Straightening of castings, also known as correction or rectification, is a crucial step in the manufacturing process to ensure that cast metal parts meet precise dimensional specifications and structural integrity.
Methods of Straightening
There are several methods employed to straighten castings, each suitable for different types of materials and casting shapes. The primary methods include:
Mechanical Straightening: This involves the application of external forces using mechanical tools and machines. Techniques such as pressing, bending, and hammering are common. Mechanical straightening is particularly effective for large and sturdy castings.
Thermal Straightening: In this method, heat is applied to specific areas of the casting to induce thermal expansion or contraction, thus correcting distortions. This method is advantageous for castings that are susceptible to cracking or breaking under mechanical stress.
Hydraulic Straightening: Utilizing hydraulic presses, this method applies controlled pressure to straighten castings. It offers high precision and is suitable for delicate and complex shapes that require careful handling.
Combination Methods: Often, a combination of mechanical and thermal straightening is employed to achieve the desired results, particularly in castings with complex geometries and varied material properties.
Classification and Selection of Straightening Equipment
The choice of straightening equipment depends on several factors, including the type of casting, material properties, and the extent of deformation. The main types of equipment are:
Manual Straightening Tools: Simple tools like hammers, anvils, and handheld presses are used for small-scale or minor corrections. They require skilled operators to achieve precise results.
Mechanical Presses: These include toggle presses, screw presses, and eccentric presses. They are suitable for medium to large castings and provide consistent force application. Mechanical presses are chosen for their reliability and ease of operation.
Hydraulic Presses: These presses offer high force capabilities and precise control over pressure application. They are ideal for straightening large, heavy, and complex castings. Hydraulic presses can be fitted with various dies and fixtures to accommodate different shapes and sizes.
Heat Treatment Furnaces: Used in thermal straightening, these furnaces allow for controlled heating of castings to induce stress relief and correction of deformations. They are essential for castings that cannot endure mechanical force.
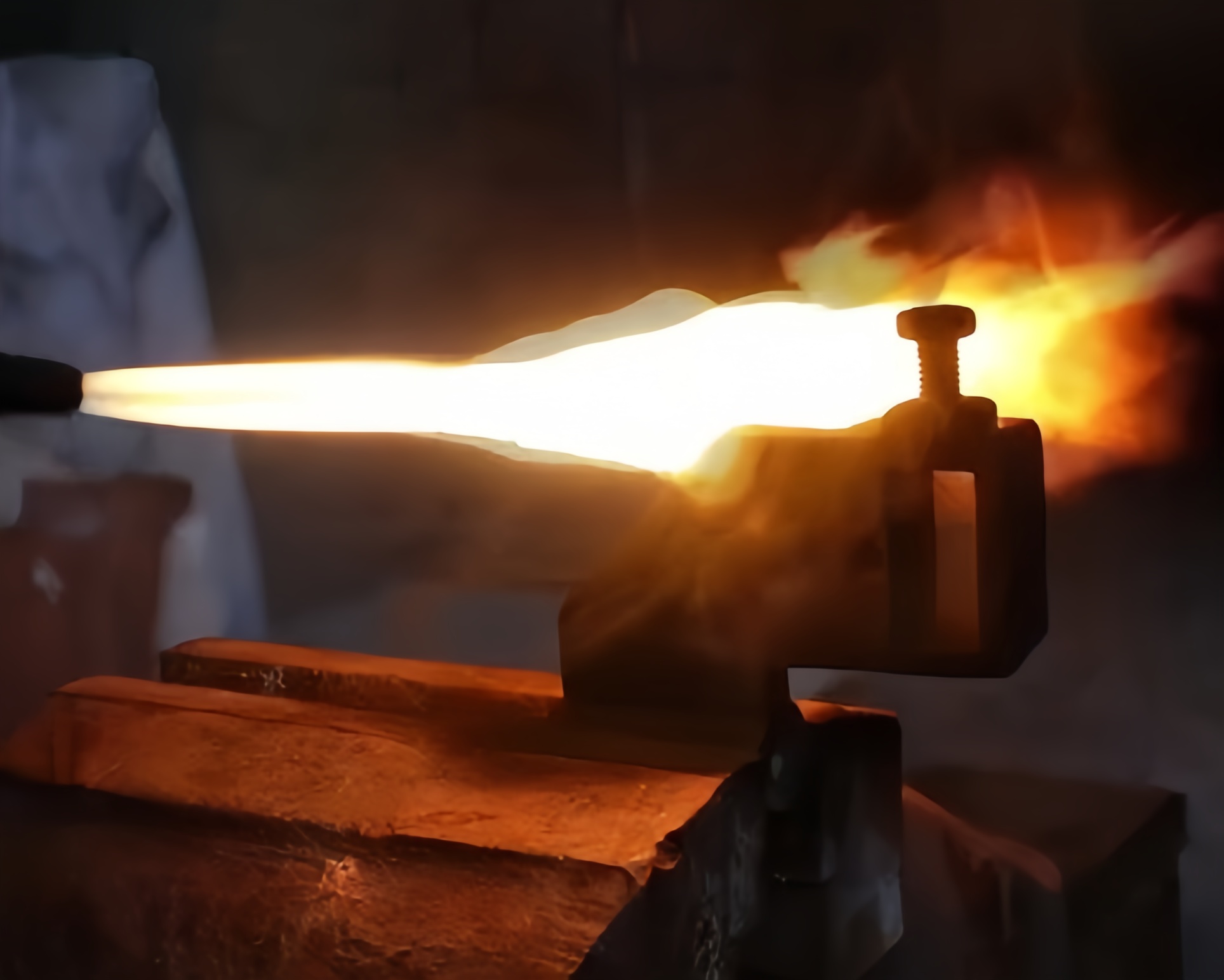
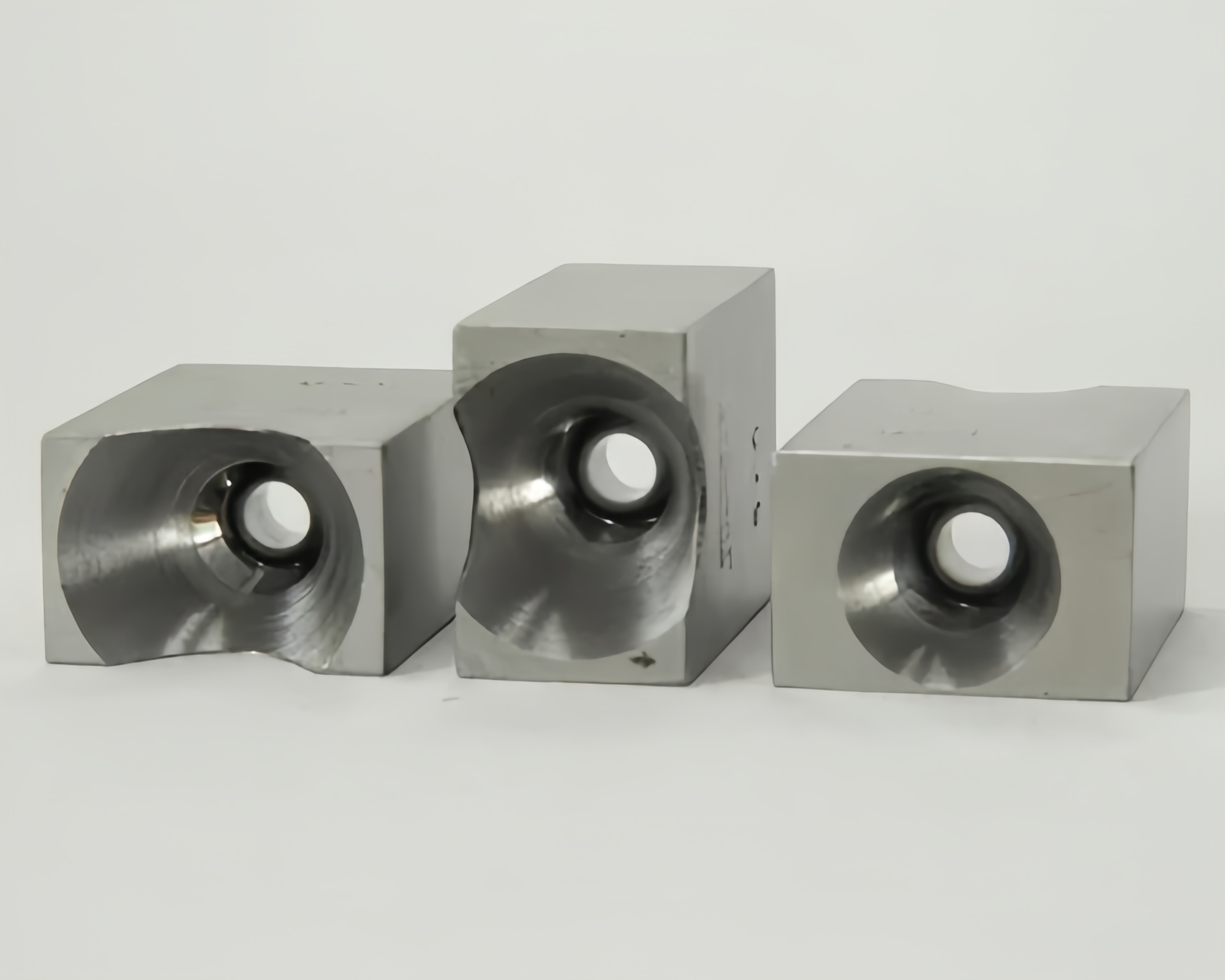
Straightening Dies
Straightening dies, also known as correction dies, are specially designed tools used in conjunction with presses to accurately reshape deformed castings. They are categorized based on their function and the type of casting they are used for:
Flat Dies: These are used for straightening flat surfaces and edges. They are simple in design but effective for correcting planar distortions.
Forming Dies: Designed to match the contour of the casting, these dies are used to correct complex shapes and curves. They are custom-made for specific casting designs and ensure precision in straightening.
Support Dies: These dies provide support and stabilization to the casting during the straightening process. They are crucial in preventing additional deformations or damage during correction.
The choice of straightening die is critical to achieving the desired results. It must match the casting’s geometry and the nature of the distortion to provide effective correction without inducing further stress or damage.
Straightening of castings is a vital process in ensuring the quality and functionality of metal parts. By employing the appropriate methods, selecting the right equipment, and utilizing precise straightening dies, manufacturers can correct deformations and produce castings that meet exacting standards. This not only enhances the performance of the final product but also extends its service life, ensuring reliability and customer satisfaction.
Post time: Oct-18-2024