Manufacturer of Carbon Steel Green Sand Casting - Aluminium Alloy Casting Engine Spare Parts – RMC Foundry Detail:
Steps of Sand Casting Production Process
1. Making Patterns
Resin or aluminum patterns will be necessary for green sand casting process. Without patterns, the production for castings will be impossible. Sometimes, wooden patterns could be used for small quantity production, but for mass production, resin or aluminum patterns will be more suitable.
2. Molding Process
The green sand molding could be made by three methods typically, including manual molding, molding machine and automatic molding equipment. The manual molding is a traditional molding method, but it still exists because of its capability for large castings at lower costs. The molding machine method could save manpower and produce better quality castings, but it can not produce large castings because of its size limitation of sand boxes.
3. Iron Melting and Pouring
Melting could be done by medium frequency electrical induction furnaces, which could keep the quality good and stable comparing to the traditional furnaces.
4. Sand Blasting and Grinding
After the green sand iron castings are taken out from sand molds, they would be transferred into next steps for shot blasting or shot-peening to remove the sands and oxide outside of the casting parts. Then the operators will cut off, clean and grind the gating heads, risers, parting lines and sharp edges.
Further processing such as heat treatment, precision machining and surface treatment would be proceeded if the drawings or end-users require.
Aluminium and its alloys could be cast and poured by high pressure die casting, low pressure die casting, gravity casting, sand casting, investment casting and lost foam casting. Usually, the aluminum alloy castings have less weight but complex structural and better surface.
Cast Aluminium Grade in Different Standards | |||||||||
AISI | W-stoff | DIN | BS | SS | AFNOR | JIS | UNI | EN | ISO |
A356 | 3.2371 | G-AlSi7Mg | LM25 | 4244 | A-S7G | AC4C | - | 42000 | AlSi7Mg |
- | 3.2373 | G-AlSi9Mg | - | - | - | - | - | - | - |
A360 | 3.2381 | G-AlSi10Mg | LM9 | 4253 | A-S10G | - | - | 43100 | AlSi10Mg |
A413.2 | 3.2581 | G-AlSi12 | LM6 | 4261 | A-S12U | AC3A | - | 44100 | AlSi12 |
A413.0 | 3.2582 | GD-AlSi12 | - | 4247 | - | - | - | - | - |
A413.1 | 3.2583 | G-AlSi12(Cu) | LM20 | 4260 | A-S12 | - | - | 47000 | AlSi12(Cu) |
- | 3.3561 | G-AlMg5 | LM5 | 4252 | A-SU12 | AC4A | - | 51300 | ALMg6 |
- | 3.5101 | G-MgZn4SE1Zr1 | MAG5 | - | G-Z4TR | - | - | - | - |
- | 3.5103 | MgSE3Zn2Zr1 | MAG6 | - | G-TR3Z2 | - | - | - | - |
- | 3.5106 | G-MgAg3SE2Zr1 | MAG 12 | - | G-Ag22,5 | - | - | - | - |
- | 3.5812 | G-MgAl8Zn1 | MAG1 | - | G-A9 | - | - | - | - |
- | 3.5912 | G-MgAl9Zn1 | MAG7 | - | G-A9Z1 | - | - | - | - |
355.1 | - | G-AlSi5 | LM16 | - | AS4GU | - | - | 45300 | ALSi5Cu1 |
A380 | - | G-AlSi8Cu3 | LM24 | 4250 | A-S9U3 | AC4B | - | 46500 | AlSi9Cu3(Fe)(Zn) |
319 | - | G-AlSi6Cu4 | LM21 | - | A-S5UZ | AC2A | - | 45000 | AlSi6Cu4 |
319.2 | - | G-AlSi6Cu4 | LM22 | - | A-S5U | AC2A | - | 45400 | AlSi5Cu3 |
What Aluminium Alloy We Cast by Sand Casting Process:
• Cast Aluminium Alloy by China Standard: ZL101, ZL102, ZL104
• Cast Aluminium Alloy by USA Stardard: ASTM A356, ASTM A413, ASTM A360
• Cast Aluminium Alloy by other Starndards: AC3A, AC4A, AC4C, G-AlSi7Mg, G-Al12
Unified | Aluminium association | Hardness BHN | Ultimate tensile strength, MPa | Yield Strength, MPa | Modulus of elasticity, GPa | Fatigue Strength, MPa |
A03550 | AA355.0 | 75-105 | 255 | 185 | 70.3 | 69.0 |
A03600 | AA360.0 | 75.0 | 300 | 170 | 71.0 | 138.0 |
A03800 | AA380.0 | 80.0 | 317 | 159 | 71.0 | 138.0 |
A03830 | AA383.0 | 75.0 | 310 | 152 | / | 145.0 |
A03840 | AA384.0 | 85.0 | 331 | 165 | / | 140.0 |
A03900 | AA390.0 | 120.0 | 280 | 240 | 81.2 | 140.0 |
A04130 | AA413.0 | 80.0 | 296 | 145 | 71.0 | 130.0 |
A04430 | AA443.0 | 30-60 | 145 | 48.3 | 71.0 | / |
A05180 | AA518.0 | 80.0 | 310 | 193 | 69.0 | 160.0 |
Aluminum Alloy Castings Characteristics:
• The casting performance is similar to that of steel castings, but the relative mechanical properties decrease more significantly as the wall thickness increases
• The wall thickness of castings should not be too large, and other structural features are similar to those of steel castings
• Light weight but complex structural
• The casting costs per kg of aluminium castings are higher than that of iron and steel castings.
• If produced by die casting process, the mold and pattern cost would be much higher than other casting processes. Therefore, die casting aluminium castings would be more suitable for castings of large demanding quantity.
Typical Chemical Composition of Investment Casting Aluminium Alloy by North American Specifications | ||||||||||||||
Alloy Grade | Specification | Al | Cu | Si | Zn | Mg | Cr | Fe | Mn | Ti | Ag | Be | Ni | P |
A356-T6 | AMS 4218 | Bal | 0.20 | 6. 5 – 7. 5 | 0.10 | 0.25-0.45 | - | 0.20 | 0.10 | 0.20 | - | – | - | - |
A 357 | AMS 4219 | Bal | 0.20 | 6. 5 – 7. 5 | 0.10 | 0.40-.70 | - | 0.20 | 0.10 | 0.04-0.20 | - | 0.04-0.07 | - | - |
F 357 | AMS 4289 | Bal | 0.20 | 6.5-7.5 | 0.10 | 0.40-.70 | - | 0.10 | 0.10 | 0.04-0.20 | - | 0.002 | - | - |
E 357 | AMS 4288 | Bal | - | 6.5-7.5 | 0.10 | 0.55-0.60 | - | 0.10 | 0.10 | 0.10-0.20 | - | 0.002 | - | - |
A201 | AMS 4229 | Bal | 4.0-5.0 | 0.05 | - | 0.15-0.35 | - | 0.10 | 0.20-0.34 | 0.15-0.35 | 0.40-1.0 | - | - | - |
C355 | AMS 4215 | Bal | 1.0-1.5 | 4.5-5.5 | 0.10 | 0.40-0.60 | - | 0.20 | 0.10max | 0.20 | - | - | - | - |
A206 | AMS 4235 | Bal | 4.2-5.0 | .05max | 0.05max | 0.20-0.35 | - | 0.10ma | 0.20-0.50 | 0.15-0.30 | - | - | 0.5max | - |
B206 | Bal | 4.2-5.0 | .05max | 0.05max | 0.15-0.35 | - | 0.10max | 0.20-0.50 | 0 1 0 | - | - | 0.5max | - |
China Sand Casting Foundry
Product detail pictures:
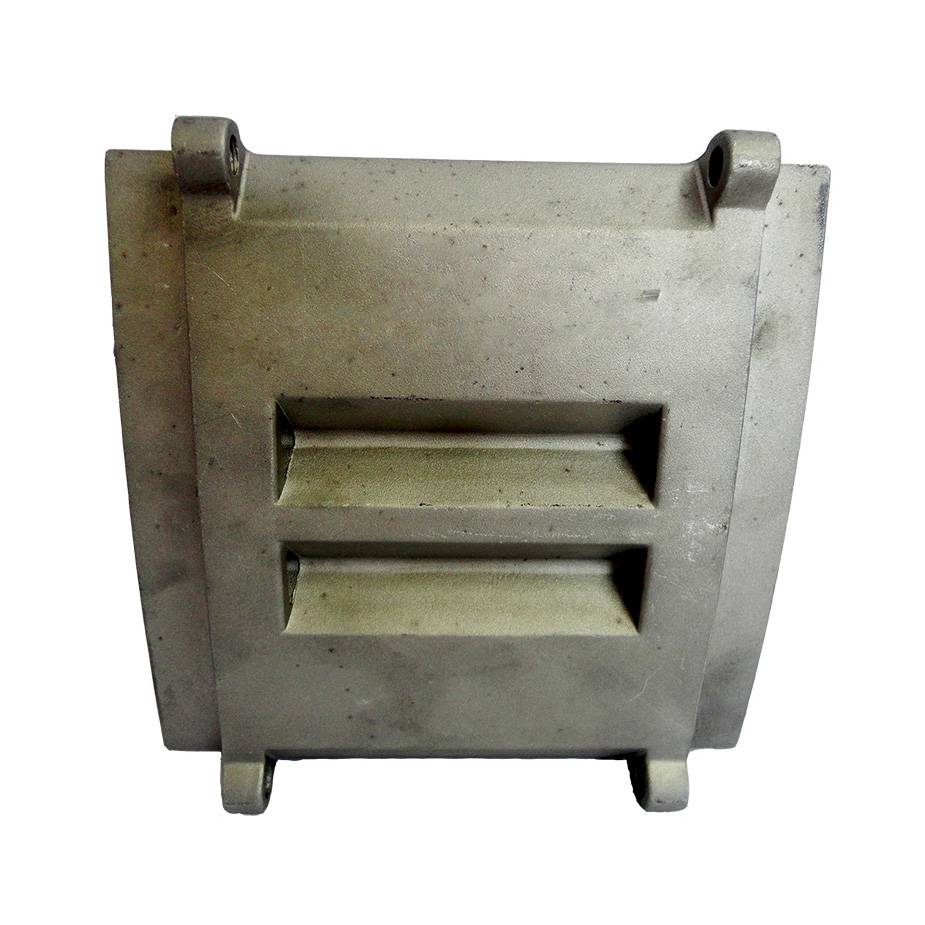
Related Product Guide:
Sticking for the perception of "Creating products of top quality and producing friends with people today from all around the world", we constantly place the desire of shoppers to start with for Manufacturer of Carbon Steel Green Sand Casting - Aluminium Alloy Casting Engine Spare Parts – RMC Foundry, The product will supply to all over the world, such as: Qatar , Madrid , Morocco , Facing fierce global market competition, we have launched the brand building strategy and updated the spirit of "human-oriented and faithful service", with an aim to gain global recognition and sustainable development.

The factory can meet continuously developing economic and market needs, so that their products are widely recognized and trusted, and that's why we chose this company.

-
Best quality Shell Casting - CNC Machining Pro...
-
Manufactur standard Alloy Steel Foundry - Stai...
-
Factory Outlets Zinc Alloy Sand Casting - Cust...
-
Hot-selling Cast Iron Casting - Lost Wax Casti...
-
Manufacturing Companies for Alloy Steel No Bake...
-
High definition Gray Iron Casting Products - C...