Negative pressure casting, also known as vacuum-sealed casting, reduced pressure casting, or V-method casting, is a process that uses vacuum pressure to cover a heated, plasticized plastic film over the pattern and template. Dry sand without any binder is then filled into the sand mold, and the top surface of the sand mold is sealed with plastic film. By creating a vacuum, the sand is compacted, the pattern is removed, cores are placed, molds are closed, and molten metal is poured until solidification forms the casting.
Characteristics of Negative Pressure Casting
1. High dimensional accuracy and clear contours: Since the pattern surface is covered with plastic film, there is no need for vibration or knocking during pattern removal. The vacuum compacts the sand mold, giving it high and uniform hardness, preventing deformation of the mold cavity under the heat of the molten metal. The negative pressure also aids in the smooth filling of molten metal. Investment casting can be combined with vacuum casting technology, and this combination is usually referred to as vacuum investment casting or negative pressure investment casting.
2. No binders or additives in the sand: The molding sand contains no binders, water, or additional materials, simplifying the sand processing steps.
3. Easy casting cleanup and low labor intensity: Cleaning castings is convenient, and fewer harmful gases are produced during pouring, making clean production easier and improving working conditions.
4. Wide range of applications: This method is suitable for both single-piece and small-batch production, as well as for mass production. It is especially effective for producing medium to large, precision, and thin-walled castings.

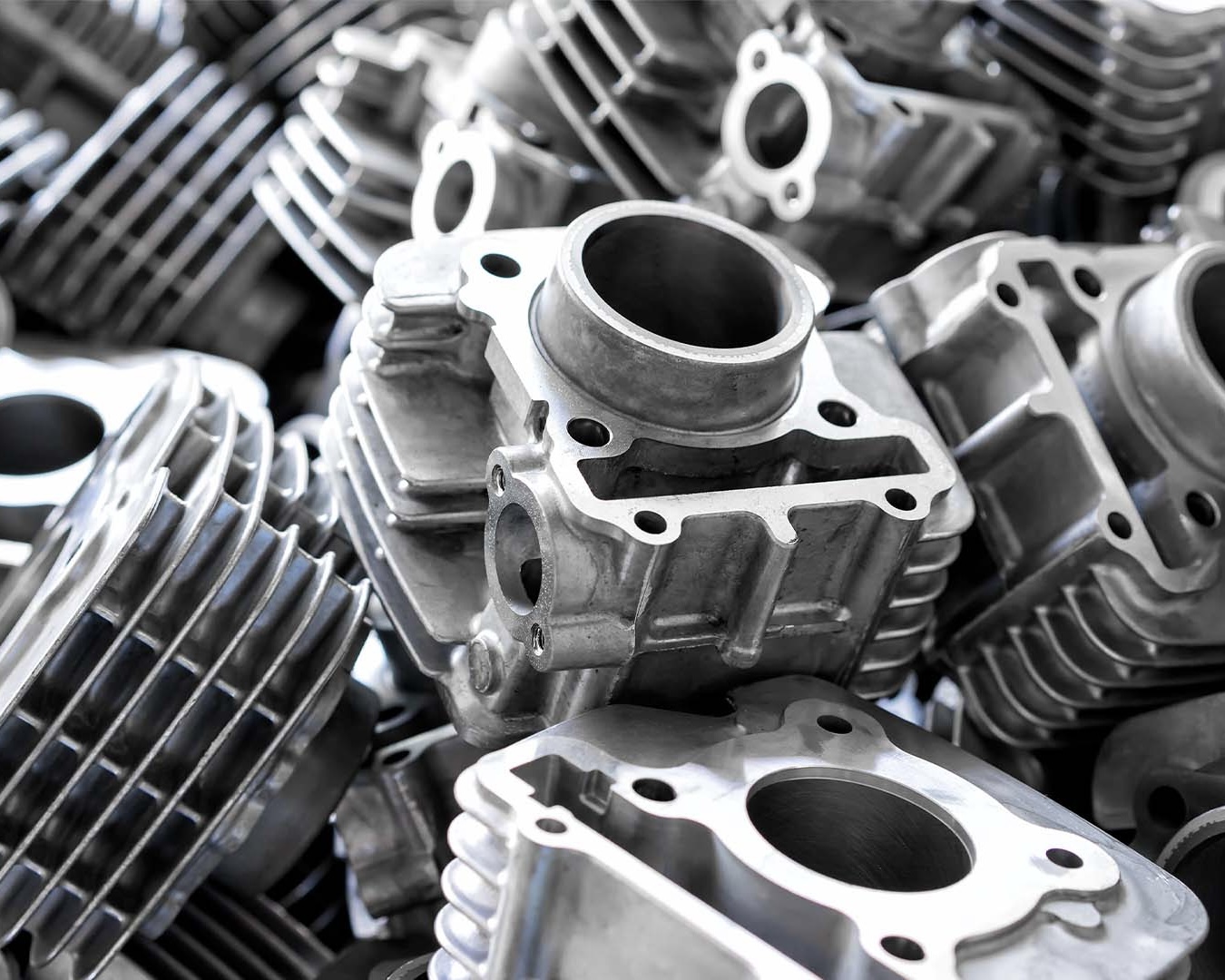
.jpg)
Molding Materials for Negative Pressure Casting
1. Plastic Film:
Plastic film is a crucial material in negative pressure casting. It is approximately 0.05–0.1 mm thick and must have good ductility. The surface should be free of scratches, impurities, or air bubbles. The film should not stick to the pattern, and when stretched and formed, it should produce minimal thermal stress. It must have no elasticity — meaning it cannot return to its original shape. Additionally, the film should produce minimal gas during thermal decomposition and be non-toxic, odorless, and low in ash content.
2. Molding Sand:
The quality of raw sand directly affects the strength of the sand mold, the vacuum suction capacity, and the surface roughness of the casting. Since dry sand is used in negative pressure casting, the gas emission is low, and the continuous vacuum process during pouring enhances the sand mold’s ventilation. However, due to the vacuum’s effect, molten metal can be drawn into the gaps between sand grains, causing mechanical sand adhesion. To achieve a smooth casting surface, fine sand is used.
3. Coating:
Applied after the plastic film is laid, the coating should not contain any materials that chemically react with the plastic film.
Post time: Mar-07-2025