Formation of shrinkage cavities and shrinkage
After the molten iron fills the mold, liquid shrinkage occurs immediately. At this time, shrinkage can be compensated from the pouring system. When the surface temperature of the cast iron part drops to the solidification temperature, the surface solidifies into a hard shell. After the ingrowth solidifies, if there is no riser to compensate for shrinkage, the molten iron in the hard shell will shrink in liquid state due to the drop in temperature during cooling. At the same time, the solidification shrinkage of the gradually thickening hard shell layer must be compensated. Although the solid hard shell reduces the size of the cast iron part due to the decrease in temperature, the liquid shrinkage and solidification shrinkage of the molten iron exceed the solid shrinkage of the hard shell. As the crystallization and solidification process proceeds, the hard shell continues to thicken. After the molten iron is completely solidified, shrinkage cavities are formed in the last solidified part of the cast iron part due to the lack of molten iron compensation.
During the solidification process, gray cast iron castings and ductile iron castings will also expand in volume with the precipitation of graphite. This expansion may offset part or all of the volume shrinkage formed in the early stage of solidification. If the mold rigidity is poor, under the action of graphitization expansion pressure, the mold wall will migrate outward, the size of the cast iron part will increase, the volume will also increase accordingly, and eventually the total volume of shrinkage cavities in the cast iron part will increase.
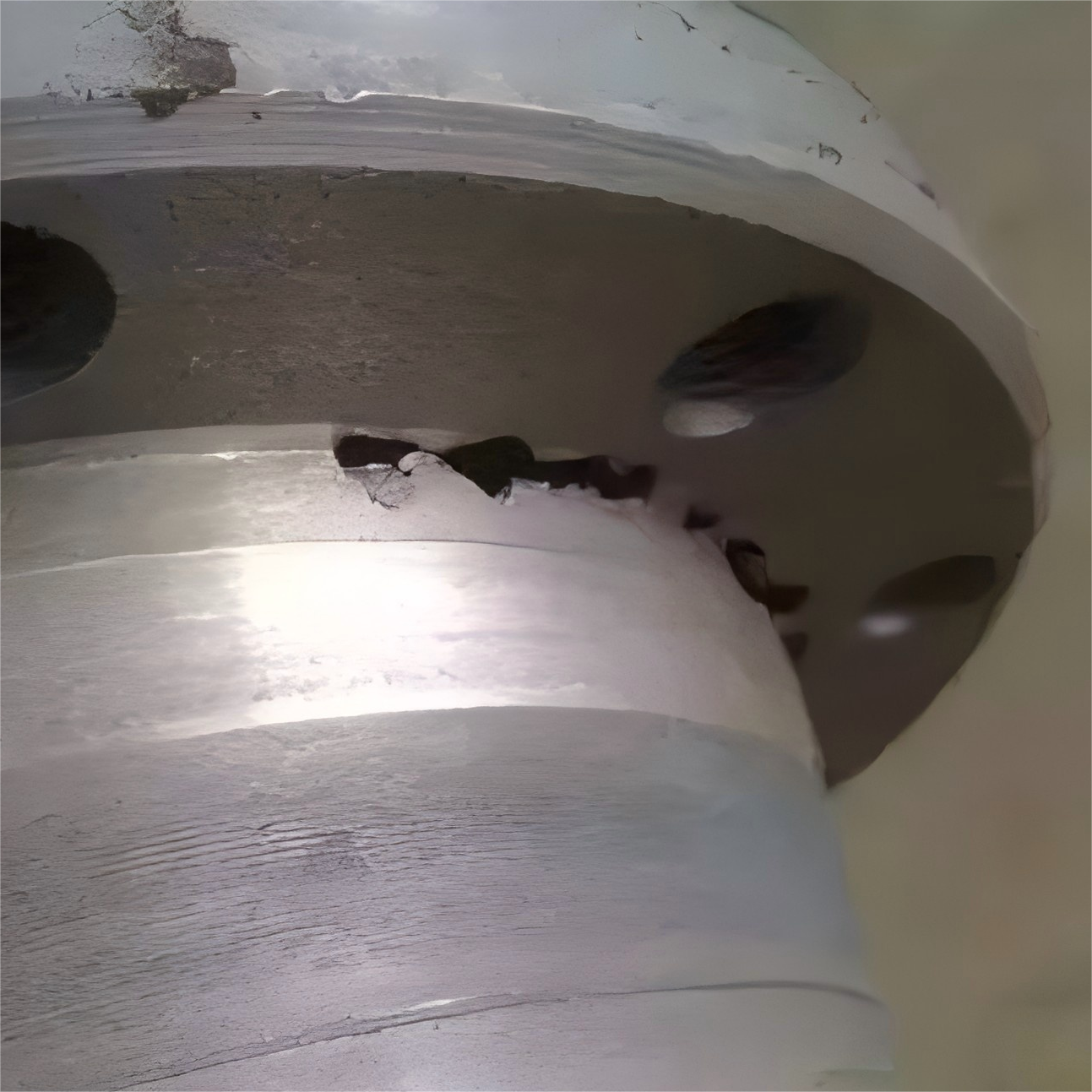
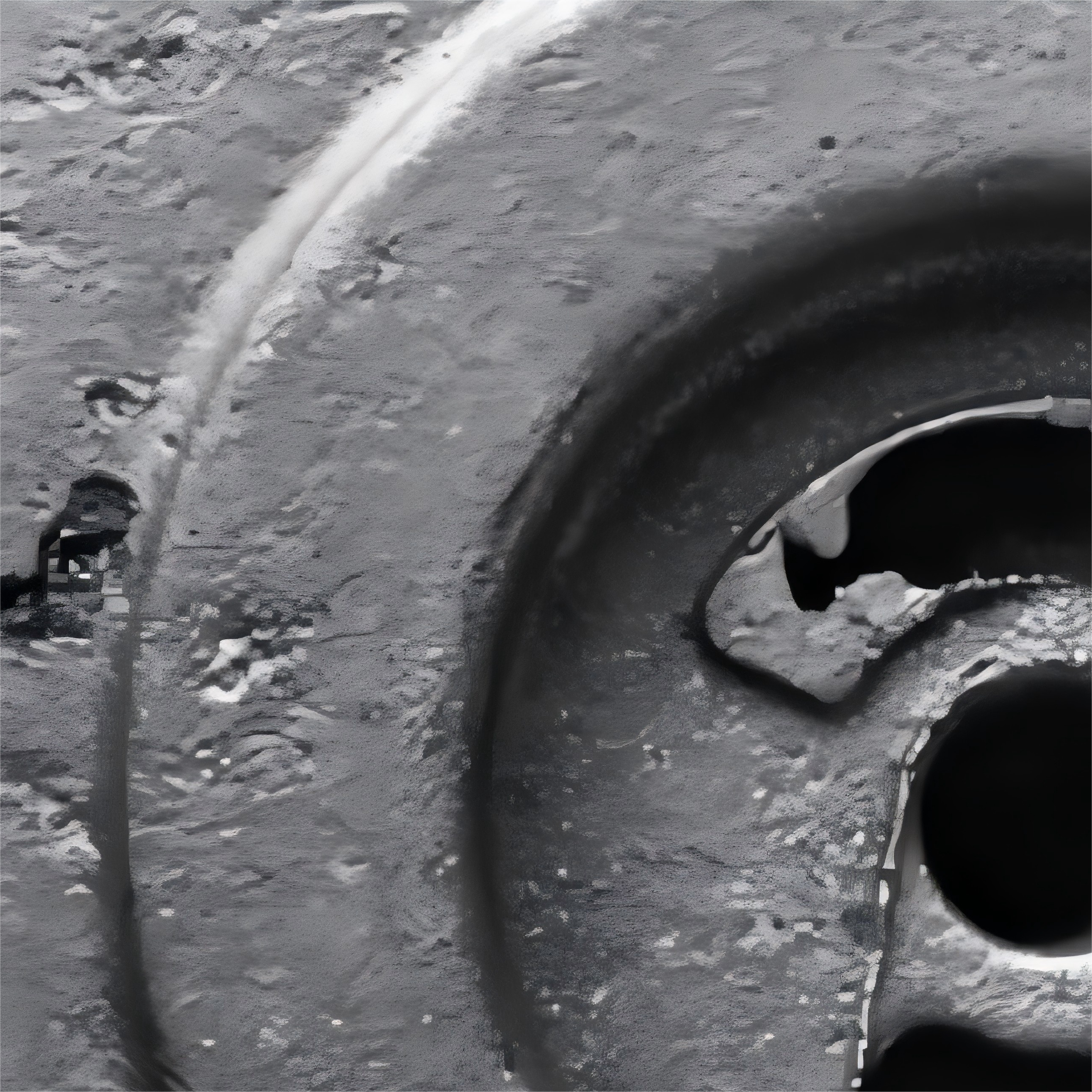
The basic reason for the formation of shrinkage is the same as that for the formation of shrinkage cavities, but the conditions for the formation of shrinkage cavities are: the crystallization temperature range or solidification area of molten iron is wide, tending to be a paste solidification mode; the temperature gradient on the cross section of the cast iron part is small, thus forming fine and dispersed shrinkage cavities.
The shrinkage and expansion at different times cannot offset each other and self-compensate, so that the graphitization expansion of the cast iron part cannot be fully utilized. If the cast iron part is not effectively compensated when shrinking, shrinkage cavities and shrinkage cavities will occur. Once the shrinkage defect is formed, the later graphitization expansion cannot offset it.
Compared with gray cast iron, ductile iron tends to "solidify in a paste-like manner", so there is a wider solidification area on the cross section of the casting, and it takes a longer time to form a solid shell; a considerable part of the graphite nodules grow surrounded by the austenite shell, and the expansion force of the graphite when growing can easily be transmitted to the casting shell through the contact of the austenite shell, thus showing a much larger eutectic graphitization expansion force than gray cast iron. Since magnesium and rare earth elements are added during the spheroidizing treatment, the white cast iron tendency is increased. At the same time, the size of the eutectic clusters of ductile iron is much smaller than that of gray cast iron, so it is difficult for the tiny gaps between the eutectic clusters to be fully compensated by the molten iron.
The above characteristics often cause ductile iron castings to show a large external dimensional expansion (the size of which depends on the rigidity of the casting mold) and a tendency to produce shrinkage cavities and shrinkage in actual production.
Post time: Mar-07-2025