1. Material Overview
AISI 316 stainless steel is an austenitic stainless steel that is popular for its excellent corrosion resistance, heat resistance and mechanical properties. Its chemical composition mainly includes chromium, nickel and molybdenum, which give AISI 316 stainless steel excellent corrosion resistance and stability in high temperature environments.
2. Product Features
Excellent corrosion resistance: AISI 316 stainless steel Turbo Housing can effectively resist the erosion of various corrosive media, including sulfuric acid, hydrochloric acid, chlorine, etc., as well as fresh water and seawater environments. The passivation film formed on its surface can prevent the corrosive medium from further eroding the metal matrix.
Good heat resistance: AISI 316 stainless steel can still maintain good mechanical properties and corrosion resistance in high temperature environments. In an environment with a temperature of up to 870℃, the material can still maintain high strength and toughness, which is suitable for the manufacture of high-temperature equipment.
Excellent mechanical properties: It has high strength, good toughness and hardness, making it an ideal material for manufacturing turbine housings that withstand high pressure and high temperature. Its yield strength is usually above 205 MPa, and its tensile strength can reach above 515 MPa.
Excellent machining quality: AISI 316 stainless steel is easy to cold work, hot work and weld, and can be customized in various shapes and sizes according to customer needs.
3. Application fields
In the automotive manufacturing industry, AISI 316 stainless steel Turbo Housing is not only used for turbocharged engines of traditional fuel vehicles, but is also gradually used in the turbocharged part of the range extender or hybrid system of new energy vehicles to improve the power performance and fuel economy of the whole vehicle.
4. Customized service
We are a casting manufacturer from China, specializing in the production of a variety of castings including stainless steel AISI 316 stainless steel turbine pipes. We can provide comprehensive customized CNC machining services according to your specific needs and drawings. As your trusted single supplier, we provide a complete solution from custom model design to finished castings, to secondary machining including CNC machining, heat treatment and surface treatment, ensuring that every production link is accurate and correct to meet your diverse needs.
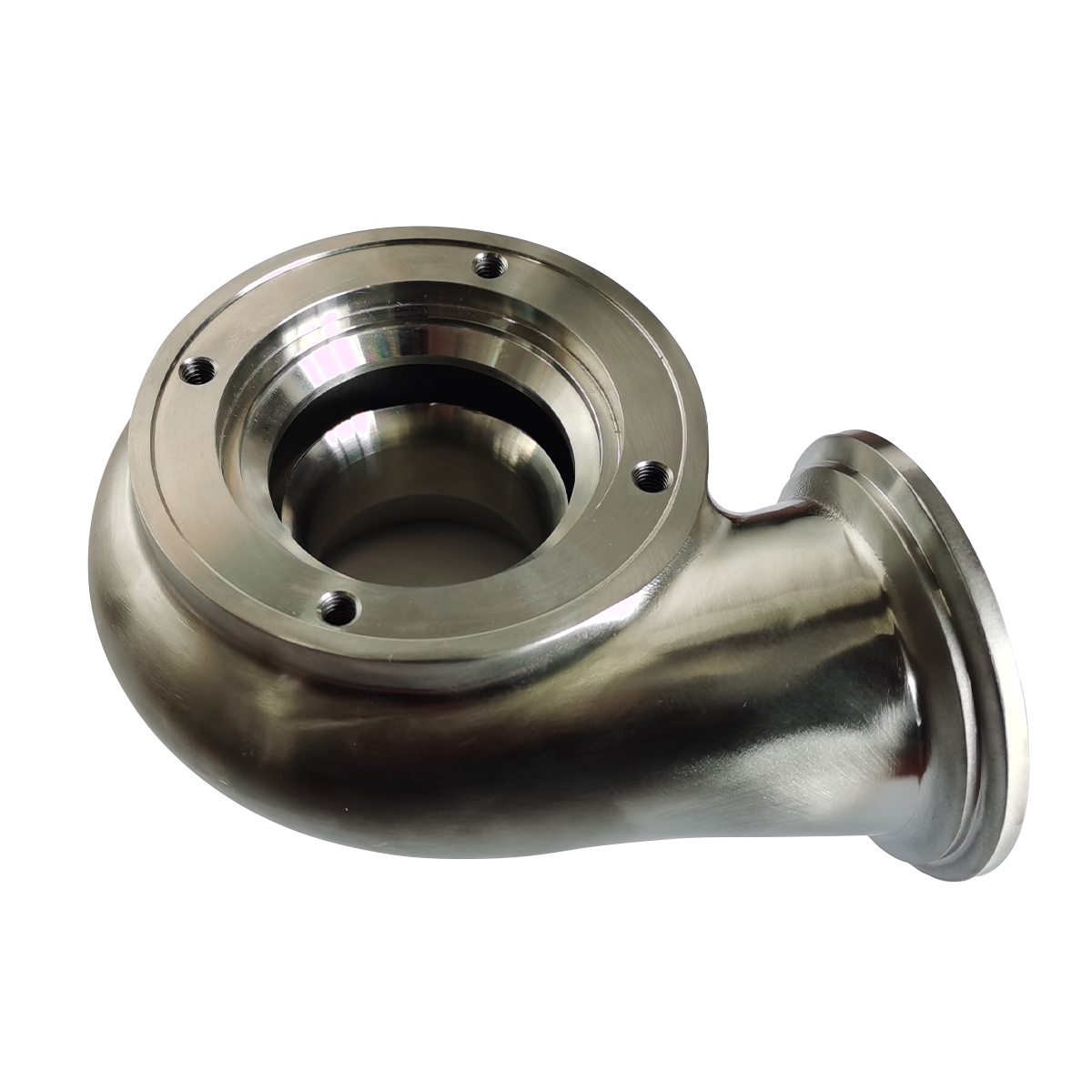
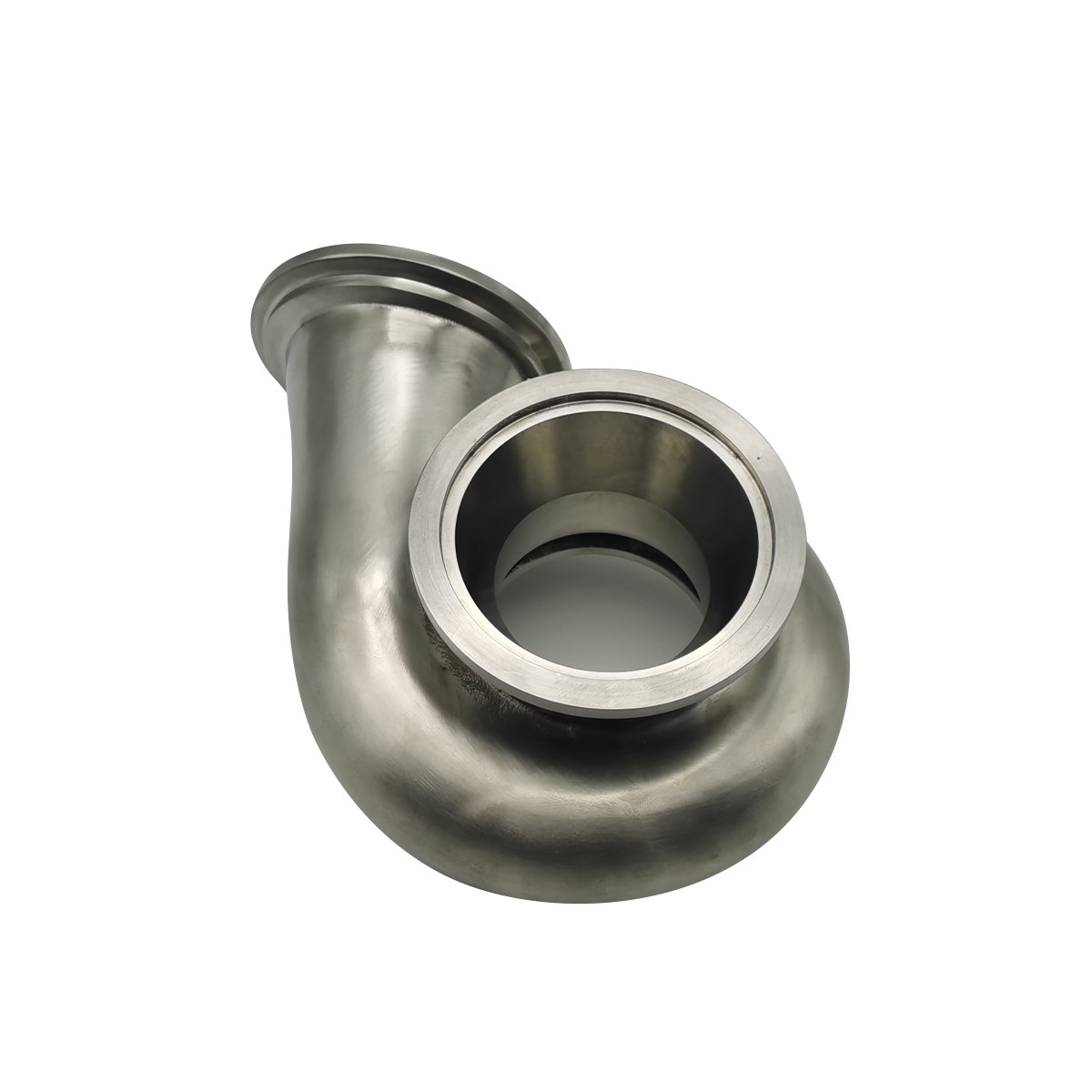
Advantages of AISI 316 stainless steel Turbo Housing using investment casting process:
1. High precision and complex shape realization
High precision: The investment casting process can ensure that the size and shape accuracy of the turbine housing reaches a very high level. Since the investment mold is made accurately according to the design drawings using fusible materials (such as wax materials), it can very accurately reflect the design intent and reduce the workload of subsequent processing and finishing.
Complex shape realization: For turbine housings with complex internal structures and shapes, the investment casting process shows its unique advantages. It can easily cope with various complex shape designs and meet diverse product needs.
2. High surface quality
Smoothness and flatness: During the investment casting process, the surface finish and flatness of the turbine housing can be significantly improved by coating multiple layers of special refractory coatings and binders on the surface of the investment mold, and performing subsequent treatments (such as sandblasting, passivation, etc.) after the metal liquid cools and solidifies. This high-quality surface helps reduce fluid resistance and improve turbine efficiency.
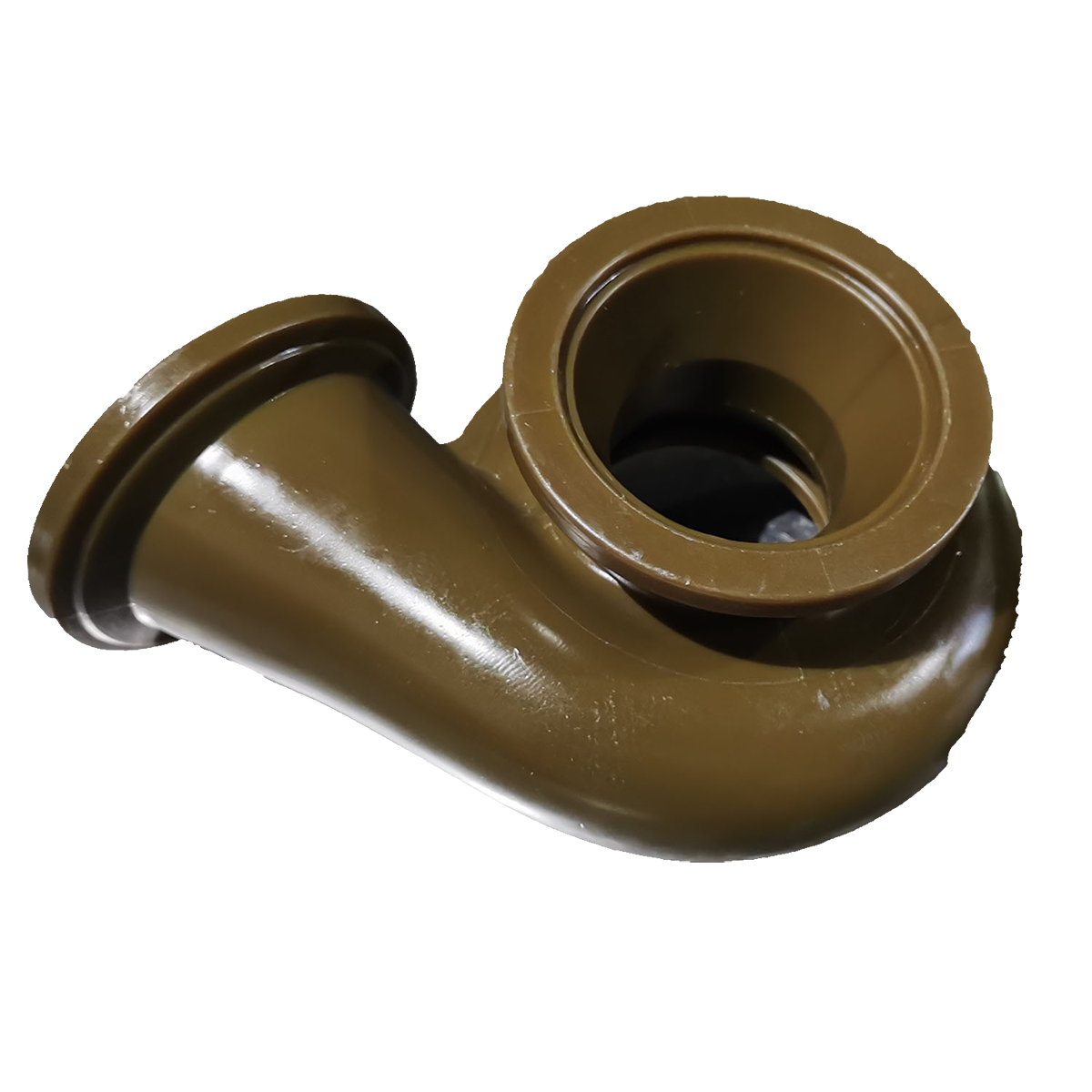
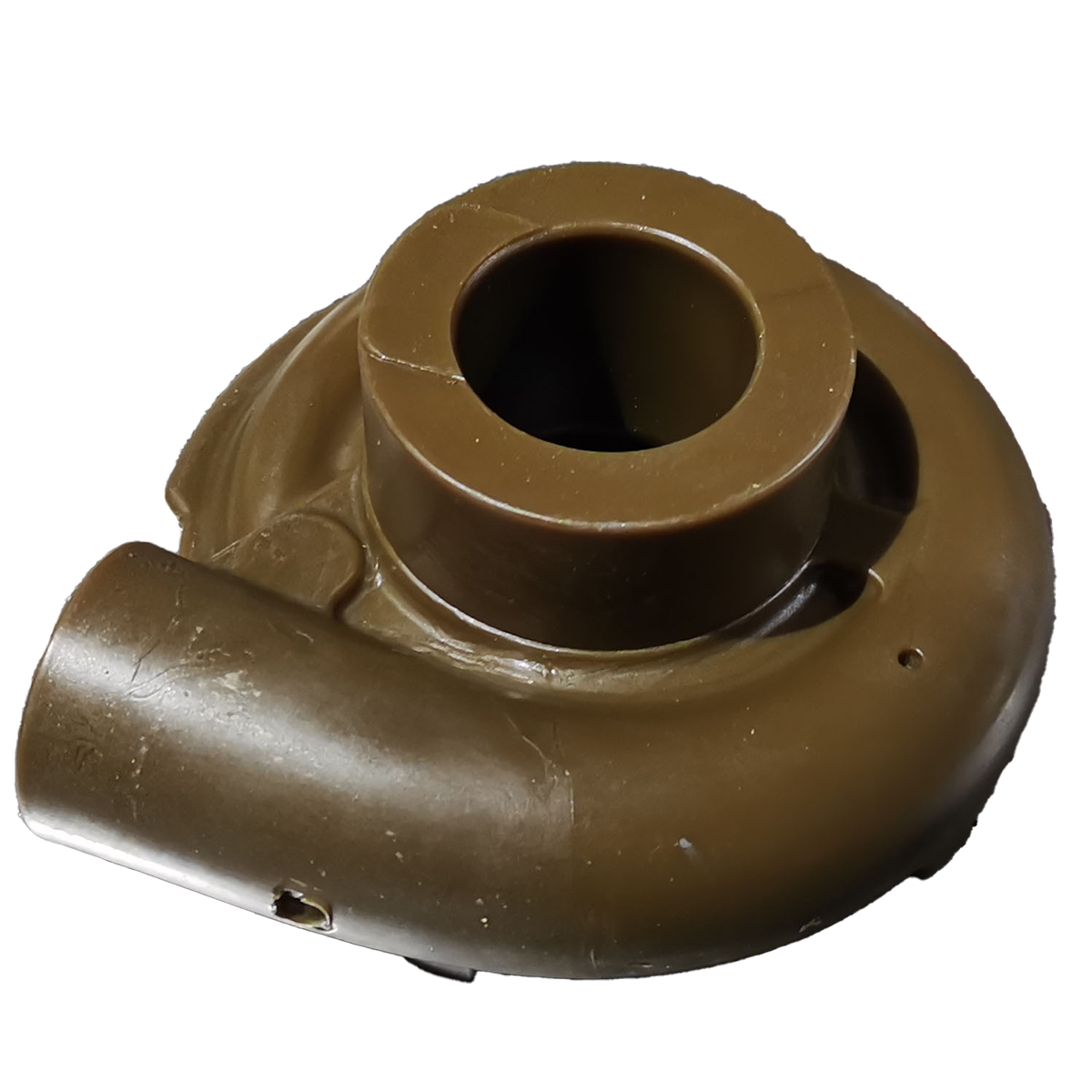
3. Material performance retention
Excellent material performance: AISI 316 stainless steel is a high-performance austenitic stainless steel with excellent corrosion resistance, heat resistance and mechanical properties. Through the investment casting process, these material properties can be retained to the maximum extent, ensuring that the turbine casing can still maintain stable operation under extreme working conditions.
4. Production efficiency and cost control
Production efficiency: The investment casting process can achieve one-time molding, reducing the subsequent processing and assembly steps, thereby improving production efficiency. At the same time, since the process can produce parts with complex shapes, it avoids steps such as split casting and welding in traditional casting methods, further improving production efficiency.
Cost control: Although the initial investment of the investment casting process is high, it can significantly reduce production costs in mass production because it can reduce the workload of subsequent processing and finishing, as well as improve production efficiency.