1. Hydrostatic Testing
Hydrostatic testing is a pressure test method that uses water as the test medium. It is usually used to test the pressure resistance and sealing of equipment such as pipelines, pressure vessels, boilers, storage tanks, pumps, etc. under working pressure.
Working Principle:
By filling the equipment or pipeline with water, gradually increase the water pressure to 1.5 to 2 times the design working pressure (usually there will be standard requirements), and keep it for a period of time (usually 30 minutes to a few hours) to observe whether there are leaks, expansion or other problems.
The key to hydrostatic testing is to ensure that the water does not contain bubbles during the test (no compressed air or gas is used), because the incompressibility of water makes leaks easier to find.
Advantages:
Water does not expand during the test, so it can produce a more realistic stress test effect.
Water is stable, easy to obtain and low cost.
Can better find small leaks.
Disadvantages:
Drainage and cleaning are required during the test, which may cause waste or additional operating troubles.
Not suitable for some equipment materials that are easily corrosive or affected by water.
Application scenarios:
Pressure testing of pipelines, boilers, storage tanks, etc.
Equipment inspection in industries such as oil, gas, and chemicals.

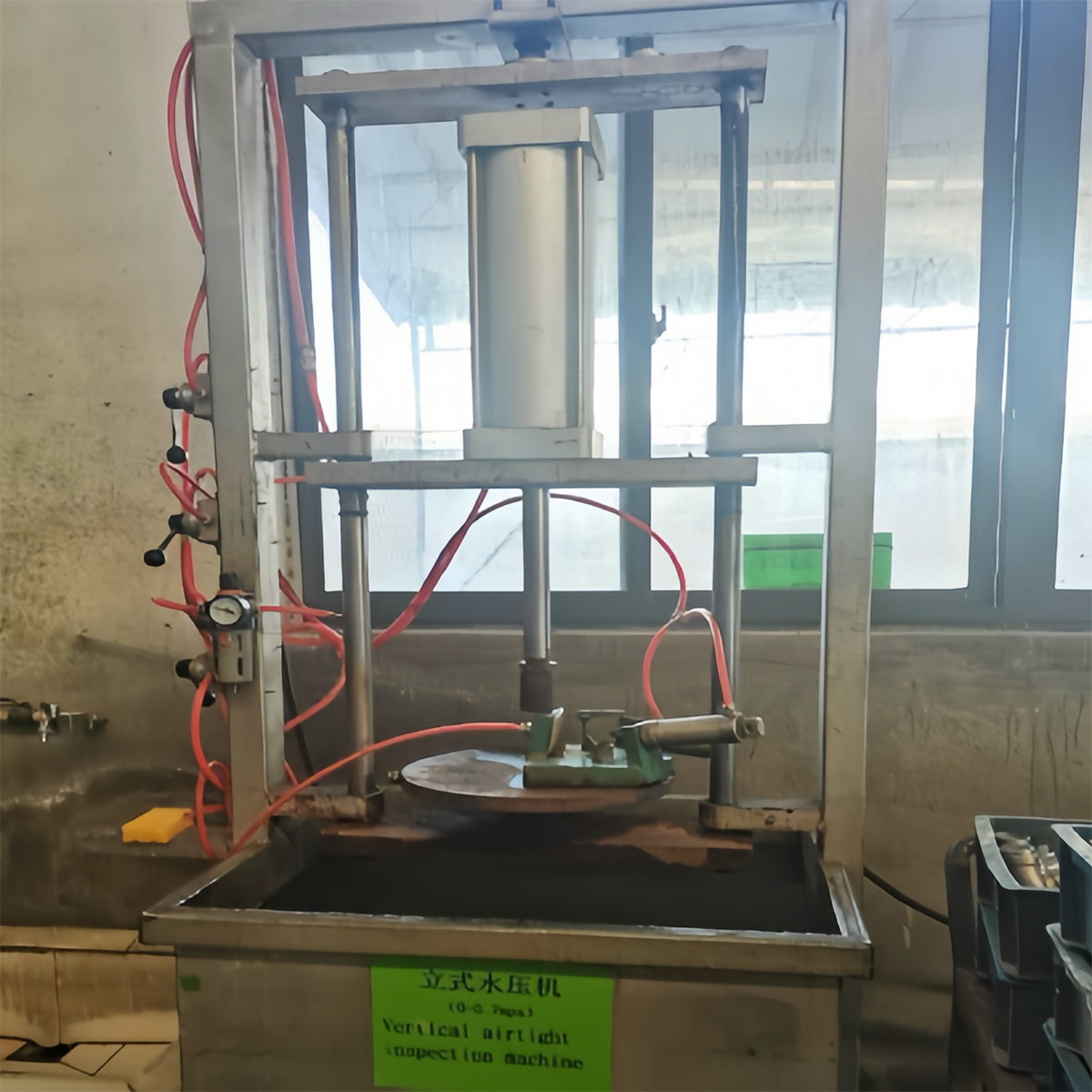
2. Pneumatic Testing
Pneumatic testing is a method that uses gas (usually compressed air or nitrogen) as the test medium. This test is often used for equipment that is not suitable for water or that needs to be tested at lower temperatures.
Working Principle:
Fill the equipment or pipeline with gas, gradually increase the pressure of the gas, and monitor the pressure gauge to ensure that the equipment can withstand the predetermined maximum working pressure.
During the test, you need to be particularly careful because the gas is highly compressible and may produce dangerous dynamics (such as explosive airflow) when it leaks.
Advantages:
The test process is simple and the equipment is easy to operate.
Equipment that is not suitable for water testing, such as electrical equipment, high-temperature containers, etc., can be tested.
No water needs to be discharged during the test, which can reduce environmental pollution.
Disadvantages:
Gas is highly compressible, and if a leak occurs during the test, it may pose a greater safety risk.
For small leaks, pneumatic testing may not be as intuitive and easy to find as water pressure testing.
Application Scenarios:
Testing of electrical equipment and pneumatic systems.
Equipment that is not suitable for water testing, such as certain high-temperature or low-temperature containers, chemical reactors, etc.
Safety inspection of gas pipelines or compressed gas systems.
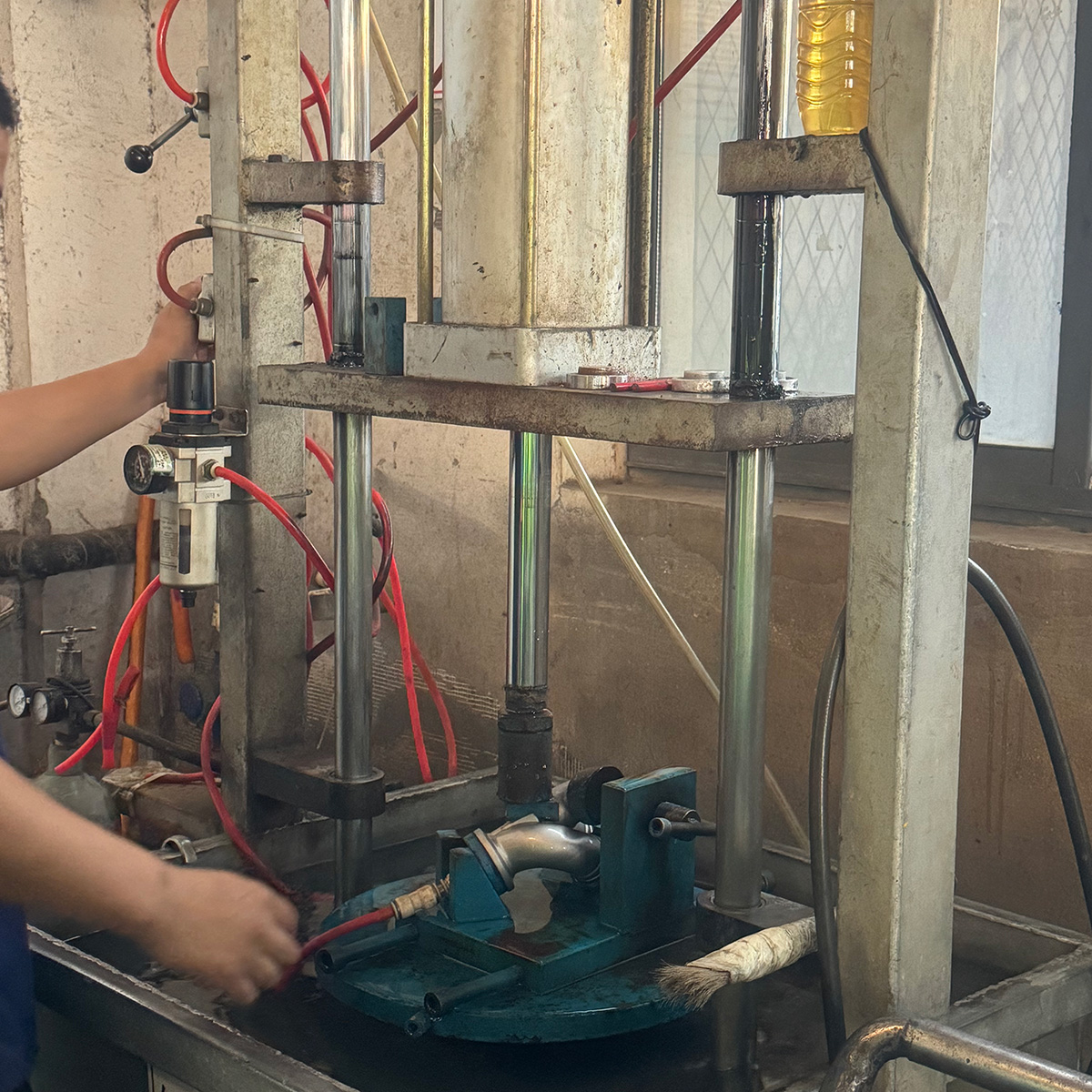

Post time: Dec-02-2024