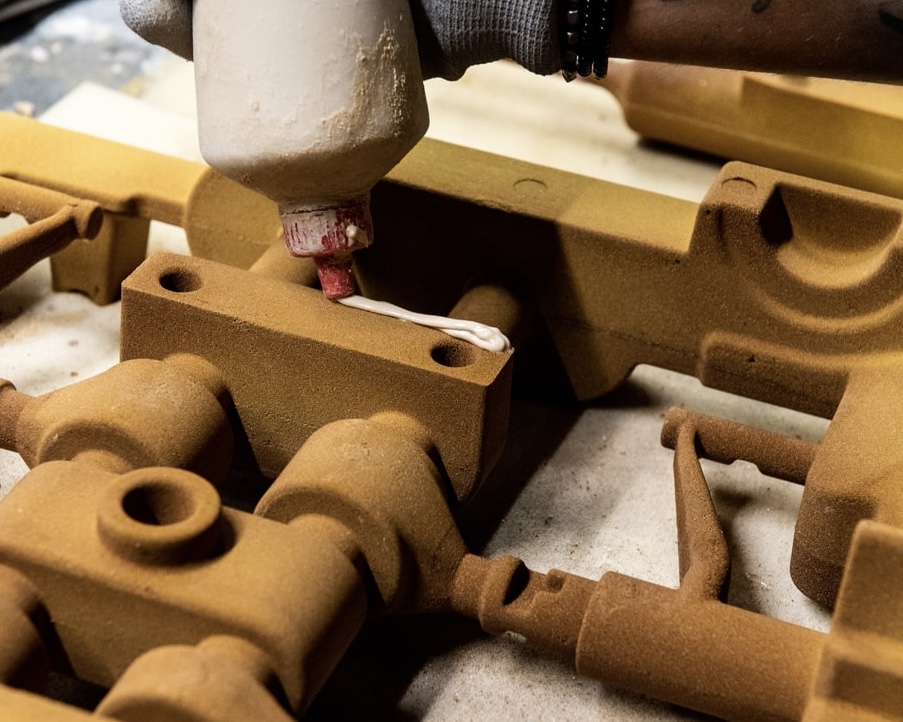
Fixation and Positioning of Sand Cores
The fixation and positioning of sand cores are achieved through various methods to ensure they remain in place during the casting process:
1.Core Prints: These are extensions of the mold cavity that hold the core in position. They provide a mechanical means of fixing the core and ensuring alignment.
2.Chaplets: These are small metal supports that hold the core in place. They are designed to fuse with the molten metal, becoming part of the final casting.
3.Core Boxes: These are used to form the sand cores and ensure they fit perfectly within the mold. The design of the core box must account for the shrinkage and expansion of the sand.
Negative Cores
Negative cores, or core negatives, are used to create undercuts or internal features that cannot be formed with conventional cores. They are typically made from wax or other materials that can be removed after the casting process. The design of negative cores requires careful consideration to ensure they can be easily removed without damaging the casting.
Venting, Assembly, and Pre-Assembly of Sand Cores
1.Venting: Proper venting is essential to allow gases generated during the pouring process to escape. Vents can be formed within the core or added as separate components. Insufficient venting can lead to gas porosity and other casting defects.
2.Assembly: In complex molds, multiple cores may need to be assembled to form the final shape. This requires precise alignment and fixation to ensure the cores fit together correctly. Assembly jigs and fixtures are often used to aid in this process.
3.Pre-Assembly: Pre-assembling cores outside the mold can improve accuracy and reduce setup time. This involves assembling the cores into a single unit before placing them into the mold cavity. Pre-assembly is particularly useful for large or complex cores that are difficult to handle individually.
Post time: Oct-31-2024