The filling ability of molten metal, also known as fluidity, is a crucial factor in the casting process. It refers to the capability of molten metal to fill the mold cavity completely before solidification. Understanding and optimizing this property is essential for producing high-quality castings with intricate geometries and minimal defects.
Basic Concept of Filling Ability
The filling ability of molten metal determines how well the metal flows into and fills the intricate details of a mold. It is influenced by several factors including the metal’s composition, temperature, and the design of the mold. Good filling ability ensures that the final casting is free from defects such as misruns, cold shuts, and incomplete sections. This property is particularly important in the production of thin-walled castings and components with complex geometries.
Factors Influencing Filling Ability
1.Metal Composition: The chemical composition of the molten metal plays a significant role in its fluidity. Metals with lower melting points generally have better fluidity.
2.Temperature: The temperature of the molten metal is directly proportional to its fluidity. Higher temperatures decrease the viscosity of the metal, enhancing its ability to flow into the mold. However, excessively high temperatures can lead to increased oxidation and gas absorption, which can cause defects in the casting.
3.Mold Design: The design and material of the mold significantly impact the filling ability. A mold with smooth surfaces and appropriate gating systems facilitates better flow.
4.Pouring Rate: The rate at which molten metal is poured into the mold affects its ability to fill the cavity. A controlled and consistent pouring rate ensures that the metal maintains its temperature and flow characteristics, preventing premature solidification.
5.Additives: Certain additives can be introduced to improve the fluidity of molten metal. For instance, silicon is often added to aluminum alloys to enhance their fluidity, making them more suitable for complex castings.
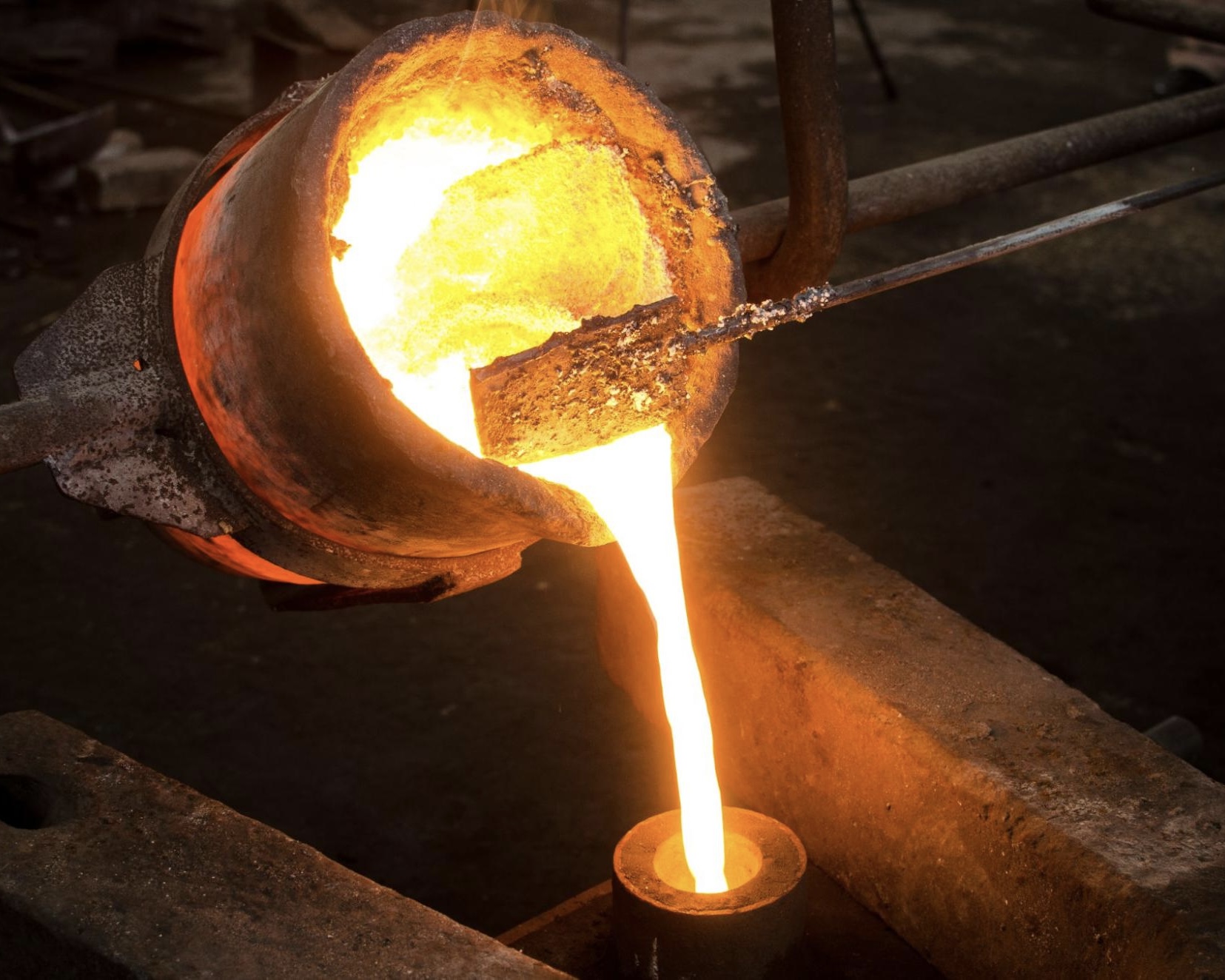
.jpg)
Measures to Improve Filling Ability
1.Optimal Alloy Selection: Choosing alloys with inherent good fluidity properties is the first step towards improving filling ability. For example, aluminum-silicon alloys are preferred for their superior fluidity and ease of casting.
2.Temperature Control: Maintaining the optimal temperature of the molten metal throughout the casting process is crucial. Preheating the mold and controlling the pouring temperature can significantly enhance fluidity. Utilizing temperature monitoring systems helps in achieving consistent results.
3.Improved Mold Design: Designing molds with smooth surfaces, adequate venting, and well-planned gating systems can facilitate better metal flow.
4.Use of Inoculants and Fluxes: Adding inoculants can refine the grain structure of the metal, improving its fluidity. Fluxes can also be used to remove impurities and reduce surface tension, enhancing the flow characteristics of the molten metal.
5.Degassing: Removing dissolved gases from the molten metal can prevent the formation of bubbles and voids, improving the overall filling ability.
6.Controlled Pouring Techniques: Utilizing automated pouring systems ensures a consistent and controlled flow of molten metal into the mold. This reduces the chances of turbulence and cold shuts, leading to better filling ability.
Post time: Nov-08-2024