Residual stress in metal castings is a significant issue that can affect the performance and longevity of metal components. Predicting and managing these stresses is crucial for ensuring the quality and durability of the final product.
Prediction of Residual Stress in Castings
Residual stress in castings can be predicted using computational methods such as finite element analysis (FEA). These simulations consider the thermal and mechanical processes during casting, including solidification and cooling.
Reducing the Formation of Residual Stress
To reduce the formation of residual stress in castings, several approaches can be employed. Controlled cooling is one method, where the casting is cooled at a uniform rate to prevent differential contraction. Optimizing the casting design to avoid sharp corners and thick sections can also help, as these areas are prone to higher stress concentrations. Additionally, modifying the alloy composition to achieve a more uniform solidification can reduce stress.
Detection of Residual Stress
Detecting residual stress in castings can be achieved through various non-destructive testing methods. X-ray diffraction (XRD) is a common technique that measures the spacing of crystal planes in the material to determine the stress state. Ultrasonic testing can also be used to detect changes in material properties indicative of stress. Strain gauges can be applied to measure surface strains directly.
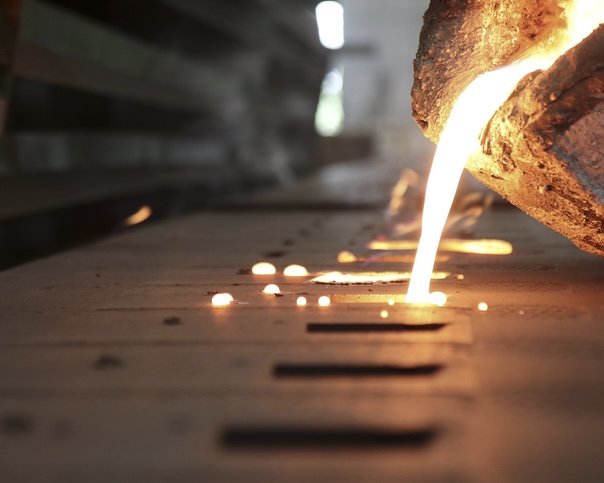
.jpg)
Stress Relief in Cast Iron Castings
To eliminate residual stress in cast iron, annealing is a widely used method. This involves heating the casting to a temperature below its melting point, holding it at that temperature to allow for stress relaxation, and then cooling it slowly. This process allows the internal stresses to be relieved without significantly altering the material properties.
Stress Relief in Steel Castings
For steel investment castings, stress relief annealing is also effective. The process is similar to that for cast iron, but the temperatures involved are generally higher due to the different thermal properties of steel. Controlled heating and cooling are critical to prevent the introduction of new stresses during the process.
Stress Relief in Non-Ferrous Alloy Castings
Non-ferrous alloys, such as aluminum and copper alloys, also require stress relief to enhance their performance. These materials are typically stress-relieved through thermal methods similar to ferrous metals but often at lower temperatures. Additionally, some non-ferrous alloys can benefit from mechanical stress relief techniques, such as vibratory stress relief, which uses mechanical vibrations to redistribute and relieve internal stresses.
Post time: Nov-22-2024