OEM custom vacuum casting products of grey iron and spheroidal graphite (SG) ductile nodular cast iron with heat treatment, surface treatment and CNC machining service.
Vacuum Casting is also called Negative Pressure Sealed Casting, Reduced Pressure Casting or V Process Casting. Vacuum pressure casting requires the use of air extraction equipment to extract the air inside the casting mold, and then use the pressure difference between the inside and outside of the mold to cover the heated plastic film on the pattern and template. The casting mold will become strong enough to withstand the molten metal during casting. After obtaining the vacuum mold, fill the sand box with dry sand without binder, and then seal the top surface of the sand mold with the plastic film, followed by vacuum to make the sand firm and tight. After that, remove the mold, put the sand cores, close the mold to make everthing ready for pouring. Finally, the casting is obtained after the molten metal is cooled and solidified.
Lost Foam Casting vs Vacuum Casting | ||
Item | Lost Foam Casting | Vacuum Casting |
Suitable Castings | Small and medium-sized castings with complex cavities, such as engine block, engine cover | Medium and large castings with few or no cavities, such as cast iron counterweights, cast steel axle housings |
Patterns and Plates | Foam patterns made by moldings | Template with suction box |
Sand Box | Bottom or five sides exhaust | Four sides exhaust or with exhaust pipe |
Plastic Film | The top cover is sealed by plastic films | All sides of both halves of sand box are sealed by plastic films |
Coating Materials | Water-based paint with thick coating | Alcohol-based paint with thin coating |
Molding Sand | Coarse dry sand | Fine dry sand |
Vibration Molding | 3 D Vibration | Vertical or Horizontal Vibration |
Pouring | Negative Pouring | Negative Pouring |
Sand Process | Relieve negative pressure, turn over the box to drop sand, and the sand is then reused | Relieve negative pressure, then the dry sand falls into the screen, and the sand is recycled |
Ductile cast iron, which is also called nodular cast iron, spheroidal graphite cast iron or just SG iron for short, represent a group of cast iron. Nodular cast iron obtains nodular graphite through spheroidization and inoculation treatment, which effectively improves the mechanical properties of the cast iron, especially the plasticity and toughness, so as to obtain higher strength than carbon steel.
Ductile iron castings have better shock absorption performance than carbon steel, while carbon steel castings have much better weldability. And to some extent, the ductile iorn castings could have some performances of resistanting wear and rust. So the ductile iron casting could be used for some pump housings or water supply systems. However, we still need to make precautions for protecting them from wearing and rust.
Ductile iron is not a single material but is part of a group of materials which can be produced to have a wide range of properties through control of the microstructure. The common defining characteristic of this group of materials is the shape of the graphite. In ductile irons, the graphite is in the form of nodules rather than flakes as it is in grey iron. The sharp shape of the flakes of graphite create stress concentration points within the metal matrix and the rounded shape of the nodules less so, thus inhibiting the creation of cracks and providing the enhanced ductility that gives the alloy its name. So generally speaking, if the ductile iron could meet your requirements, the ductile iron could be your first choice, instead of carbon steel for your castings.
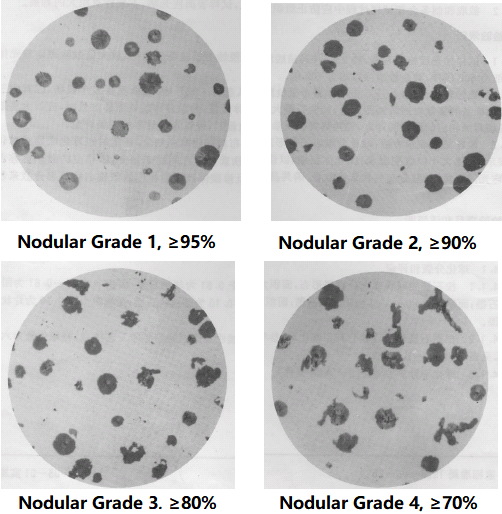