Riser design is a crucial aspect of the casting process, ensuring that castings are free from defects such as shrinkage cavities and porosity. Risers, also known as feeders, act as reservoirs of molten metal that feed the casting as it solidifies and contracts.
Riser Design for Steel Castings
In steel investment casting, the primary objective of riser design is to ensure adequate feeding of molten steel to compensate for volumetric shrinkage during solidification. Steel tends to have high shrinkage rates, making effective riser design critical.
For steel castings, two main types of risers are used: open risers and blind risers. Open risers are exposed to the atmosphere, whereas blind risers are enclosed within the mold. Blind risers are more efficient in minimizing heat loss.
Risers should be located at the heaviest sections of the casting where shrinkage is most likely to occur. The size and shape of the riser should be designed to ensure a sufficient volume of molten metal. Cylindrical risers are commonly used for their ease of removal and effectiveness in feeding. Insulating sleeves and exothermic materials are often used to maintain the temperature of the riser, ensuring it remains molten longer than the casting.
Riser Design for Iron Castings
For iron investment castings, particularly gray and ductile iron, the goal is to manage the expansion characteristics during solidification. Unlike steel, some types of iron expand during the final stages of solidification, reducing the need for large risers.
Blind risers are preferred for iron castings due to their efficiency. For ductile iron, smaller risers can often suffice because of the graphite expansion during solidification.
Smaller, more compact risers can be used for iron castings. The shape can vary but should minimize the surface area exposed to heat loss while maximizing feeding efficiency. Chills (materials that absorb heat) are sometimes used in conjunction with risers to control the cooling rate and promote directional solidification towards the riser.
.jpg)
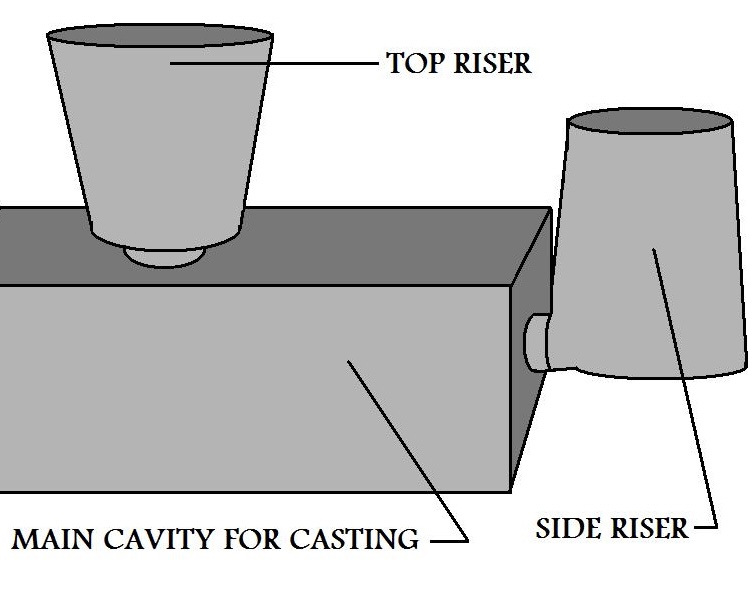
Riser Design for Non-Ferrous Alloy Castings
Non-ferrous alloys, such as aluminum and copper alloys, have different solidification behaviors compared to ferrous metals. The primary aim is to prevent defects like shrinkage porosity and to ensure complete filling of the mold.
For non-ferrous castings, both open and blind risers are used, depending on the alloy and casting design. Open risers are more common for smaller castings, while blind risers are used for larger castings.
Non-ferrous alloys typically require risers to be placed at the highest points of the casting to utilize gravity.
The riser size needs to account for the lower density and higher shrinkage rates of non-ferrous alloys. Tapered or necked risers can help in minimizing heat loss and improving feeding efficiency. Insulation is crucial for non-ferrous alloys, as they generally solidify at lower temperatures. Exothermic materials and insulating sleeves can help maintain the molten state of the riser for a longer period.
Post time: Dec-20-2024