Casting cleaning is an essential process in the manufacturing of metal components, particularly in industries such as automotive, aerospace, and heavy machinery. After the metal has been cast, the resulting product, known as a casting, often requires further processing to remove excess material, surface imperfections, and other unwanted residues. This process ensures that the final product meets the required specifications and quality standards.
Methods of Casting Cleaning
1. Mechanical Cleaning:
Shot Blasting: This is the most common method, where abrasive particles (shots) are propelled at high speed to remove surface scale, sand, and other residues from the casting. It's highly effective for cleaning ferrous and non-ferrous metals. Shot blasting is often used in investment casting to clean complex shapes of castings, especially those with complex internal structures that are difficult to clean by other methods.
Grinding: Grinding involves using a grinding wheel or abrasive belt to remove excess material, such as flash or fins, and to smooth out surface irregularities. This method is typically used for more detailed finishing work.
Vibratory Finishing: In this process, castings are placed in a vibratory machine filled with abrasive media. The vibration causes the media to rub against the castings, polishing them and removing any loose particles or burrs. This method is well-suited for small to medium-sized part.
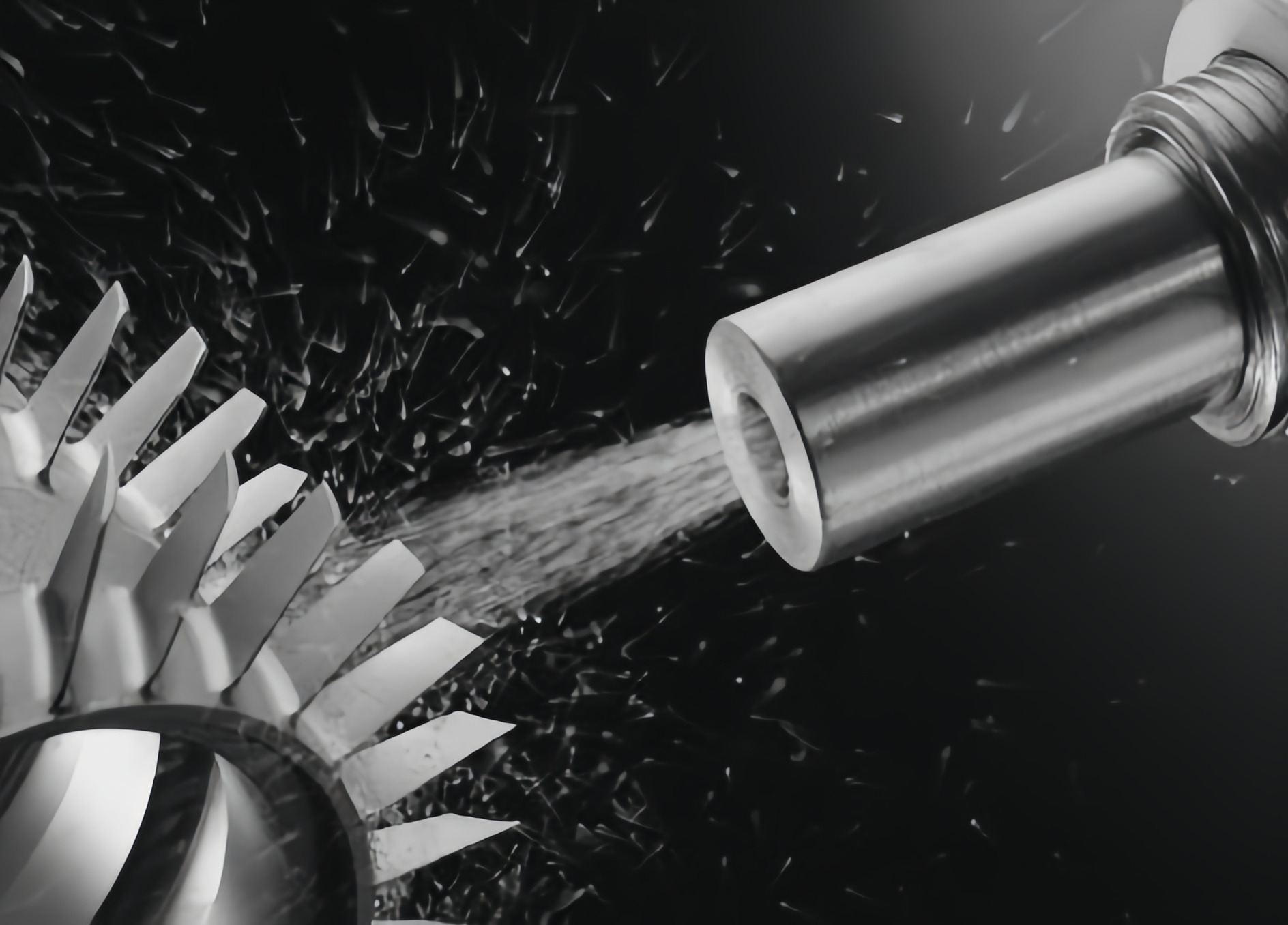
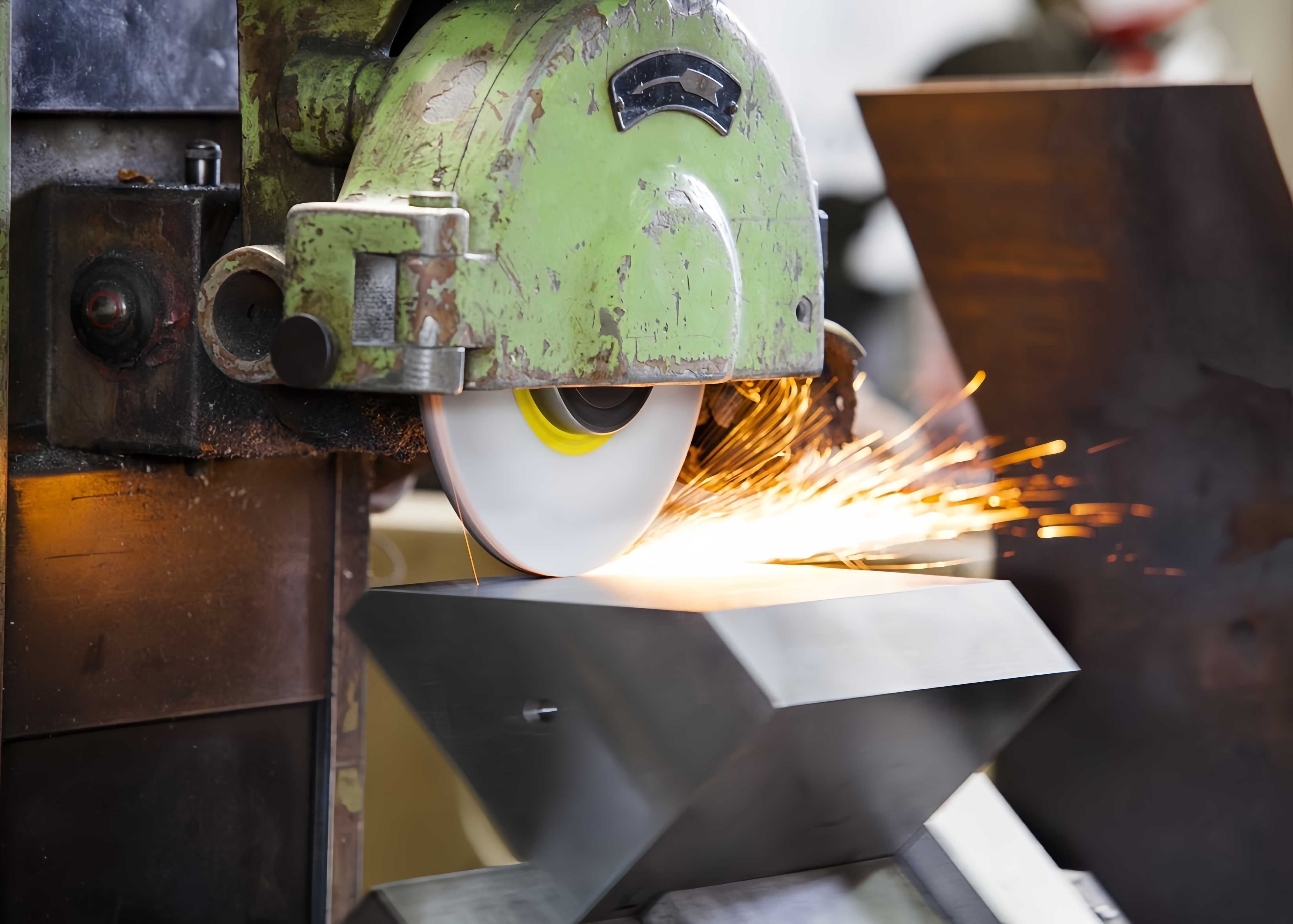
2. Chemical Cleaning:
Pickling: Pickling involves immersing the casting in an acid solution to remove surface oxides and impurities. This method is particularly useful for stainless steel and other non-ferrous metals. However, it requires careful handling due to the corrosive nature of the chemicals involved.
Electropolishing: This is an electrochemical process that smooths and cleans the surface of the casting by removing a thin layer of metal. It is often used for components requiring a high degree of cleanliness and a mirror-like finish, such as those used in medical or food-grade applications.
3. Thermal Cleaning:
Burning Off: In this method, castings are exposed to high temperatures in a furnace to burn off any residual sand, cores, or binders. This is particularly effective for castings with intricate internal passages, where mechanical cleaning might be difficult.
Applications and Suitability
Automotive Industry: Shot blasting and grinding are frequently used to clean engine blocks, cylinder heads, and other large components.
Aerospace Industry: Chemical cleaning methods like electropolishing are preferred for components that require a high degree of precision and surface finish, such as turbine blades and other critical parts.
Heavy Machinery: Vibratory finishing and shot blasting are commonly employed to clean and deburr large castings used in heavy equipment and machinery.
Conclusion
Choosing the appropriate casting cleaning method depends on the material of the casting, the complexity of the part, and the desired surface finish. Proper cleaning is crucial for ensuring that the casting meets both functional and aesthetic requirements, making it a critical step in the overall manufacturing process.
Post time: Sep-06-2024