In the casting process, chills are critical components used to control the solidification of molten metal. By promoting directional solidification, chills help minimize defects such as shrinkage cavities and improve the mechanical properties of the final casting. Chills can be classified into external and internal chills, each designed for specific applications within the mold.
Function of Chills
Promote Directional Solidification: Chills extract heat rapidly from specific areas of a casting, encouraging those areas to solidify first. This controlled solidification process directs the flow of liquid metal towards regions that are more likely to develop shrinkage cavities, thus preventing these defects.
Enhance Mechanical Properties: By controlling the solidification rate and pattern, chills help in forming a finer grain structure, which enhances the mechanical properties of the casting. The improved structure results in better strength and durability.
Common Materials for Chills
Cast Iron: Widely used due to its cost-effectiveness and adequate thermal conductivity. Cast iron chills are durable and can be easily shaped to fit various mold configurations.
Copper: Known for its excellent thermal conductivity, copper chills are used in applications requiring rapid heat extraction. Despite being more expensive than cast iron, copper's efficiency in cooling makes it valuable for specific casting needs.
Graphite: With high thermal conductivity and resistance to high temperatures, graphite chills are suitable for a variety of casting applications. They are particularly useful when a non-metallic chill is preferred.
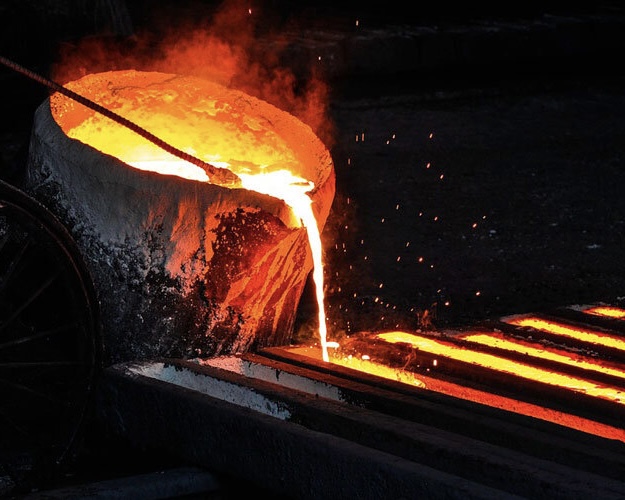
.jpg)
External Chills
External chills are placed on the surface of the mold cavity. They must be strategically designed to ensure effective heat extraction without causing excessive thermal gradients that might lead to cracking. Key considerations for external chill design include:
Size and Shape: The chill should have enough surface area to extract the necessary heat but not so large that it disrupts the solidification pattern.
Placement: Chills are positioned in areas where rapid cooling is desired to promote uniform solidification. This placement ensures that the solidification front progresses in a controlled manner, reducing the risk of defects.
Internal Chills
Internal chills are embedded within the mold cavity. They are particularly useful in complex castings with intricate internal features where external chills cannot effectively control the solidification process. Important aspects of internal chill design include:
Material Compatibility: Internal chills are often made from the same material as the casting to ensure they integrate seamlessly without causing contamination or other issues.
Strategic Placement: Internal chills must be carefully placed in regions prone to hot spots or delayed solidification. Proper placement ensures uniform cooling and solidification, enhancing the structural integrity of the casting.
Post time: Dec-06-2024